Like other automotive manufacturers, Ford already uses 3D printing technology in the development of its vehicles as a fast and cost-effective way to create new tools and test and refine new designs. Now the company is claiming a record for the largest 3D-printed metal part ever put inside a working vehicle. That vehicle is Ken Block's "Hoonitruck" Ford pickup.
The "Hoonitruck" is the star of Ken Block's latest Gymkhana 10 video and is also featured in the Forza Horizon 4 video game. It's based on a 1977 Ford F-150 and packs the same twin-turbo 3.5-liter V6 EcoBoost engine found in the Ford GT, tuned to deliver over 900 hp of drift-inducing power according to Ford (although FH4 lists 915 hp and 953 Nm/703 lb-ft of torque).
Making the vehicle a reality required a special aluminum intake manifold to supply the engine's cylinders with air from the turbochargers, so Ford Performance Engineers teamed up with the team at RWTH Aachen's Digital Additive Production Institute in Germany to create one.
"We are fortunate to have access to incredible technology, but this was one project that pushed us – and our computing power – to the absolute limit," says Raphael Koch, engineer, Advanced Materials and Processes, Ford of Europe. "The manifold has a complex web‑like structure that couldn't be made using traditional manufacturing methods. We ended up dissolving the support systems in acid."
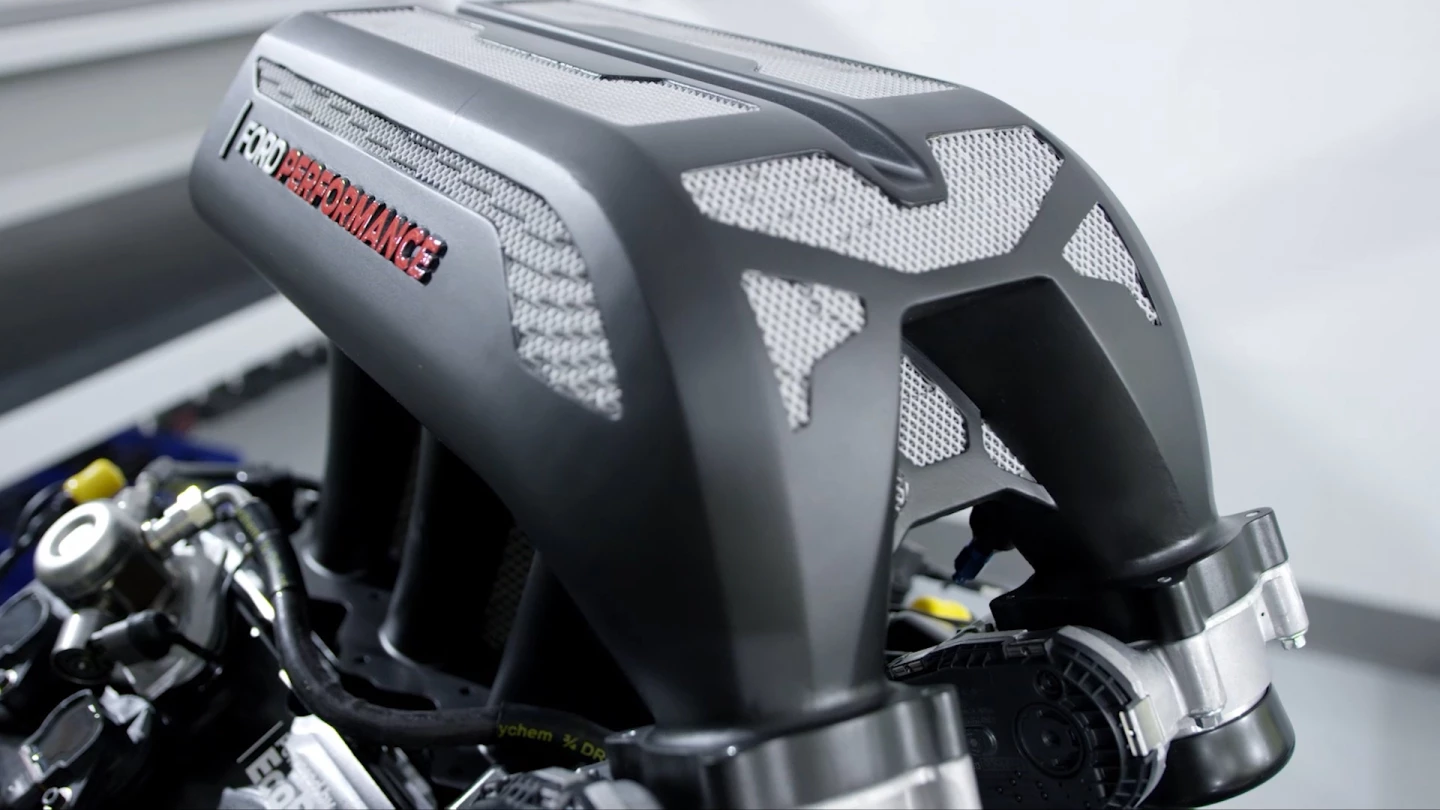
The manifold in question took five days to build and weighs almost 6 kg (13.2 lb), with Ford claiming it's the largest metal 3D-printed part to find its way into a working vehicle in automotive history.
"I think Ford did an exceptional job," says Block. "This is my favorite part of the 'Hoonitruck'. You could not have made it any other way."
The first video below shows how the part for the "Hoonitruck" was created, while you can see what Block can do behind the wheel of the pickup – and four other Ford vehicles – in the Gymkhana 10 video below.
Source: Ford