While it's important to keep the wings of aircraft ice-free, the application of chemical deicers before takeoff can be problematic. German scientists are working on something that could help, in the form of an ice-repelling laser-based treatment for flight surfaces.
As many people will know from firsthand experience, waiting for an airliner to be sprayed with copious amounts of deicer is a hassle, potentially delaying takeoff. What's more, the chemicals used can be quite expensive, plus they're typically not very eco-friendly.
In order to allow smaller amounts of deicer to do the same job, some aircraft now incorporate heating elements in key areas of their fuselage, or they use setups that divert hot air from their engines to those same areas. The new system is intended to further minimize the need for deicers, perhaps even making them completely unnecessary.
Being developed via a collaboration between the Fraunhofer Institute for Material and Beam Technology, Airbus and the Dresden University of Technology, it utilizes a variation on an existing technique known as Direct Laser Interference Patterning (DLIP).
Putting it simply, DLIP involves splitting a single laser beam into two or more "sub-beams." When those beams are focused onto a surface at the same time, their overlapping light waves create interference patterns – those patterns are in turn used to etch three-dimensional nano- or microscale structures into the surface. Up to one square meter (10.8 sq ft) of material can be treated per minute.
In lab tests, the modified DLIP process was used to apply 3D multi-layered microstructures to the aluminum surface of a NACA (National Advisory Committee for Aeronautics)-style airfoil, simulating the leading edge of an airplane wing. Inspired by the leaf of the lotus plant, those structures present a fragmented surface, with a limited number of adhesion points for ice.
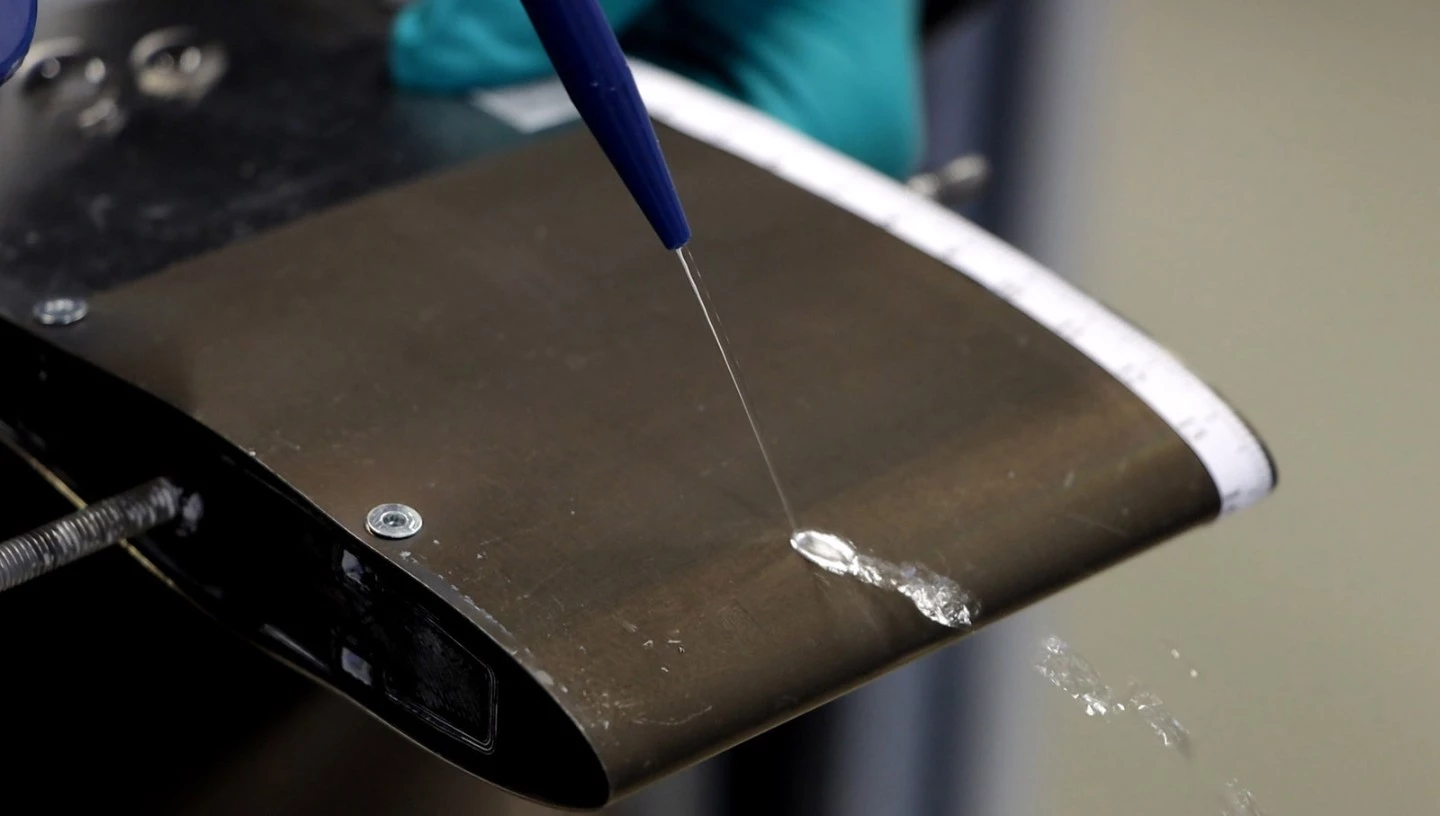
The internally-heated airfoil was subsequently placed in a wind tunnel, where it was subjected to air temperatures below -10 ºC (14 ºF), various humidity levels, and wind speeds ranging from 65 to 120 meters per second (213 to 394 ft/sec).
It was found that even when the model wasn't heated, any ice that accumulated on it would fall off on its own after a certain threshold amount had built up. And when the airfoil's heating element was used to produce 60 watts of heat, the accumulated ice melted away within just five seconds – by contrast, when the same amount of heat was produced in a non-DLIP-treated airfoil, it took 70 seconds (and thus considerably more power) to melt the ice.
The researchers now plan on testing the technology in actual flight conditions, on an Airbus A350 airliner.
Source: Fraunhofer