Desktop Metal – remember the name. This Massachussetts company is preparing to turn manufacturing on its head, with a 3D metal printing system that's so much faster, safer and cheaper than existing systems that it's going to compete with traditional mass manufacturing processes.
We've been hearing for years now about 3D printing and how it's going to revolutionize manufacturing. As yet, though, it's still on the periphery.
Plenty of design studios and even home users run desktop printers, but the only affordable printing materials are cheap ABS plastics. And at the other end of the market, while organizations like NASA and Boeing are getting valuable use out of laser-melted metal printing, it's a very slow and expensive process that doesn't seem to scale well.
But a very exciting company out of Massachusetts, headed by some of the guys who came up with the idea of additive manufacture in the first place, believes it's got the technology and the machinery to boost 3D printing into the big time, for real.
Desktop Metal
Desktop Metal is an engineering-driven startup whose founders include several MIT professors, and Emanuel Sachs, who has patents in 3D printing dating back to the dawn of the field in 1989.
The company has raised a ton of money in the last few months, including some US$115 million in a recent Series D round that brings total equity investments up over US$210 million. That money has come from big players, too, including Google Ventures.
The hype is real. And if Desktop Metal delivers on its promises – that it can make reliable metal printing up to 100 times faster, with 10 times cheaper initial costs and 20 times cheaper materials costs than existing laser technologies, using a much wider range of alloys – these machines might be the tipping point for large scale 3D manufacturing.
The company is putting forward two systems: a studio system aimed at rapid, cheap metal prototyping for engineering groups, and a production system for mass manufacture.
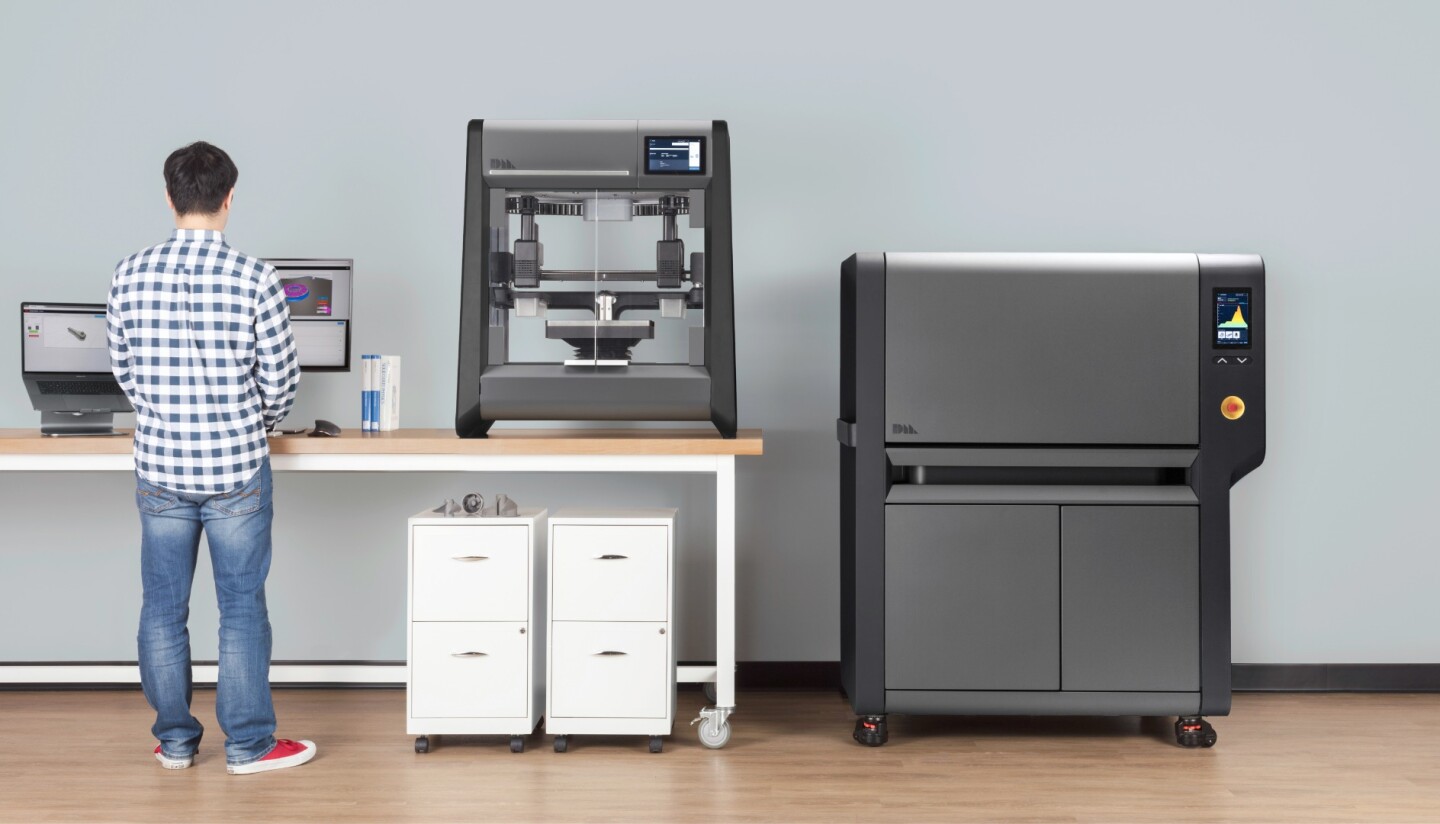
The Studio System: Rapid prototyping
Coming in at some 10 times cheaper than equivalent laser systems, Desktop Metal's Studio machines are also a ton more practical to have in an office. Without hazardous (and sometimes explosive) metal powders to deal with, or dangerous lasers, you can stick them pretty much anywhere without needing to install ventilation or make your workers wear respirators.
Indeed, having the Studio system around is much more like a regular old FDM (fused deposition modeling) ABS plastic printer than any other metal printing machine. It's very low maintenance and requires no special support equipment or staff.
The metals arrive in rod form, bound to a polymer binding agent and shipped in cartridges. But there's a ton of metal options – basically anything you can use in a Metal Injection Molding (MIM) system. That includes 4140 chromoly steel, aluminum, copper, bronze, a range of stainless steels, Hiperco 50 magnetic, titanium, and more than 200 other alloys.
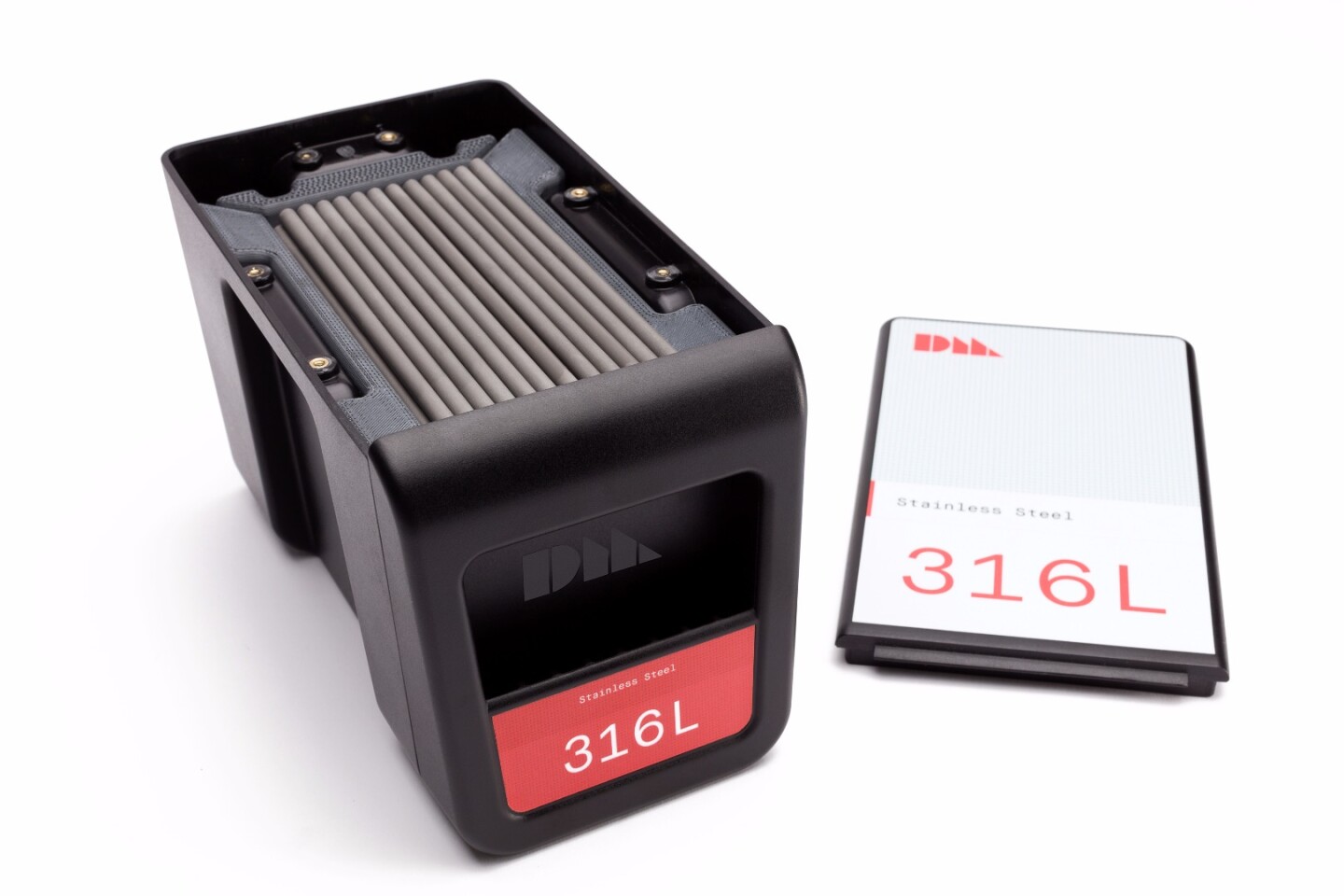
The Studio printer runs around and prints parts into layers of bound metal. The parts then go into a de-binding bath that removes a good portion of the binding polymer, and then the parts go into a sintering furnace.
The furnace is the special sauce in the Desktop Metal process. It uses a combination of regular heating elements and microwave heating to bring the part up to a temperature just below its melting point, where the binding agent burns off and the metal particles within fuse to their neighbors to produce a highly dense, sintered metal.
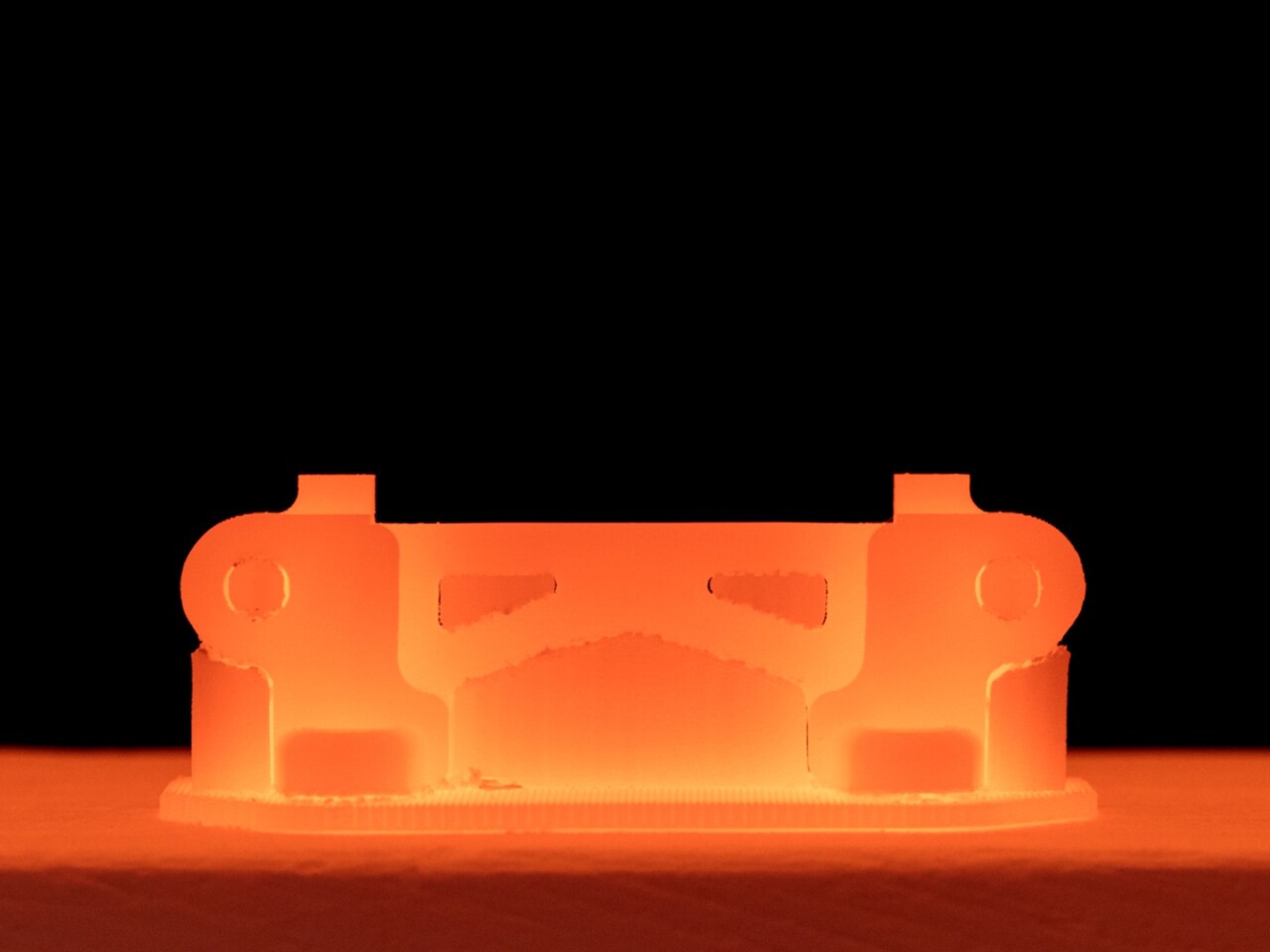
Timing and temperature are managed automatically by the system, depending on the design and the metals you've used. Parts also shrink up to 15 percent during the debinding and sintering process – but again, that's all automatically managed by the system. All you need to do is feed in the end design and all that business is handled.
At the end of the process, you basically poke out the support sections with a screwdriver. They're not welded to the part, and in many cases can be broken off by hand.
Depending on the nature of the part, it might be necessary to do some post-print surface finishing like sanding or bead blasting to smooth out the layered surfaces, but effectively you're left with a prototype part, produced quickly, in the production material and ready for testing. And parts are around 99.8 percent dense, which is huge. They're very mechanically tough.
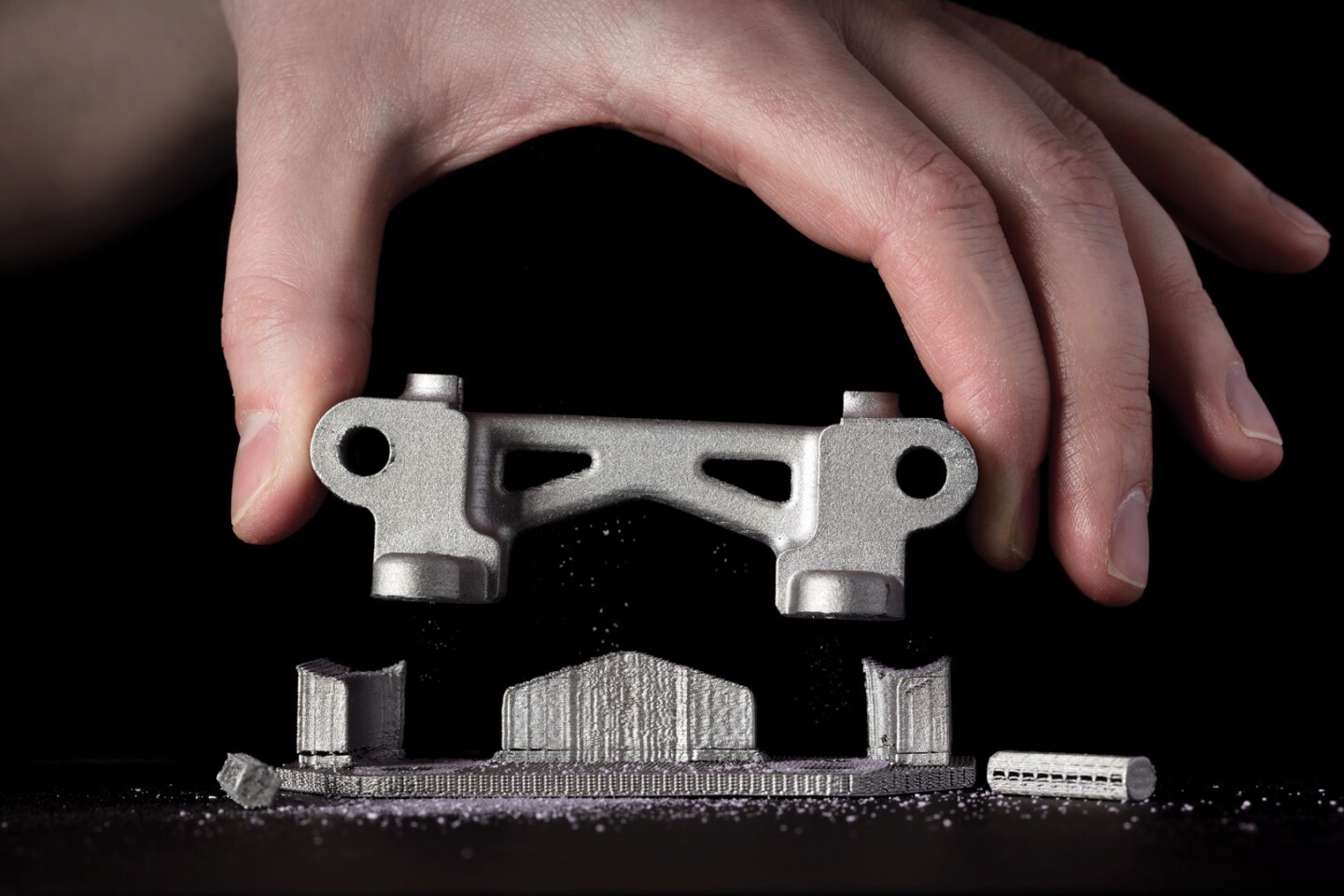
The Studio system makes rapid, affordable metal prototyping much more accessible than ever before, using a huge range of cheap, safe and easily handled materials and producing high-quality parts that can be tested properly. The entire integrated system and associated software retails for US$120,000, where an equivalent laser system will run you more than US$1 million – and that doesn't take into account the safety and materials handling overheads the laser systems require.
That's a massive step forward in prototyping, and the Studio system will begin shipping this year. But the production system, which will debut in 2018, is where the real revolution could lie.
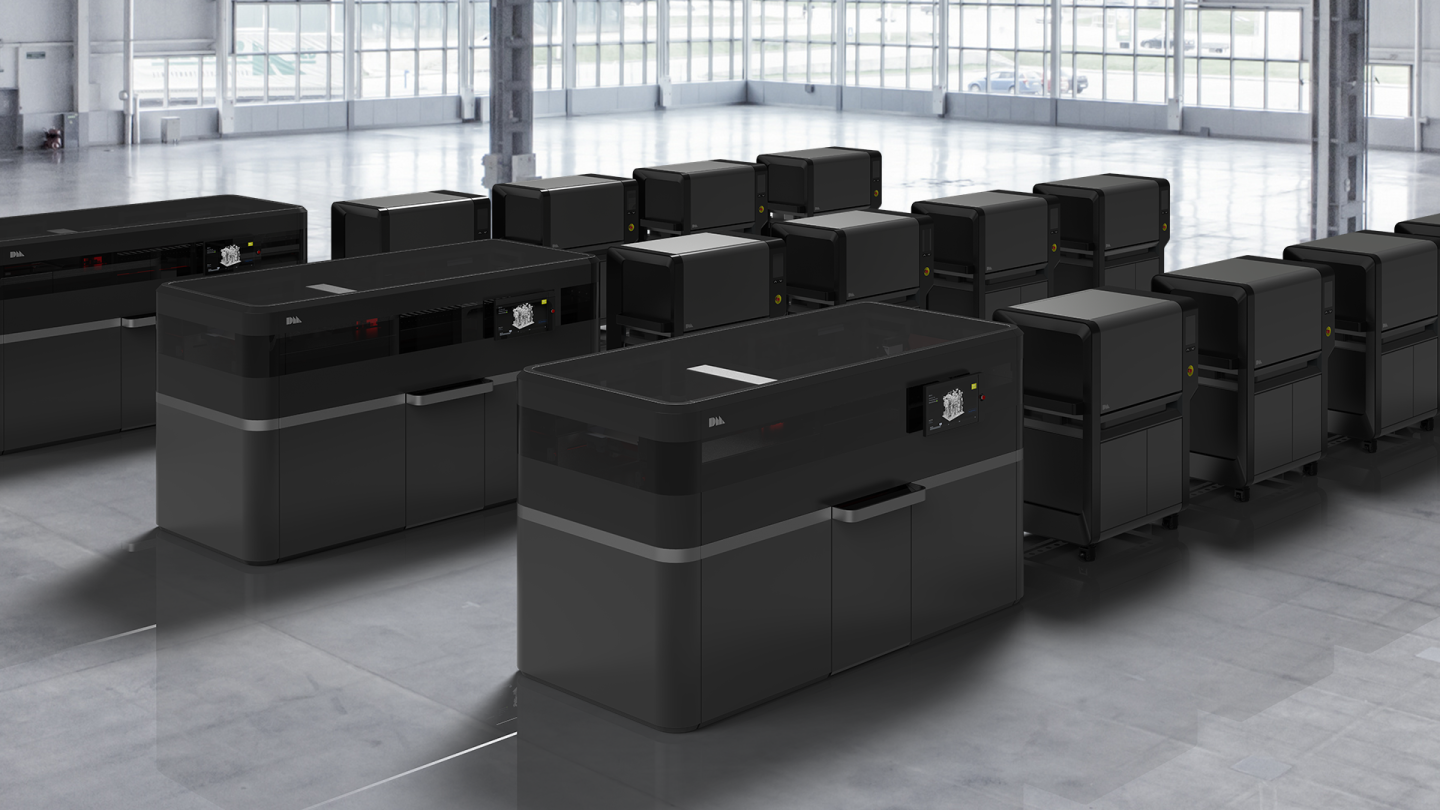
The Production System: Mass manufacture
The production system is built for speed, to a degree that has never been seen before. Faster than machining, casting, forging or any other technique, each production printer can produce up to an incredible 500 cubic inches of complex parts per hour. That's 100 times quicker than a laser-based alternative, with zero tooling.
Indeed, it prints faster than those hybrid microwave furnaces can sinter. To reach the full production speed, you'll need up to four furnaces per printer.
The Production printers use a different process called Single Pass Jetting, explained in the video below.
Instead of bound metal rod cartridges like the Studio printer uses, the Production machines use powders, which are bonded together during printing by spray-jetted droplets of a binder solution. They use regular, low-cost, easily available MIM powders. That's another huge advantage over laser machines, which need expensive powders with very precise particle sizes. Material costs here will be up to 20 times lower.
This, combined with the lack of tooling and job setup costs, can bring 3D printed metal parts down cheap enough to compete with traditional manufacturing processes for the first time.
The rest of the process – de-binding and sintering – looks much the same as the Studio system. Print resolution is as fine as 50 microns, roughly the width of a human hair. And while no final pricing has been given yet on the full system, each printer will retail for around US$360,000.
It's hard to overstate what a leap forward the Desktop Metal system represents. It's orders of magnitude faster than the current state of the art. It uses vastly cheaper materials that already exist in commercial quantities thanks to Metal Injection Molding. And the printers themselves are massively cheaper, too.
It's safe, simple and highly automated, and it's designed to make 3D printing as cost-effective as traditional manufacturing. It could be the tipping point that opens the door to radical 3D-printed design elements in mass market products.
This could be huge, folks. Hold on tight!
More information: Desktop Metal