In an effort to demonstrate the use of a construction material that is more sustainable than commonly used alternatives, Dutch students have constructed a 14-m (46-ft) long footbridge out of hemp and flax fibers. The so-called "biobridge" is located in Eindhoven, Netherlands and will open to the public on Thursday.
The project has come out of the 4TU partnership between the four universities of technology in the Netherlands, TU Delft, Eindhoven University of Technology (TU/e), University of Twente and University of Wageningen. Together, the institutions seek to strengthen and share their knowledge with the aim of helping to develop more and better qualified engineers and technical designers than would otherwise be the case.
For TU/e, the biobridge project isn't the first time it has worked on constructing a bridge with unorthodox materials.
"Using biocomposite in constructions reduces our dependence on finite fossil resources and brings us a step closer to the circular economy in which products and resources are reused," says TU/e researcher and project leader Rijk Blok. "In time, I expect that we will see more of these materials in our buildings."
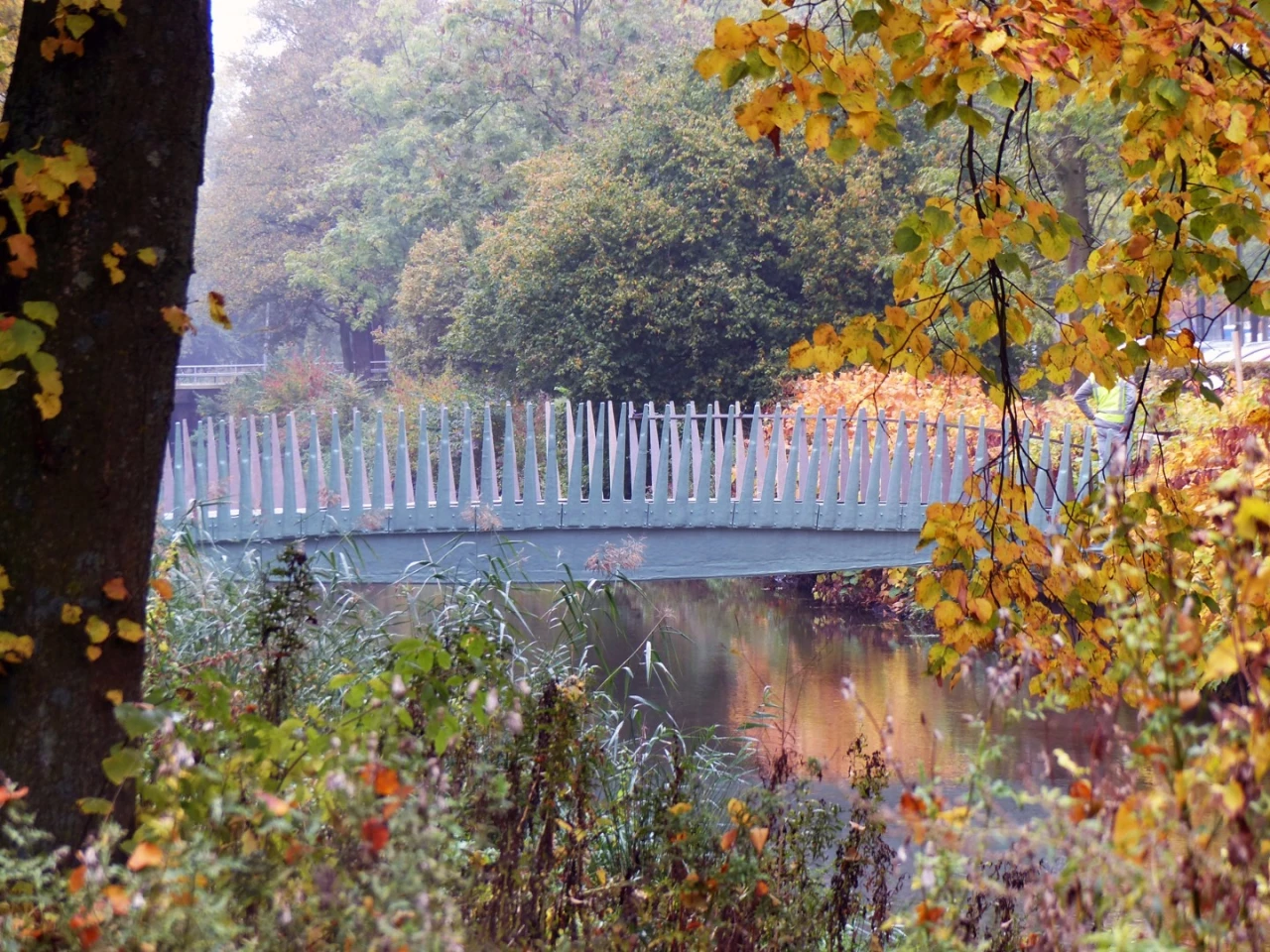
Project funding was applied for at the end of last year and the project began in January. A model of the bridge was constructed in June, with work on the final bridge structure beginning in August and continuing until last week.
Hemp and flax were chosen as they are abundantly available, although project leader Patrick Teuffel tells New Atlas that other fibers could have been used and points to the use of bamboo fiber in another, similar project. The hemp and flax fibers are stuck to a polylactic acid foam core, which may sound terrifying, but is actually touted as an environmentally-friendly replacement for polystyrene. The plastic has a low density and is both biodegradable and compostable.
Once the fibers are in place, a vacuum is used to suck bioresin, into the fiber layers, which ultimately creates the biocomposite. The bioresin hardens and binds the fibers together, but is greener than more conventional resins, with bioresins variously able to be recycled, to degrade, or to be composted. Teuffel says that while alternative materials such as steel, concrete or carbon fiber may be stronger and stiffer than the resulting biocomposite, the difference isn't as great as may be expected and that the biocomposite has the additional benefit of comprising ingredients that are more plentiful and less environmentally harmful.
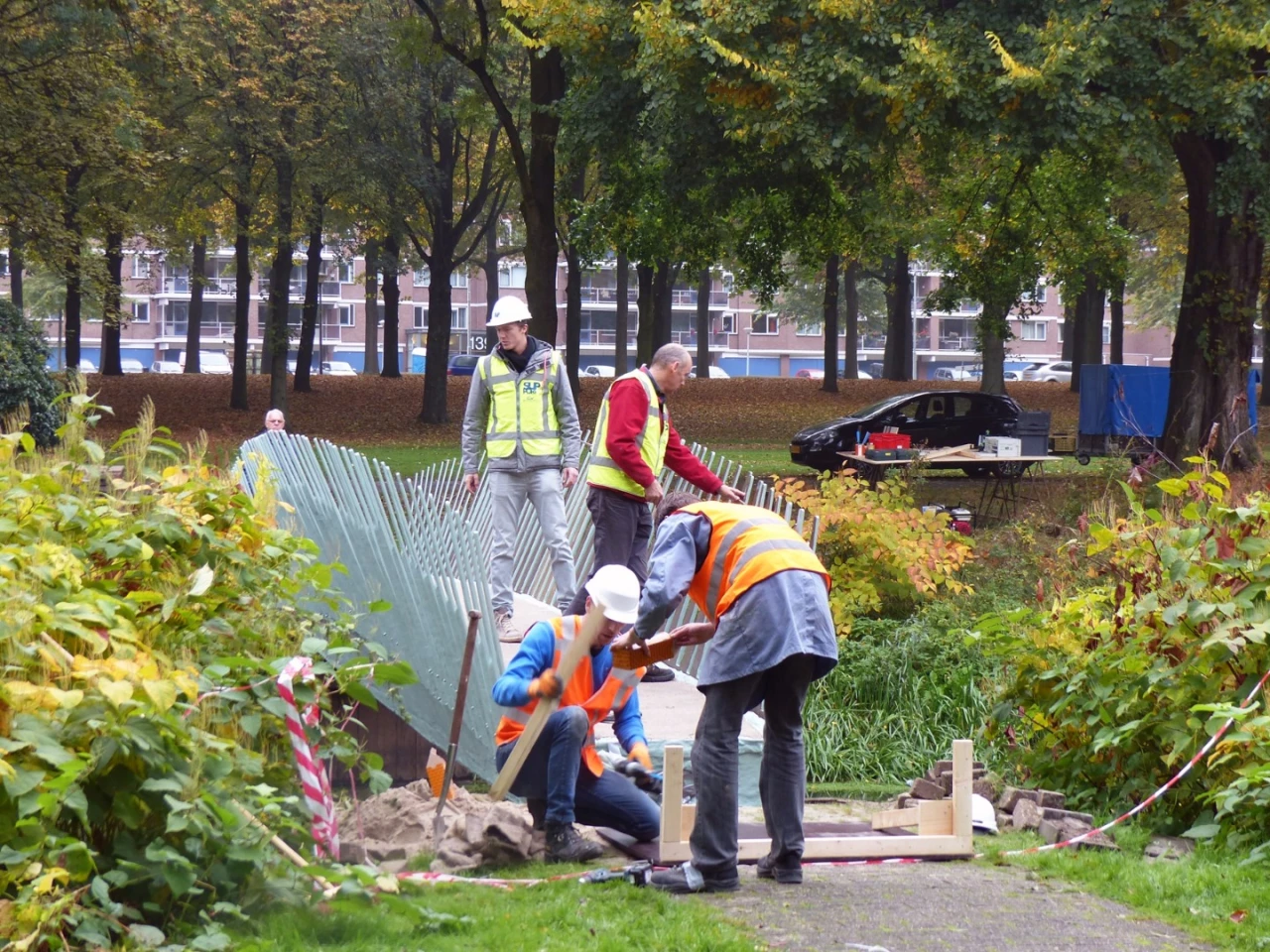
Blok explains that, although biomaterials have been used for construction in the past, they have not as yet been used to create load-bearing structures, so the biobridge will be a test-bed to see how such material performs. An existing bridge has been moved to make space for the biobridge and the project-team has permission to leave it in place for a year. Teuffel says that it could be expected to have a lifespan of two years at the very least, but that it is difficult to estimate beyond that. Indeed, the bridge will provide the first real insight in that respect.
To help provide that insight, there are twenty-eight sensors embedded in the bridge that will be used to measure strain and bending. This data will be relayed to the project team in real-time and data on factors like temperature, moisture and UV light exposure will also be monitored.
The load capacity of the bridge was was successfully tested last week and it has been lifted into place over the Dommel river on the TU/e campus today.