With a few exceptions, robotic grippers aren't known for having a soft touch – so they often can't be trusted with delicate objects. That may be about to change, however, thanks to a shock-absorbing gripper developed by scientists from the University at Buffalo.
Created by a team led by Assoc. Prof. Ehsan Esfahani, the experimental new gripper incorporates two motorized fingers that slide towards or away from each other, along a track. Each finger is mounted on a magnetic base, which sits between two "repulsive" neodymium magnets which push against it. Neither magnet is actually touching the base, so there's an air gap between each side of the base and its corresponding magnet – that gap acts as a shock-absorbing spring.
When the two fingers close together to grasp an object between them, the magnets on either side of each one sit relatively close to its base, keeping the finger held firmly in place by pushing against it. That said, there still is a bit of an air gap, allowing the fingers to "give" somewhat when cradling a fragile object.
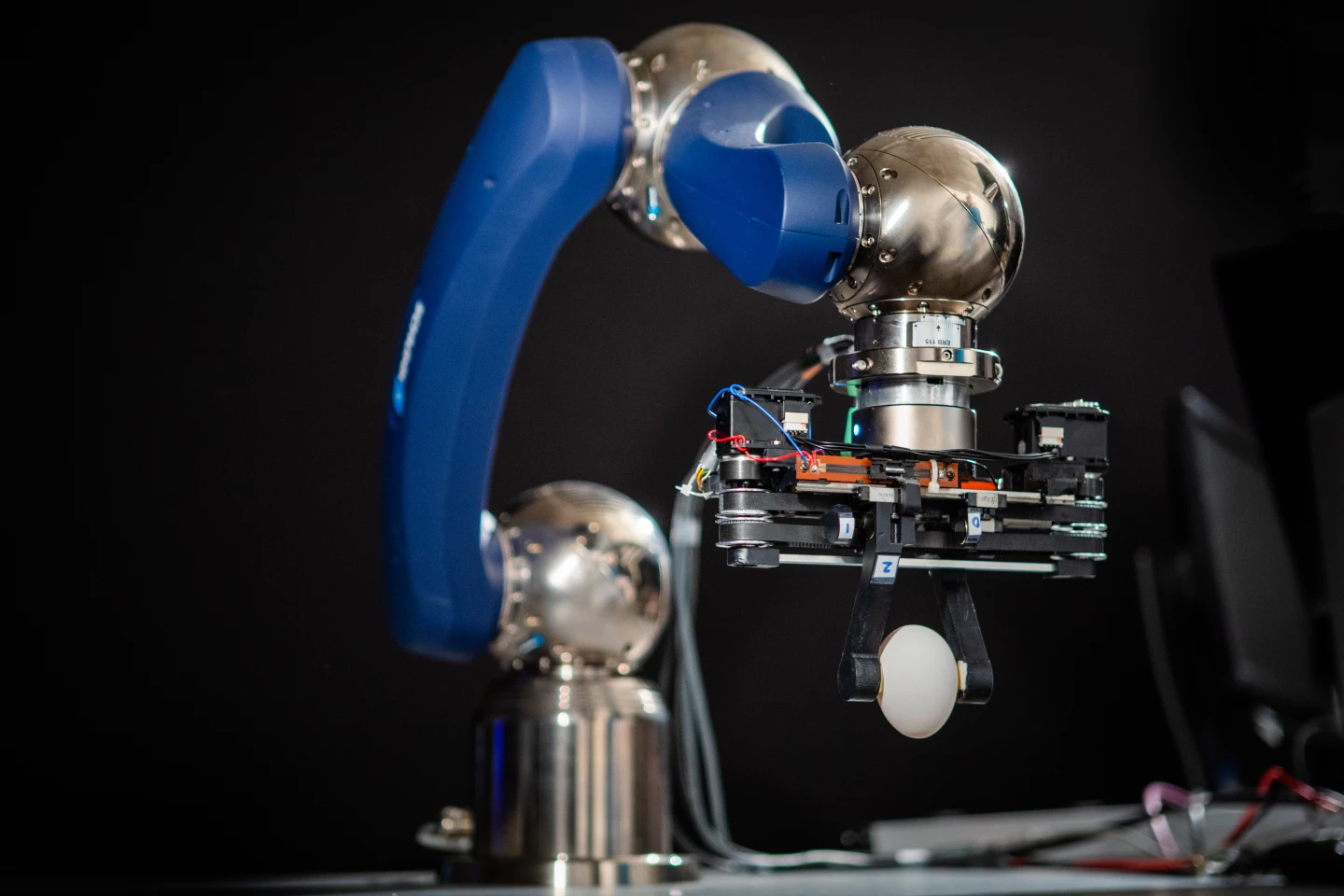
As that item is subsequently being lifted and moved (via a robotic arm to which the gripper is attached), there's always a chance that the gripper may accidentally be knocked against an obstacle. Should that happen, an integrated sensor detects the impact, and responds instantaneously by moving the magnets farther away from the fingers. This reduces the repulsive force, allowing the two fingers to absorb the impact by temporarily sliding over relative to the rest of the gripper.
Once the obstacle is cleared, the magnets are moved back in, pushing the fingers back over to their original position. And as an added benefit, the system not only protects items that are being carried, but it could also keep factory workers from being injured by industrial robots.
"These grippers are designed for collaborative robots that work together with people," says Esfahani. "They’re going to be helpers, so they need to be safe, and variable stiffness grippers help to achieve that goal."
The technology is now being commercialized for use with third-party robotic arms, via a spin-off company. It's described in a paper that was recently published in the journal IEEE Transactions on Industrial Electronics, and is demonstrated in the following video.
Source: University at Buffalo