Graphene is themodern go-to material for scientists and engineers looking to create all manner of new electronic devices. From ultra-frugal light bulbs (bothbig and small), to super-efficient solar cells, flexible displays and much more, graphene is a multi-tasking marvel. However, in all ofthese instances, graphene in its original form of atom-thin, flat sheets has had to be used with peripheral supports and structures because it lacks a solid shape and form of its own. Now researchers from theUniversity of Illinois at Urbana-Champaign (UIUC) have come up with a way of creating3D objects out of graphene that opens up the possibility of fashioning a whole new range of innovative electronic devices.
To create 3D shapes in graphene, the researchers first had to ensure that their approach was sufficient to maintain the structural integrity of the material when it was subjected to deformation. As such, the team used an underlying substrate former over which they laid a film of graphene that had been soaked in solvent to make it swell and become malleable. Once overlaid on the former, the solvent then evaporated over time, leaving behind a layer of graphene that had taken on the shape of the underlying structure. In this way the team was able to produce a range of relatively intricate shapes.
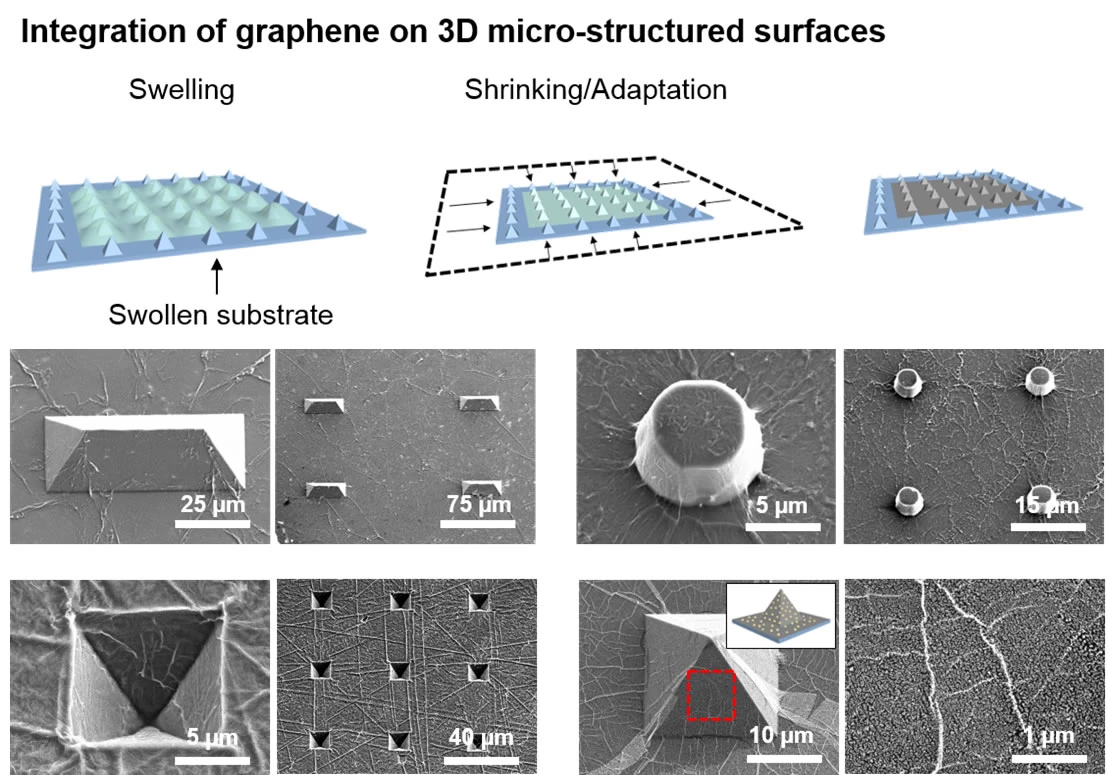
"To the best of our knowledge, this study is the first to demonstrate graphene integration to a variety of different microstructured geometries, including pyramids, pillars, domes, inverted pyramids, and the 3D integration of gold nanoparticles (AuNPs)/graphene hybrid structures," said SungWoo Nam, assistant professor of mechanical science and engineering at UIUC. "Our swelling, shrinking, and adaptation steps are optimized to minimize the degree of graphene suspension around the 3D microstructures and facilitate successful 3D integration. We control the amount of substrate swelling by adjusting the time of immersion in organic solvent and the mixing ratios of monomer and curing agent of the polydimethylsiloxane (PDMS) substrate."
Varying in size from just 3.5 to 50 μm, the dimensions of the graphene microstructures developed by UIUC put them right in the middle of a range of electronic devices, including various types of photodetectors, nano antennas, and other sub-miniature components that were once only the domain of silicon-based products. According to the team, these factors, along with graphene's high carrier mobility, chemical inertness, and biocompatibility, mean that three-dimensional graphene could be adapted over even wider areas.
"We also expect that our new 3D integration approach will facilitate advanced classes of hybrid devices between microelectromechanical systems (MEMS) and 2D materials for sensing and actuation," said SungWoo Nam.
Due to the fragility of atom-thin graphene, previous methods to bend or mold it into complex shapes resulted in uneven, ill-formed objects at best, and a ruptured mess at worst. In investigating the new technique, the researchers at UIUC were diligent in their testing of the formed graphene via electron microscopy, atomic force microscopy, Raman spectroscopy, and electrical resistance measurement to confirm that it maintained its shape and consistency after forming.
"Our results demonstrate a simple, versatile, and scalable method to integrate graphene with 3D geometries with various morphologies and dimensions," said Jonghyun Choi, a graduate student in Nam’s research group. "Not only are these 3D features larger than those reported in previous works, but we also demonstrate the uniformity and damage-free nature of integrated graphene around the 3D features."
The results of this research were recently published in the journal Nano Letters.