The winner of the James Dyson Award 2010 will be announced next week and there's just time for a closer look at one of the finalists, the Butterfly micro scooter. Taking inspiration from a collapsible umbrella, adding some street durability and clever engineering - and a touch of Mini styling - and the human-powered, portable urban transport solution is ready to ride. When folded, the scooter is small enough to fit inside a backpack or carried by hand but at the press of a button, flips open and extends out to a nifty three-wheeler.
I have to admit that when pawing my way through the finalists' pages on the Dyson Awards site, it was the video that accompanied the project details for the Butterfly which grabbed my attention. Designers Martin Ruegg and Simon Koenig told Gizmag that "it all began with a collapsible mini-umbrella, manufactured by a company called KNIRPS. We were very impressed by this unique parallelogram-mechanism.The umbrella's spring-loaded opening system is released by a push-button. Therefore the object is open and ready to use instantly."
In fact, the very first prototype was built using the inner workings of the umbrella and although not particularly effective as a road-worthy scooter – as you can see from the following video–- it succeeded in propelling the duo into Butterfly territory.
The designers took the basic elements of the KNIRPS umbrella design and transferred them to a stronger, working 12.2-inch (31cm) long prototype that is strong enough to ride on. Ruegg explained that the internal mechanism is based on "two identical parallelogram constructions. Each functions through 5 pivot points with bush bearings. The allowance for clearance is reduced to a minimum due to the parallel guidance. The main connection on the steering tube is a smooth running, ball-bearing fitting."
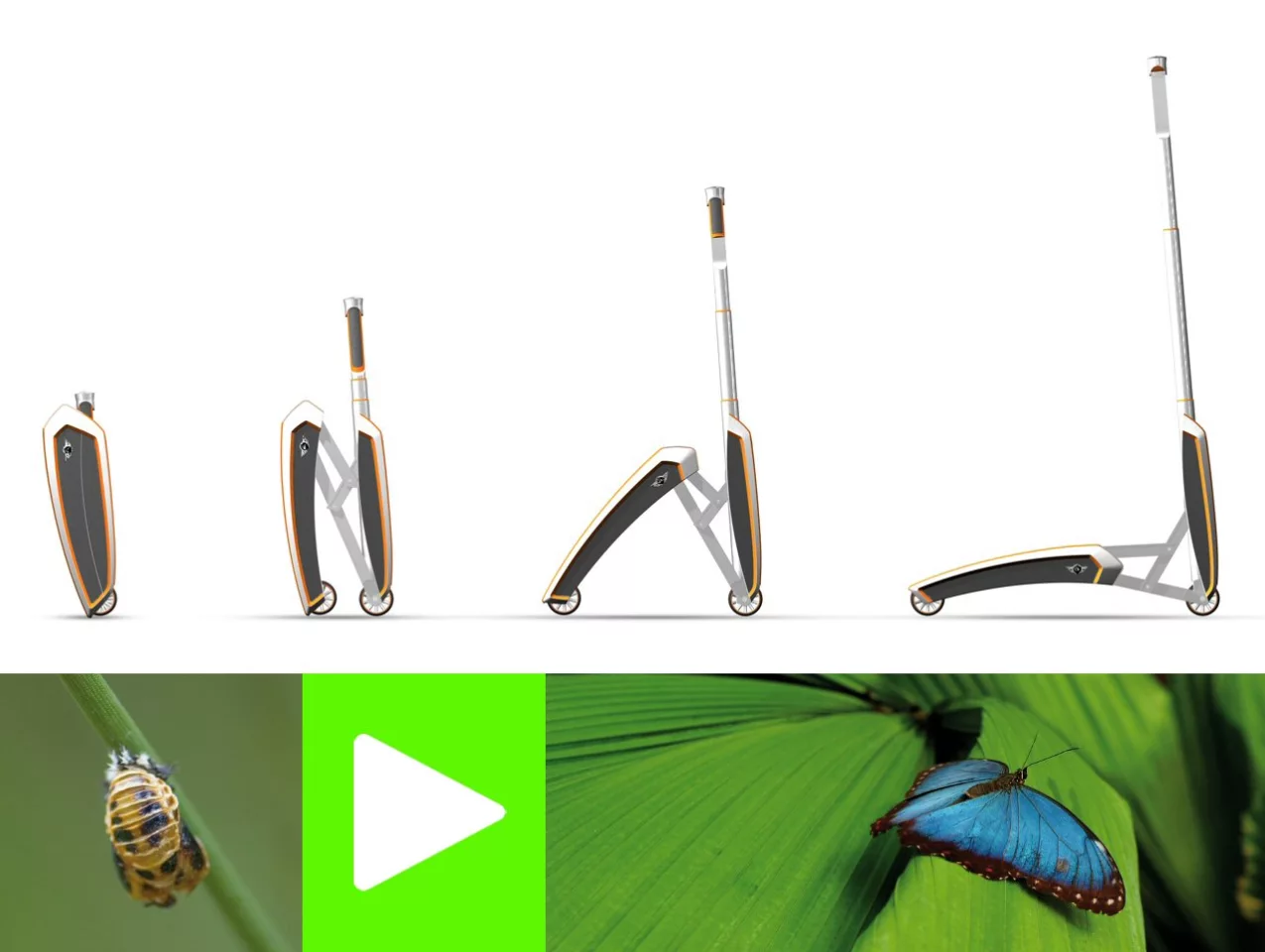
The outer shell protects the mechanical core and is made from carbon fiber in order keep weight to a minimum without making any unnecessary concessions on strength and durability. The final production version will have a non-slip surface underfoot, much like that used on skateboards and the cosmetic Mini-type detail seen in the computer models. Steel was used in the construction of the internal mechanism and is put together so the multiple pivot points and shell all snuggle against each other and snap into place to provide a solid framework that is currently capable of carrying around 176 pounds (80kg) – with a final production model aiming for 220 pounds (100kg).
"There are two wheels in the back, one in the front, said Ruegg. "Thus the single wheel in the front will smoothly slide in-between the two wheels in the back when Butterfly is closed. Everything but the laminated shell is shop-bought. We were students and had no financial support. We reduced the width of the wheels by machining them, so they would fit next to each other."
It only takes a second to flip open the mechanism to reveal the scooter inside, where the Butterfly is in its natural position and ready to ride.
"When closed, the spring is on tension. Accordingly there is no risk of a sudden collapse of Butterfly. Even though, there is a ball catch to provide the folding performance with a certain quality."
At the moment the Butterfly opens and closes with the aid of springs but the designers would prefer to use hydraulics for future incarnations.
The designers see only light maintenance being necessary to keep the Butterfly in tip-top condition, Ruegg confirming that "the maintenance depends on the quality of the bearings. If they are loose, a simple hexagon socket screw key should do to tighten them."
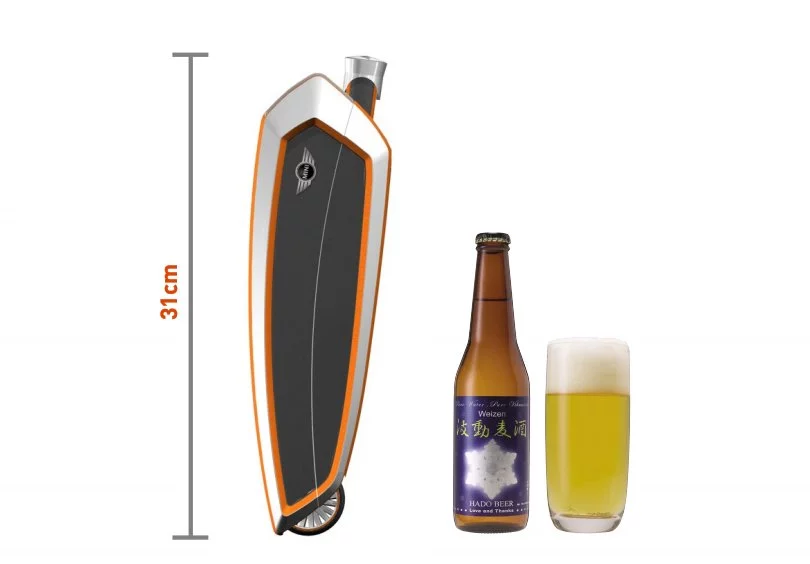
The Butterfly micro scooter was developed in cooperation with BMW – although it was produced without either financial or technical support – and has recently been presented to the company at its Munich headquarters, where it was received well.