3D-printed architecture seems to have taken another step towards the mainstream, with the news that engineering firm Arup and CLS Architetti are collaborating on the first 3D-printed concrete house in the European Union. Named 3D Housing 05, the project was conceived to demonstrate the efficacy of the cutting-edge technology.
The prototype home is being constructed in Milan's central square, Piazza Cesare Beccaria, and will be officially unveiled during this year's Salone Del Mobile in April. The project also includes Italian cement supplier Italcementi and Cybe Construction.
Just like every other 3D-printed architecture project we've seen, the basic construction process involves extruding a cement mixture out of a nozzle layer by layer to build up the home's walls. However, 3D Housing 05 makes use of a robotic manipulator mounted on a movable base for increased flexibility rather than the more typical static printer.
Once the machine has done its work, humans are then required to finish off the roof, windows, and doors, as well as any other finishing touches. An Arup representative told us that the company is hoping to automate this part of the process in the future too.
The 3D Housing 05 project looks significantly larger and more complex than previous 3D-printed houses we've seen. It will comprise 100 sq m (1,076 sq ft) of floorspace laid out on one level, and include a living area, bedroom, kitchen and bathroom. It's also designed to be easily disassembled, so once Milan's design week comes to a close it can be broken down and installed elsewhere.
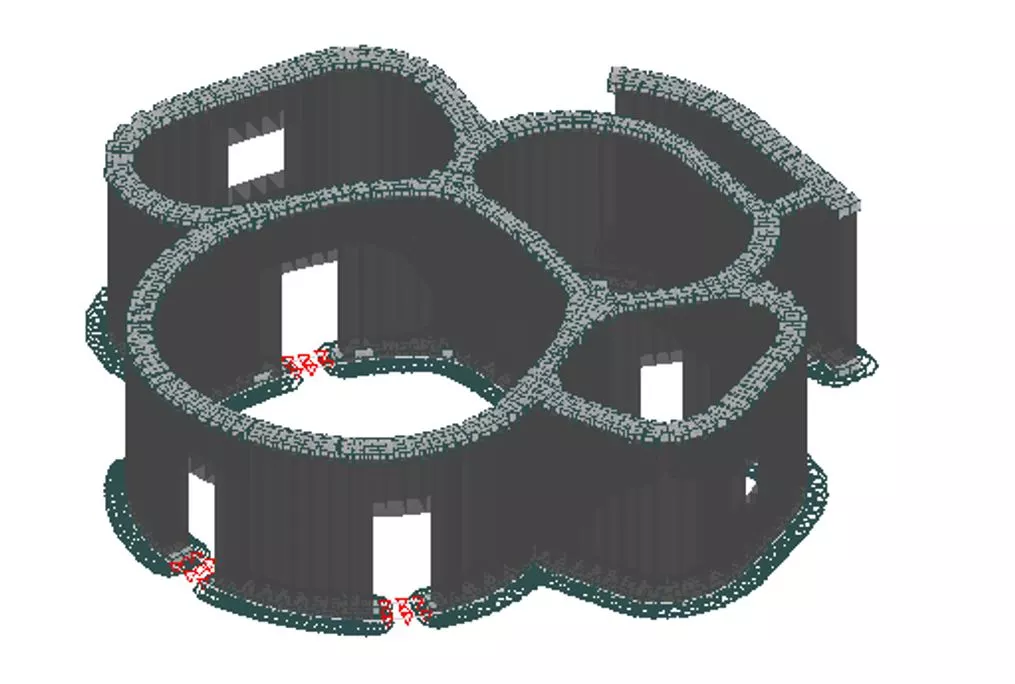
While we've no figures available, Arup told us that the project's cost will be "significantly lower" than a house of a similar type and size constructed using traditional methods, and that the printing process took just 48 hours. Arup also lauded the tech's potential to produce projects quicker and with less waste, for less money and more accurately than before. Naturally we'll be keen to follow up with the firm once it has the finished home ready to show off.
"The construction industry is one of the world's biggest users of resources and emitters of CO2," says Guglielmo Carra, Europe Materials Consulting Lead at Arup. "We want to bring a paradigm shift in the way the construction industry operates and believe that 3D printing technology is critical to making buildings more sustainable and efficient. It creates less waste during construction and materials can be repurposed and reused at the end of their life."
Sources: Arup, CLS Architetti