A Florida team working with the US Air Force claims that it's built and tested an experimental model of a rotating detonation rocket engine, which uses spinning explosions inside a ring channel to create super-efficient thrust.
The vast majority of engines, of course, use combustion rather than detonation to achieve their output goals. Combustion is a relatively slow and controlled process resulting from the reaction between fuel and oxygen at high temperatures, and it's very well understood and mature as a technology.
Detonation, on the other hand, is fast and chaotic and much less predictable. An explosion instead of a burn, it is the massive discharge of energy you get when you break apart the chemical bonds holding an explosive molecule together by giving it a jolt of energy – either electrical or kinetic – in the form of a sufficiently powerful shockwave to destabilize those bonds. Detonation is excellent when you want to wreck stuff in bulk, and much harder to maintain precise control over.
But when you need to break the chains of the Earth's gravity and go to space, every gram of weight makes things that much harder and more expensive. Detonation releases significantly more energy from significantly less fuel mass than combustion, so for more than 60 years, rocket scientists have been working on the idea of a rotating detonation rocket as a potential way to cut down weight and add thrust.
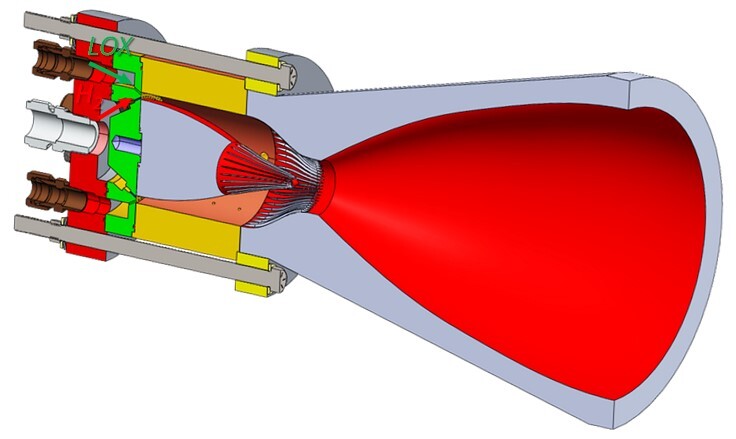
In essence, such a device starts with one cylinder inside another larger one, with a gap between them and some small holes or slits through which a detonation fuel mix can be pushed. Some form of ignition creates a detonation in that annular gap, which creates gases that are pushed out one end of the ring-shaped channel to produce thrust in the opposite direction. But it also creates a shockwave that propagates around the channel at around five times the speed of sound, and that shockwave can be used to ignite more detonations in a self-sustaining, rotating pattern if fuel is added in the right spots at the right times.
Pioneered by engineers at the University of Michigan in the 1950s, the rotating detonation engine is tantalizingly simple in a mechanical sense, but this self-propagating detonation wave has proven torturously difficult to achieve and sustain.
Until now, it seems. A team at the University of Central Florida, working alongside the Rotating Detonation Rocket Engine Program at the Air Force Research Laboratory, claims to have built and tested a working laboratory model. It's a 3-inch copper test rig using a mix of hydrogen and oxygen for fuel, which is the highest-performing rocket fuel for upper stage rocket engines.
"The study presents, for the first time, experimental evidence of a safe and functioning hydrogen and oxygen propellant detonation in a rotating detonation rocket engine," says Kareem Ahmed, an assistant professor in UCF's Department of Mechanical and Aerospace Engineering who led the research. "The detonation is sustained continuously until you cut off the fuel. We have tested up to 200 lbf, but the thrust increases linearly with the propellant mass flow."
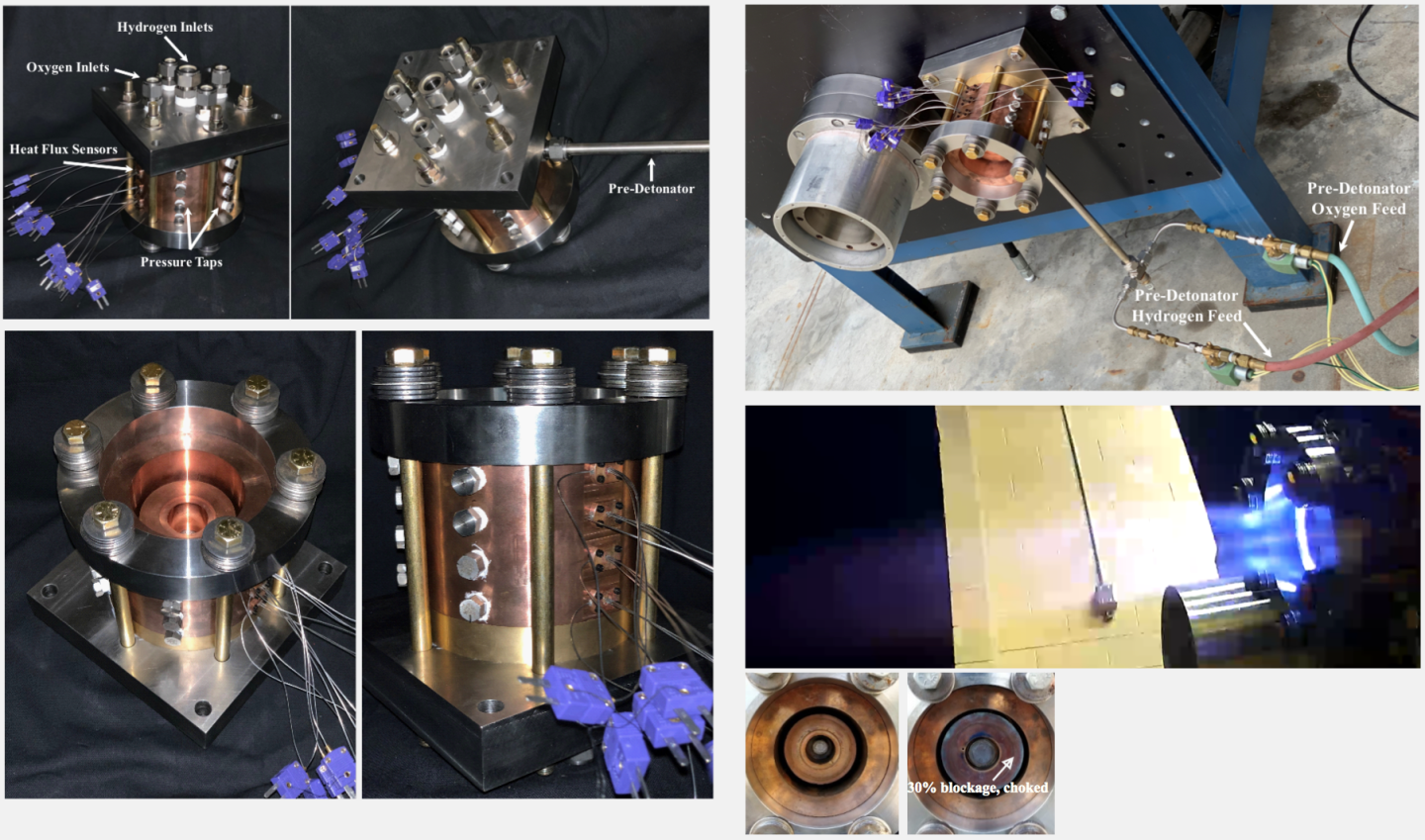
The secret, according to the researchers, was as simple as a tune-up.
"We have to tune the sizes of the jets releasing the propellants to enhance the mixing for a local hydrogen-oxygen mixture," Ahmed says. "So, when the rotating explosion comes by for this fresh mixture, it's still sustained. Because if you have your composition mixture slightly off, it will tend to deflagrate, or burn slowly instead of detonating."
"Just a few months prior, a number of US rocket engine experts had publicly declared that hydrogen-oxygen detonation engines were not possible," Ahmed tells New Atlas. "However, the paper presents experimental evidence and demonstrated without a doubt that detonation of oxygen and hydrogen are occurring within a rotating detonation rocket engine."
"These research results already are having repercussions across the international research community," says William Hargus, lead of the Air Force Research Laboratory's Rotating Detonation Rocket Engine Program, who is a co-author of the study. "Several projects are now re-examining hydrogen detonation combustion within rotating detonation rocket engines because of these results. I am very proud to be associated with this high-quality research."
Ahmed tells us this engine design is being evaluated as a possible replacement for Aerojet Rocketdyne's RL-10 rocket, which was first developed in 1962. Modern versions are still in production for the upper stages of Atlas V and Delta IV rockets, with further versions under development for the Exploration, OmegA and Vulcan rockets, but a proven rotating detonation rocket engine could be a real game-changer.
"The U.S. Air Force is targeting a rocket launch flight test by 2025," says Ahmed, "and we are contributing to achieving that goal."
While space propulsion is the key driver for this research, it also has potential terrestrial uses in other cases where high power and low fuel consumption could make a big difference. In 2012, the Naval Research Laboratory estimated that rotating detonation engines could save the Navy 15-20 percent off a ~US$2-billion annual fuel bill if they were retrofitted in place of the gas turbine engines that run over 100 of its large ships. They could also potentially be used in hypersonic and supersonic flights, or even electric power generation, and Ahmed tells us the design has potential as a booster stage engine as well, but it'd require a different type of propellant.
See a short slow-motion video of the rocket firing below.
The team has published their results in the journal Combustion and Flame.
Source: University of Central Florida