Driving a car in the country at night can be a scary. The combination of poor visibility and animals or other hard to spot obstacles on the road poses an obvious threat to both the car and its occupants. Some luxury models now have the option of forward looking infrared (FLIR) night vision systems, so you can see the animal in time to swerve. Unfortunately these systems are pricey, even as an aftermarket add-on, but that may soon change through the work of researchers at the Fraunhofer Institute for Mechanics of Materials (IWM) in Freiburg, Germany. The researchers have invented a way of bringing down the cost of the infrared lenses in FLIR systems down by 70 percent - opening the way to cheap FLIR cameras for the mass market.
FLIR night vision devices are based on microbolometers, which are a kind of room-temperature heat detector. Arrays of these in the FLIR camera use infrared light to detect animals by their body heat. This body heat may be used to create thermal images on a screen or simply to activate an alarm. Microbolometers are very useful devices, but they cost a fortune because of the infrared lenses used in their construction. In order for microbolometers to see wider application, the cost has to be brought down.
Currently, lenses are made of crystalline materials like germanium, zinc selenide or zinc sulfide. These are very expensive and require costly grinding and polishing, so the IWM team went in search of a cheaper material that used cheaper processing. The key to this was replacing traditional material with amorphous chalcogenide glass. This is glass that contains cheaper elements like sulfur, selenium or tellurium and is commonly used in lasers and CDs and DVDs.
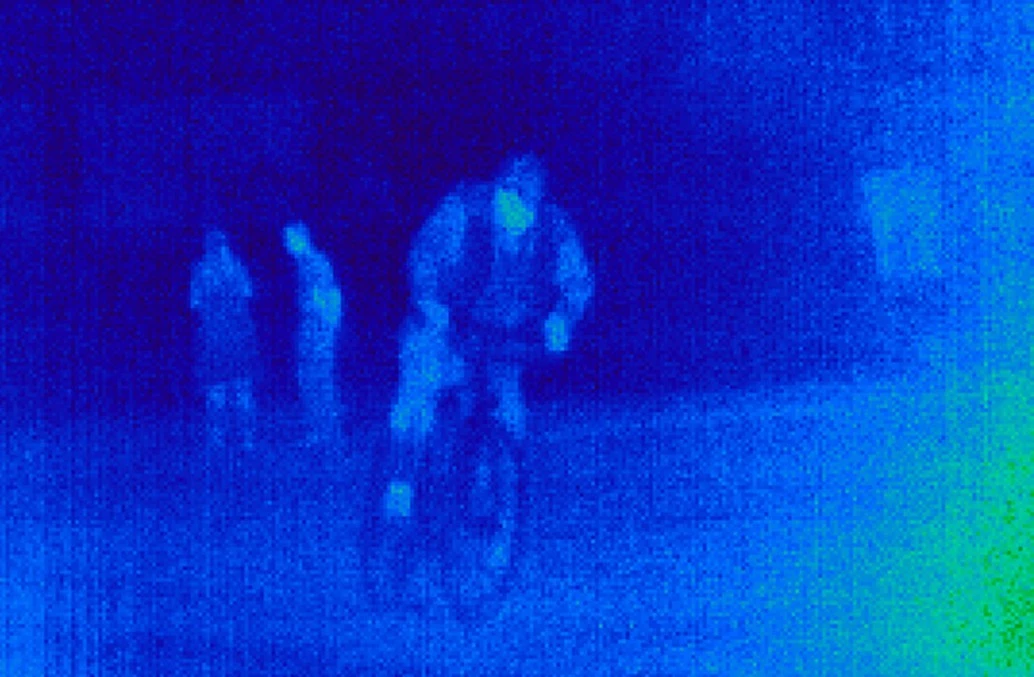
“Its softening temperature – that is, the temperature at which it can be formed – is low. Therefore, we can form it using non-isothermic hot stamping,” says Dr. Helen Müller, scientist at IWM.
“Non-isothermic hot stamping” means that instead of grinding and polishing, the lens are formed in a press that researchers describe as a “waffle iron.” Two heated plates contain a lens mold. The hot glass is clamped between these and then allowed to cool. When removed, there is a perfect lens that has the same optical qualities as a ground and polished one.
And it’s 70 percent cheaper.
The researchers are now working on adapting the process for mass production and are looking forward to the time when microbolometers are cheap enough to move out of the car market and into everyday life. They envision applications such as monitoring devices to assist the elderly, temperature monitoring in manufacturing and improving energy conservation by finding heat leaks in buildings.
Source: Fraunhofer