Researchers at MIT and Stanford have found a new way to transform waste heat into electricity, particularly in situations where the temperature gradient is small, below 100º C (180° F). The technology uses widely available materials, and could be used to recycle the large amounts of wasted heat generated in industrial processes and electric power plants.
According to the US Environment Protection Agency (EPA), one third of the industrial energy consumption in the United States is wasted as heat. If we could get even a small portion of it back, we'd be able to decrease power consumption significantly.
Scientists have turned to thermoelectric materials, which can generate electricity from a temperature gradient, as a possible solution. However, there are two problems with that approach: firstly, they are mostly made from rare materials, meaning they are expensive and can't be scaled up for industrial applications; and secondly, when the waste heat is only tens of degrees hotter than the surrounding environment, which is very common, their efficiency of thermoelectric materials is of only about 0.5 percent.
Researchers at MIT and Stanford led by Prof. Gang Chen have devised an alternative approach that takes advantage of the thermogalvanic effect, which describes a peculiar relationship between the temperature of a battery and the voltage at which it can effectively be charged up.
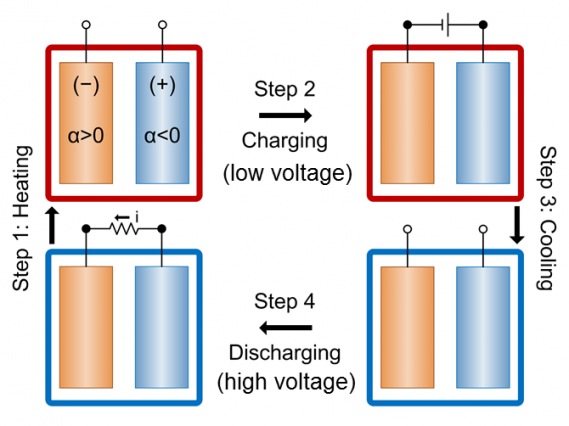
The scientists built a system that allows waste heat to first raise the temperature of a battery. Because of the thermogalvanic effect, the battery can now be charged at a lower voltage than would normally be required. The battery is then allowed to cool down, and at this point its lower temperature allows it to be discharged at a higher voltage, releasing more energy than was put into it through the electric grid. The difference in energy was gathered from waste heat.
The idea to harness the thermogalvanic effect to generate electricity was first proposed in the 50s, where it demonstrated efficiencies of up to 50 percent of the Carnot limit.
Compared to the original system, Chen and colleagues have achieved the capability to harness much smaller differences in temperature with relatively high efficiency (a difference of 50° C (90° F), with 5.7 percent efficiency) and the use of commonly available materials, such as copper, that could easily work at scale. Finally, their system could be manufactured quite easily, as it fits very well into the existing production chains of the battery industry.
The researchers will now turn to tackle the remaining challenges – namely, the low power density of 1.2 W/kg compared to thermoelectric materials, the speed of battery cycling of about one hour, and the need for extensive testing to ensure a useful operating life.
A paper describing the results appears in the journal Nature Communications.
Source: MIT