We covered a lot of bike-related innovations last year, but by far the most popular was CeramicSpeed's DrivEn pinion-style shaft-drive system. Now, its designers have taken it much closer to real-world usability, by giving it the ability to shift between gears.
To recap our previous coverage, the original version of the setup consisted of a cylindrical carbon fiber shaft that reached from a single chainring in front to a flat 13-speed cassette on the rear wheel. Mounted on either end of that shaft were sets of very-low-friction ceramic bearings (a total of 21) contained within front and rear cylindrical devices known as pinions – these engaged the teeth on the chainring and the cassette cogs. As the rider pedaled, the bearings transferred torque from the chainring through the shaft and into the rear wheel, turning it.
At the time, the system's Colorado-based inventors proclaimed that DrivEn was the world's most efficient bicycle drivetrain – when it came to converting pedaling energy into wheel motion, that is. And just last month, it was announced that wind tunnel testing conducted in partnership with Specialized revealed that it is also one of the most aerodynamic. Now, at this year's Eurobike show, the system's master/slave-type gear-shifting functionality is being unveiled.
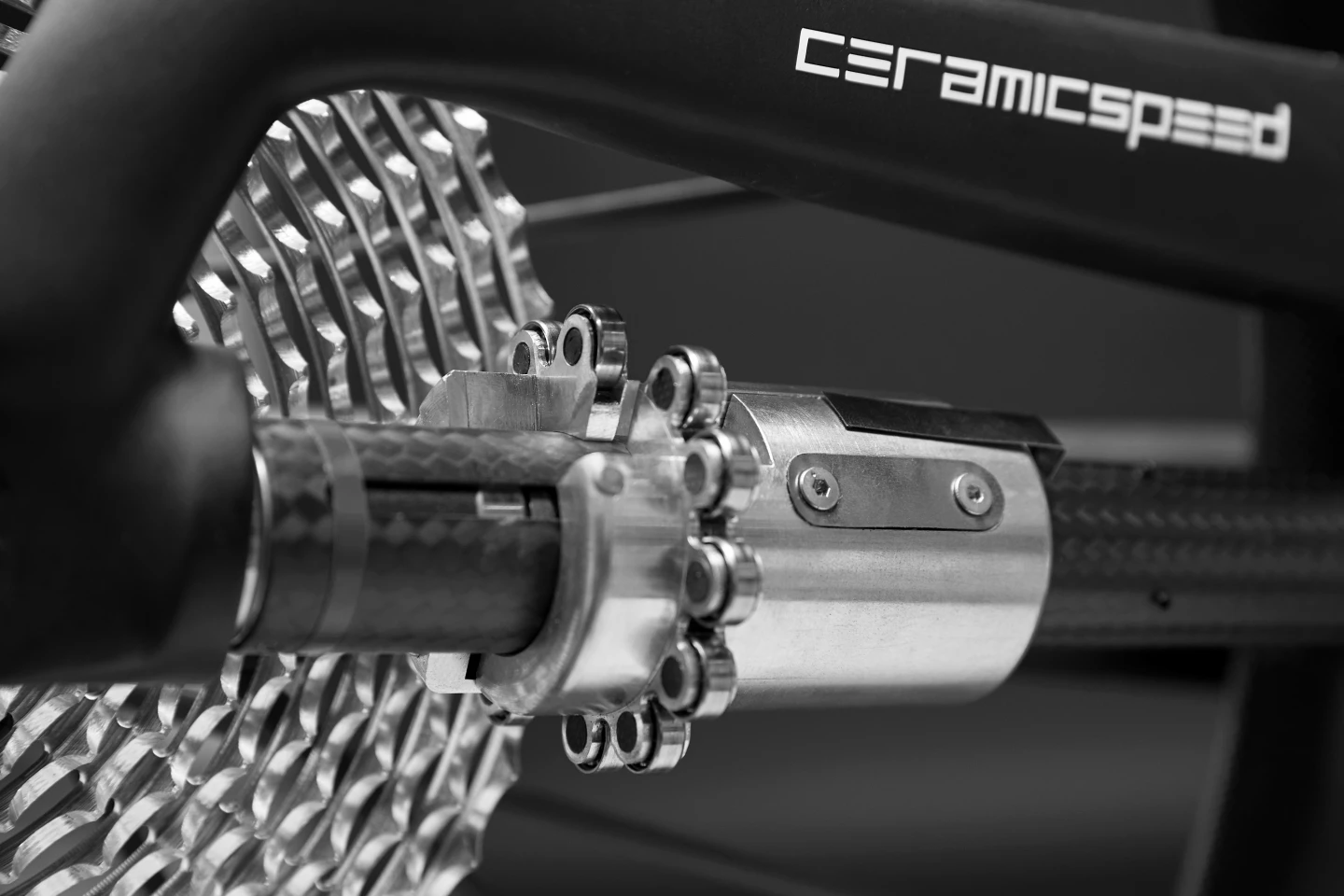
At the heart of the new system is a laterally-split rear pinion.
In response to a wirelessly-transmitted signal from a handlebar-mounted shifter, the side/half of the pinion that is not currently engaging the cassette cog teeth gets moved forward or backward by an actuator inside the shaft. As the bearings on that (master) side of the pinion proceed to rotate 180 degrees and engage the teeth on a new cog, the linked (slave) side of the pinion also gets pulled over onto that cog, so that both sides of the pinion are now back in line with one another, but on a different cog.
The mechanism is illustrated in the following video.
According to CeramicSpeed CTO Jason Smith, all of the shifting hardware (except for the bar-mounted shifter) is located on or in the shaft. He says that battery life should ultimately be similar to existing wireless electronic shifting systems, such as Shimano Di2 – in the system's current form, one charge has proven to be good for at least 1,800 shifts, with plenty of juice left over.
In terms of the number of gears, the present prototype has a 13-cog cassette, plus the front pinion could also be split, allowing it to be shifted between two chainrings. That said, Smith tells us that the design allows for an almost unlimited number of cogs or chainrings – within practical limits, that is. "You wouldn't want a rear cog as large as your rear wheel," he says.
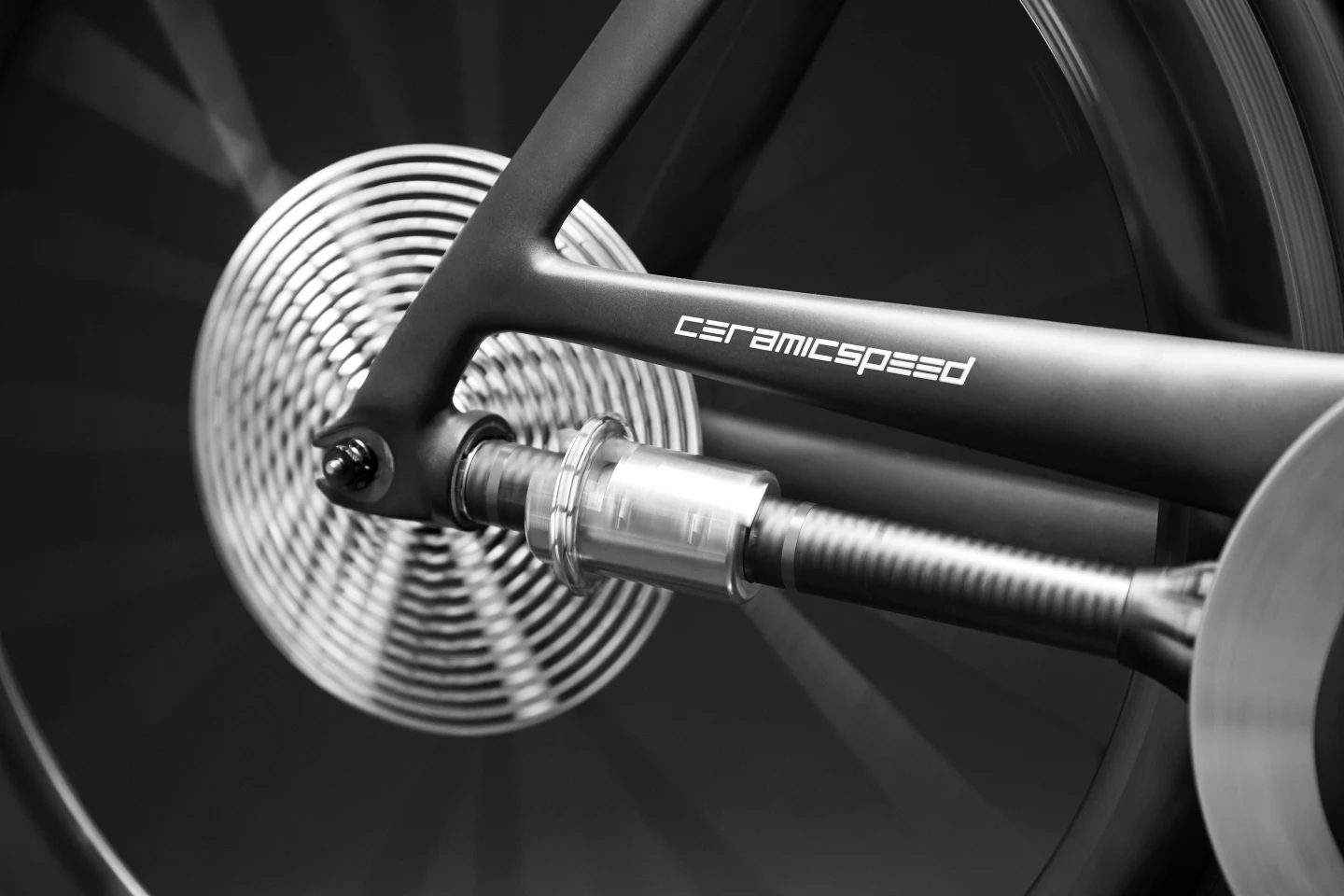
The system is said to be suitable for both road and mountain bikes (even full-suspension models), and requires no lubrication. Initially, bikes equipped with it might be a bit pricier than most others, although once the system reaches full production, those prices should drop to the range of other electronically-shiftable bikes.
"We're now at the point where we've taken this as far as we can, we've got the shifting down, the ride-ability, we've addressed a lot of the challenges," says Smith. "We're starting to consider looking for somebody to team up with that has deeper pockets and is potentially in the drivetrain market or would want to be."
So, should anyone from a company such as Shimano, SRAM or Campagnolo be reading this … Jason and his team can be reached via the link below.
Source: CeramicSpeed