How do you stop bullets using the lightest material possible? This question has inspired a string of fascinating breakthroughs from material scientists in pursuit of advanced lightweight armor that keeps foot soldiers agile and vehicles light. Yet another comes from researchers at North Carolina State University, who have developed a new type of bulletproof material comparable in performance to conventional armor, at just half the weight.
The team behind the breakthrough was also responsible for an impressive bit of research in 2015, which led to a new kind of lightweight shielding with the ability to block X-rays, gamma rays and neutron radiation. A year later, it adapted its approach to produce a high-strength shielding capable of stopping bullets in their tracks. Other research groups have had similar success using graphene.
At the heart of all this is what is known as a composite metal foam (CMF). This can be made by bubbling gas through molten metal to produce a frothy mixture, which can then be cooled to form a lightweight matrix and embedded with hollow, metallic spheres. The result is a material much lighter than conventional metals but with comparable strength.
This time around the team led by Afsaneh Rabiei, a professor of mechanical and aerospace engineering, used this approach to produce a steel CMF embedded with steel spheres. This was then sandwiched in between a ceramic faceplate and a thin aluminum back plate and blasted with rounds of bullets to see how it stood up.
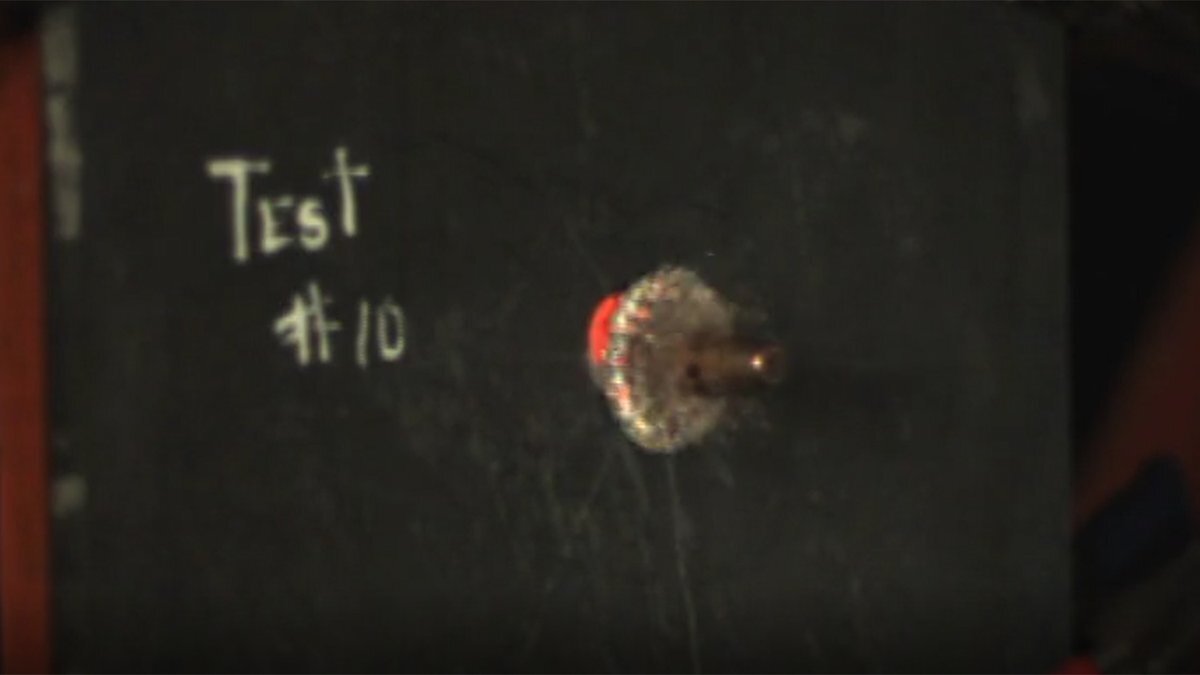
The projectiles used were .50 caliber ball and armor-piercing rounds, which were blasted into the armor at speeds between 500 and 885 meters per second (1,640 and 2,900 ft/s). The material was able to absorb 72-75 percent of the kinetic energy of the ball rounds and 68-78 percent of the armor-piercing rounds. In some of the tests, the blasts left no indentations on the back plate.
"The CMF armor was less than half the weight of the rolled homogeneous steel armor needed to achieve the same level of protection," says Rabiei.
The team imagines this material making its way onto armored vehicles for the military, helping to reduce their weight and therefore improving fuel efficiency. The researchers imagine that with further work, they could produce CMF-based materials with even greater performance.
"These findings stem from testing armors we made by simply combining steel-steel CMF with off-the-shelf ceramic face plates, aluminum back plate and adhesive material," says Rabiei. "We only optimized our CMF material and replaced the steel plate in standard vehicle armor with steel-steel CMF armor. There is additional work we could do to make it even better. For example, we would like to optimize the adhesion and thickness of the ceramic, CMF and aluminum layers, which may lead to even lower total weight and improved efficiency of the final armor."
You can see footage from some of the team's testing below, while the research was published in the journal Composite Structures.
Source: North Carolina State University