Building a wall by precisely stacking randomly shaped boulders could almost be the definition of hard work – both physically and mentally. It's the sort of thing we might want robots to do one day, so it should come as no surprise that one has in fact just done it.
The "robot" is named HEAP (Hydraulic Excavator for an Autonomous Purpose), and it's actually a 12-ton Menzi Muck M545 walking excavator that was modified by a team from the ETH Zurich research institute. Among the modifications were the installation of a GNSS global positioning system, a chassis-mounted IMU (inertial measurement unit), a control module, plus LiDAR sensors in its cabin and on its excavating arm.
For this latest project, HEAP began by scanning a construction site, creating a 3D map of it, then recording the locations of boulders (weighing several tonnes each) that had been dumped at the site. The robot then lifted each boulder off the ground and utilized machine vision technology to estimate its weight and center of gravity, and to record its three-dimensional shape.
An algorithm running on HEAP's control module subsequently determined the best location for each boulder, in order to build a stable 6-meter (20-ft) high, 65-meter (213-ft) long dry-stone wall. "Dry-stone" refers to a wall that is made only of stacked stones without any mortar between them.
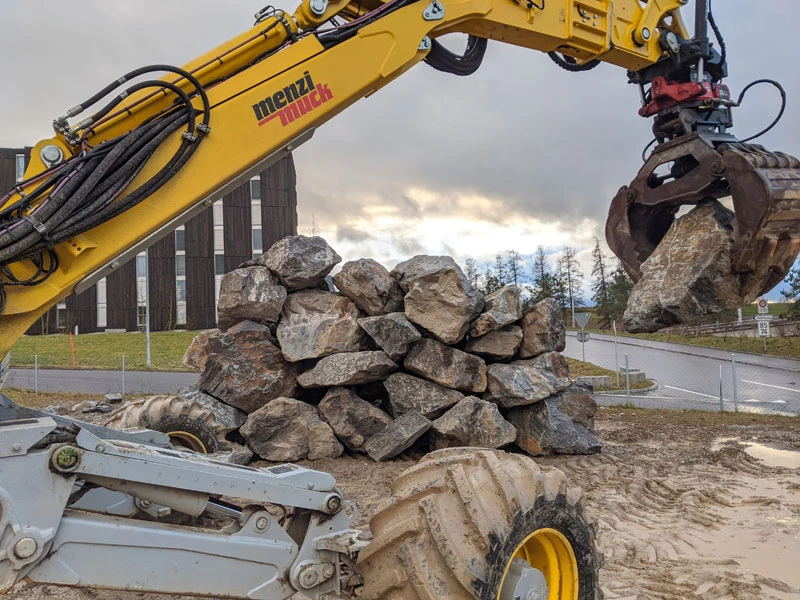
HEAP proceeded to build such a wall, placing approximately 20 to 30 boulders per building session. According to the researchers, that's about how many would be delivered in one load, if outside rocks were being used. In fact, one of the main attributes of the experimental system is the fact that it allows locally sourced boulders or other building materials to be used, so energy doesn't have to be wasted bringing them in from other locations.
A paper on the study was recently published in the journal Science Robotics. You can see HEAP in boulder-stacking action, in the video below.
Source: ETH Zurich