From science fiction to science fact: Vitaly Bulgarov's work on Hollywood sci-fi blockbusters gave him a unique perspective to tackle his greatest work – a 13-ft tall, walking robot mecha suit with arms that mimic the motions of a human pilot.
Science fiction has long been a driving force behind technological development. Imagination and inspiration leading to engineering and problem solving. And you'd be lucky to find a clearer case of sci-fi driven development than the Method-1 mecha suit that Hankook Mirae Technologies is building.
It stands 13 ft (3.9 m) tall, in shining machined aluminum and carbon fiber, a bipedal robot with a cavernous cockpit chest. Its colossal arms can mimic the motions of a pilot within, magnifying the size, strength and reach of a human, but retaining the precision. And with a total of 46 high-torque motors and a huge bank of sensors, it can self-balance and walk on flat surfaces.
Method-1 is a sci-fi nerd's dream, and mighty impressive in its own right. But at this stage it's just a test bed. Hankook Mirae Technologies is looking to learn from this prototype and then move on to custom-building similar giant mecha, tailor made for jobs in industry and construction. See it in action in the video below:
If it looks like something straight out of a movie, that's got a lot to do with its chief designer, Vitaly Bulgarov, who has come to the project from a stellar career in concept and robot design for major Hollywood movies like Terminator 4, Ghost in the Shell, Robocop and Transformers 4. He's also done extensive work on sci-fi video games such as Starcraft 2.
According to a representative of the Korean business and engineering team, who answered a few of our questions via email, Bulgarov's work spoke for itself. "Right after seeing his designs on the internet, we flew over to the USA straight away, and asked him to be our chief designer. His work and the man himself gave us no chance for a second thought. He just had to be on our team."
We called Vitaly Bulgarov at his home in Las Vegas to discuss the Method-1 giant mecha project and how it came to be.
On the beginnings of the Method-1 project
A few years back, some of the stuff I was making on the side, just for fun, the group of businessmen in South Korea saw that. They were wanting to do something like this, a large robot, but didn't know where to start.
At the time, they had a kind of idea for it, but not really a vision for how it would look, what it would do, and the right steps to get there. I started to do some concepts for it – I'm planning to release some of the concept art soon, I'm just swamped with work at the moment.
I'm not gonna lie. For me, coming from the gaming design field, the opportunity to build a real mecha was beyond exciting. I grew up on video games, watching sci-fi movies, so if you ask why we wanna build something like this, well, to me, a future where humanity is able to build mechas is more exciting than one where we can't.
Initially we tried to avoid any constraints in terms of size, or anything like that. All we knew was we wanted a bipedal robot that's controlled by a pilot who's in the cockpit of that robot. What would that look like, what would the challenges be besides the obvious?
I tried to avoid looking at any sci-fi robots for inspiration, we wanted to start with a clean slate. One of my first designs was much more automotive, or organic looking. And as we progressed, we met the challenges and the limitations of range of motion, and degrees of freedom for each joint. It became a lot more industrial looking. And as we kept iterating, it started to remind me of the robot suit in Avatar. That wasn't intentional, I guess the praise goes back to James Cameron's vision, his design team had a great understanding of functionality, so the we ended up with the same overall proportions.
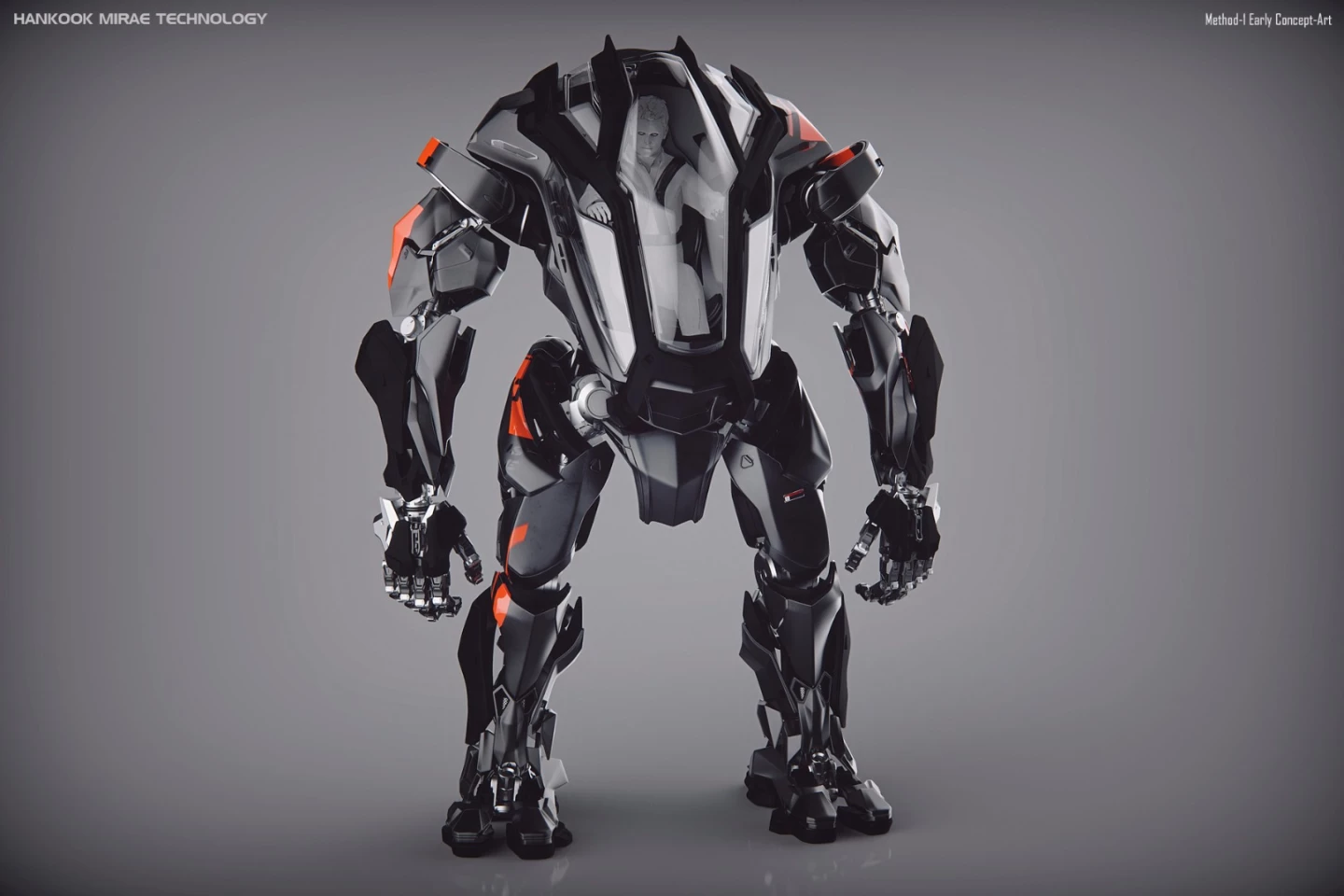
On making a giant robot walk and self-balance
It required a tremendous effort from the engineering team, figuring out custom motors that can provide enough torque at each joint, and things like stability. For example, when you sway your arms, or sway the robot's arms, that creates kind of a sway. And the robot has algorithmic software and next-gen hardware to provide the counterbalance in motion in the hip and waist area.
When I was in the cockpit, I could really feel it. First you feel like you're falling, but no, the robot's just balancing itself. It offsets the center of gravity at the hip to make sure it stays stable. Things like that are very much still under development. I feel very lucky to be working on this, I'm doing all the fun designs while the scientists are doing the groundbreaking work of making it happen.
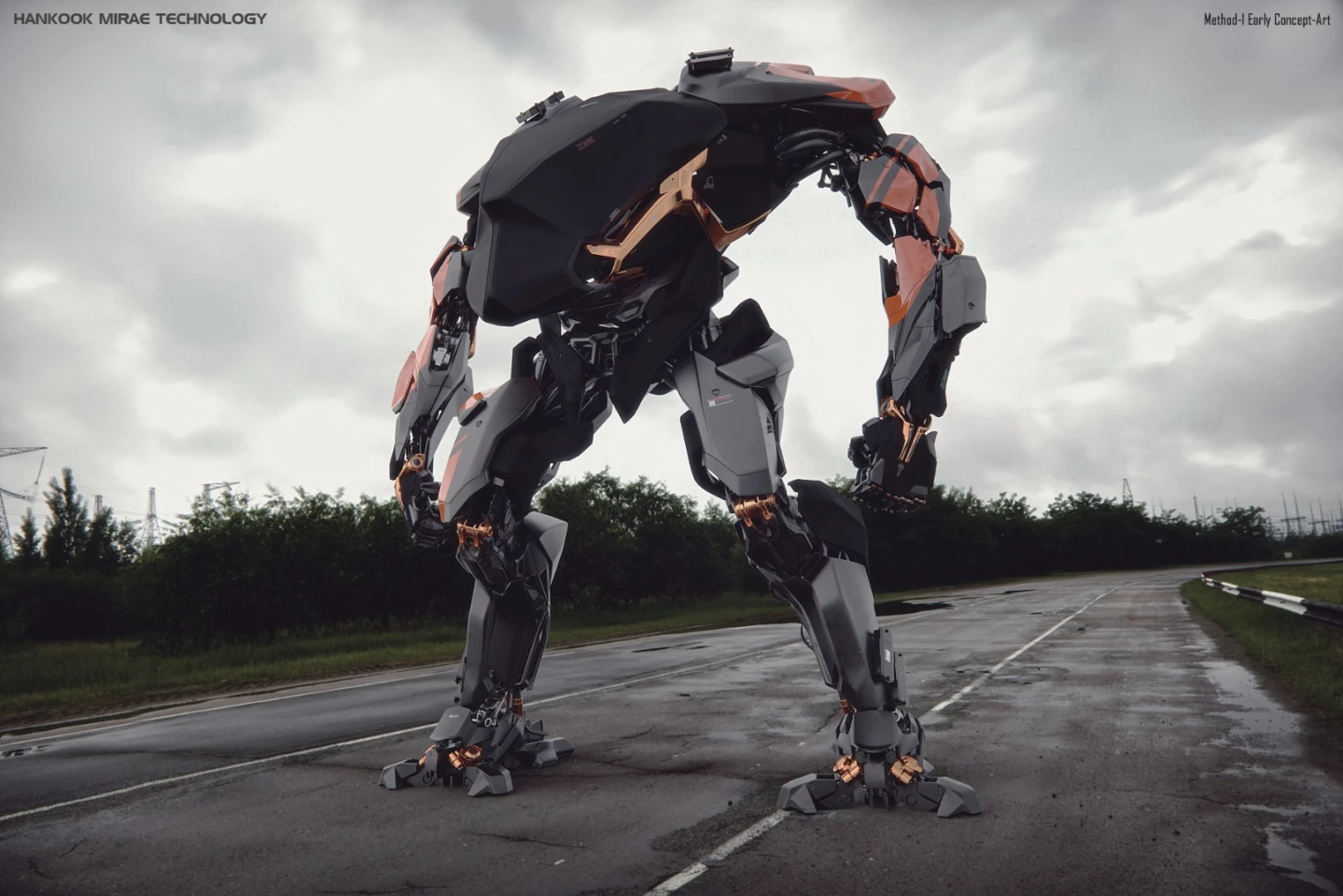
If you look at any concept art for a movie, or a video game, or any sort of fictional robot character, they always look much cooler than all the university projects and industrial robots we've seen so far. And the reason for that is the clearances and range of motion for each joint. You need to provide enough space for the robot – especially a robot with arms – to create an anthropomorphic figure.
It's difficult, because you need to reduce a lot of mass and form to provide that space. The biggest challenge for me was, how can we maintain the sort of look we expect from solid figure instead of a skeletal-looking robot, while keeping it very light. You don't want it to look creepy, or fragile.
For example, the hip joint. We have three degrees of freedom on the hip joint. Just like the shoulder. Three axes of movement, roll, yaw and pitch. They all need to happen from one point. Most of the time you end up with a very conventional looking, three cylinders kind of joint.
If you look at the robot we currently have, the distance between the hips is much narrower than it was in the original concept. I wanted a much wider looking thing that gives the visual impact of being a heavier mecha, without actually being heavy.
But as we refined the design and worked closely with the engineering team, the distance between the legs became much more narrow. The greater the distance between the legs, the bigger the sway will be when the robot walks. That sway can develop a momentum that's hard to get out of.
So those wide hips you see in traditional mecha, that create the illusion of strength and stability – that's not really the case.
On touching, feeling and working with robot hands
Our next short term goal would be to expand on this and see if we can improve it in a few areas. One would be industrial, for factories where there's no issue with using a tether to power it and the ground surface is controlled and flat. Safety is much more manageable. And also the ability to design a robot to suit a particular factory's requirements.
It could be useful when delicate work is required, but at a larger size. One of the concepts we have is switchable hands – like a CNC machine, you could switch the tools on the ends of each arm. From a blowtorch to the jaws of life, things you might need a heavy tool for generally, but now a human can do them with surgical precision from inside the robot. We're looking at that stuff.
Another direction, this company Hankook Mirae Technologies has a subsidiary in Japan that is working on the restoration of the Fukushima disaster area. The goal is really to combine a vehicle with an upper body similar to this robot – a modified version, one that's stronger and with a number of modifications. For example, a cockpit that's entirely closed for use in radioactive areas. It might have cameras outside to help with doing the delicate work outside.
One of the other companies I've worked with in the past was Intuitive Surgical, the company behind the Da Vinci robot-assisted surgery system. Instead of opening up a patient's chest in an invasive way, the surgeon makes three small incisions, one for an endoscope and two more for small mechanical arms.
The surgeon can sit outside in a console and control what happens inside a patient on a much smaller and more delicate scale. I've worked with that company for more than a year on some of their next-generation concepts. You can think about what we're doing now with Method-1 as kind of the same thing on a larger scale. Instead of going smaller, we're going bigger, trying to amplify human capability, but keeping the ability to delicate work and feel your hands.
So one of the next steps is working on some kind of haptic feedback system. Like, you can feel it through your control arms in the cockpit. You can tell the motors to give some extra resistance when the hands touch something and you can feel resistance from a surface. The engineering community has already tested this on a few concepts.
If you think of an excavator as being something really brutal, like a hammer, this can be much more precise, but with a scale that goes way beyond human scale.
This is not really a new concept. But I think we're really reaching the verge of that technical capability. Really powerful, but power-efficient motors, and also materials and machining and engineering… now we can really see if we're ready to bring this stuff to a real world application.
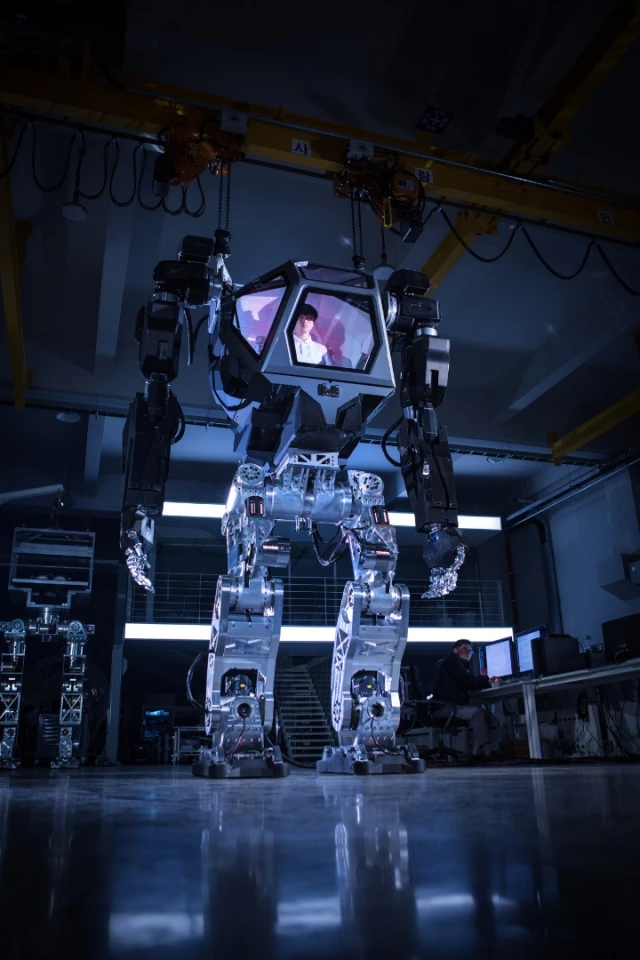
On form vs. function, design vs. engineering
There's always this back and forth between what is the most practical solution, and what's more appealing if this becomes a real product. You look at companies like Apple, they're very delicate about how a product looks and feels. We're trying to take the same approach. Maybe we don't really have to do it, but we want to do it.
Even when I was doing design for movies and entertainment, I always tried to keep learning about functionality. I was always reading books and trying to think like an engineer. And now, working on projects like this, I'm gaining a much better understanding of that stuff. I'm still not an engineer, but I'm learning from the engineers on the team about stuff like kinematics, the underlying structure of things, which is grounded in physics, the limitations you have to deal with. I would say that today I'm much more aware of that than I was five years ago.
Both of these worlds can inspire one another. Now when I work on a movie - I just finished some work on Ghost in the Shell, I made some of the lead robotic designs – I'm trying to ground my designs much more in reality, the correct constraints. I'm trying to make the movie designs more realistic.
But when I work on actual product, it's the other way around. I know we have a team of amazing engineers, so I'm trying to inspire them to get outside their comfort zone. Sometimes, I'll show them – this is how it looks if we make it completely functional and realistic – it's working – and here's a version of the same joint where I'm going for more aesthetics. Do you as an engineer think there's a way to find a compromise? Somewhere to meet in the middle where it still works but it looks much better?
A lot of the time my job is to inspire the engineers to stay excited about the project. One of the roles of the designer is not just to inform the visual direction of where we're going, or the ideas of what we're trying to build, but also to inspire the team.
On his other projects
I'd love to get back to the movies, but my current projects are all industrial design. Obviously, there's the Method-1 robot for Hankook Mirae Technologies. I also work for Boston Dynamics, another robotics company, on the Atlas robot they're developing. I'm working with them on an exterior shell to protect the body, and also partial frame redesign. And also I'm working with Panasonic on an announced project I can't talk about yet. It's all industrial design right now.
But I'd love to get back to do some movies. People always talk about how writers like Jules Verne inspired science and engineering, how science fiction inspired realty, but I really feel like today we're living in a world where one can inspire the other. The entertainment world reduces the limits – we can do anything – and that opens up the imagination and different perspectives to look at a problem from. But imagination and problem solving, they don't work without each other, and I think they can inspire each other.
More about Bulgarov's work: Vitaly Bulgarov
Edit: Bulgarov has sent us the final design that Hankook Mirae has signed off on - the mech we're looking at is far from finished, but should end up looking like this:
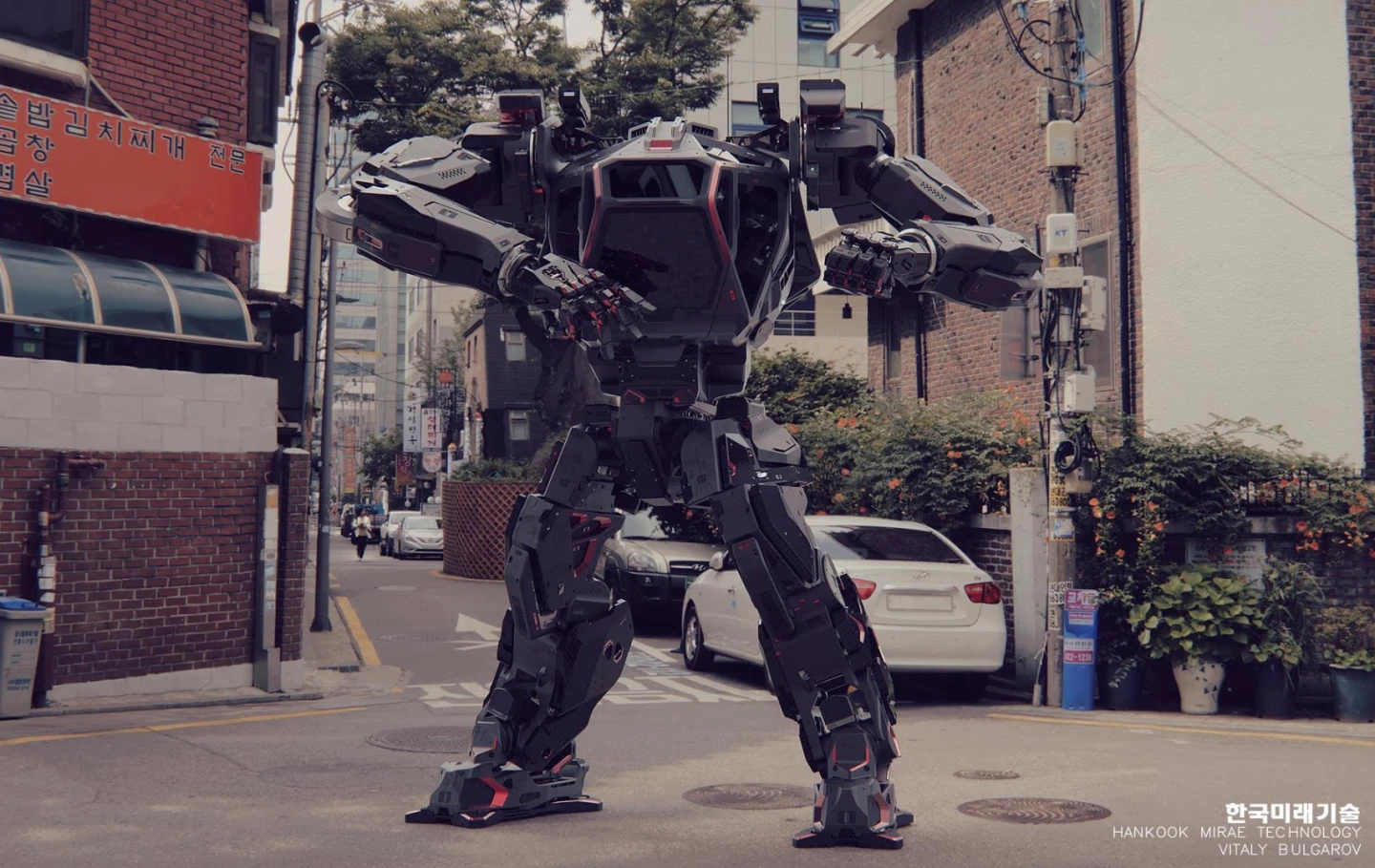