Harvesting wind energy is an important part of the renewables mix, but when those huge turbine blades reach the end of their working lives, they could end up as waste in landfill. Siemens Gamesa has developed a recyclable blade that can be used to create new products when its wind-catching days are done.
Though other wind turbine components, such as towers and nacelles, can already be recycled, the composite materials used to manufacture the huge blades in commercial wind farm installations have proven more of a challenge, and often a costly one.
The key to the RecyclableBlades development from Siemens Gamesa is a new epoxy resin system that leverages proprietary Recyclamine technology from project partners Aditya Birla Advanced Materials.
"Unlike conventional materials, the recyclable resin system enables recycling of blade and recovery of reinforcement and the resin matrix," explained Siemens Gamesa in a journal post. "The recovered blade materials can be reused and repurposed, bringing them back into the system and closing the loop. Furthermore, the resin has been designed for extra slow reactivity to enable improved processability and cure faster than conventional materials, thereby contributing towards lowering cycle time in blade manufacturing."
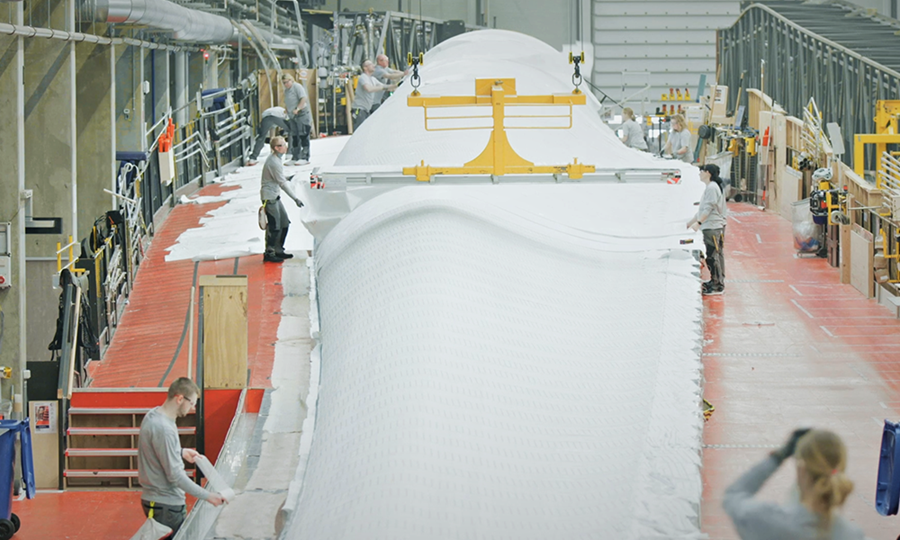
At the end of a turbine blade's service life, the resin, fiberglass, wood and other materials used to produce the RecyclableBlade would be separated using a mild acid solution, after which they can go on to be used in the production of new products such as suitcases or flat-screen casings.
Following validation testing and pilot trials, the first RecyclableBlades developed by Siemens Gamesa at a facility in Aalbor, Denmark, were manufactured in Hull, UK, last year.
Now the first turbine rocking 81-m (266-ft)-long RecyclableBlades is undergoing testing in operational conditions while also producing electricity at the Kaskasi offshore wind farm in the North Sea. This installation is operated by RWE Renewables and is expected to have 38 Siemens Gamesa 8.0-167 DD turbines harvesting wind energy by the end of this year with an installed capacity of 342 MW.
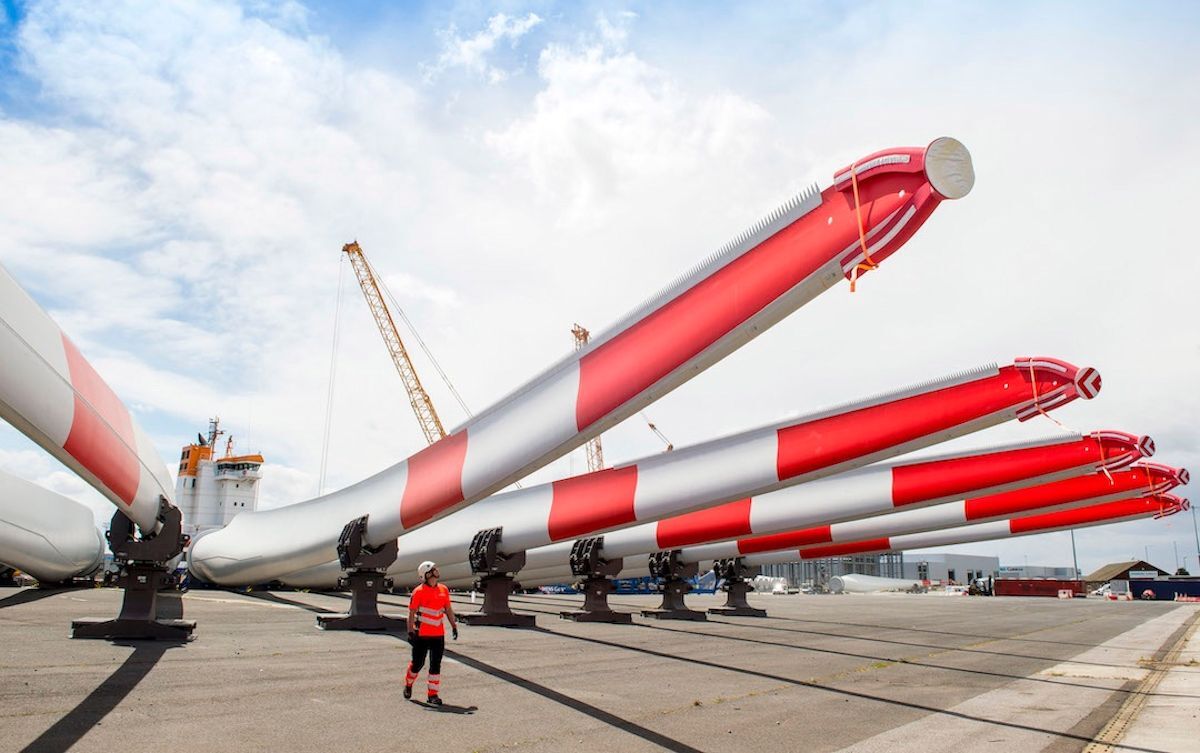
"We’ve brought the Siemens Gamesa RecyclableBlade technology to market in only 10 months: from launch in September 2021 to installation at RWE’s Kaskasi project in July 2022," said CEO of Siemens Gamesa's Offshore Business Unit, Marc Becker. "This is impressive and underlines the pace at which we all need to move to provide enough generating capacity to combat the global climate emergency. This milestone marks a significant contribution to Siemens Gamesa’s target of having fully recyclable turbines by 2040. With RecyclableBlade available for our customers, we can create a virtuous circular economy."
More turbines at the Kaskasi wind farm are expected to be fitted out with B81 RecyclableBlades in the near future, and Siemens Gamesa also reports that the technology can be scaled up to produce 108-m (354-ft)-long blades for the company's 14-222 DD turbines and 115-m (377-ft)-long blades for its 14-236 DD turbines. There's talk of future projects utilizing the development with the EDF Group and WPD Offshore as well.
Source: Siemens Gamesa