Although an airliner's engines may be quite loud on takeoff, its wings also create a lot of wind noise when it's landing. According to a new study, the latter problem could be addressed with the addition of a shape-memory alloy filler within the wing.
When an airliner is landing, its pilots throttle back the engines and deploy wing structures known as the leading edge slats.
These are basically flaps that run lengthwise along the front edge of each wing. When deployed, they move forward and downward relative to the wing's main body. This creates drag but also increases the wing's angle of attack, allowing the aircraft to fly at slower speeds without stalling.
As the slats are deployed, however, a gap opens up between them and the main wing. Some of the air that's moving over the wing rushes into that space and violently swirls around against the concave underside of the slat, creating a considerable amount of noise.
Previous research conducted at NASA concluded that by filling the under-slat space with an air-deflecting membrane, the wind noise could be drastically reduced. That membrane would have to sit flat and unobtrusive when the slat was pulled in during flight, but then pop out into an elongated S shape (viewed cross-sectionally) when the slat was deployed for landing.
At the time of that research, no materials were put forward as possible candidates for the membrane. Now, however, a Texas A&M University team led by Dr. Darren Hartl is suggesting that a shape-memory alloy could fit the bill.
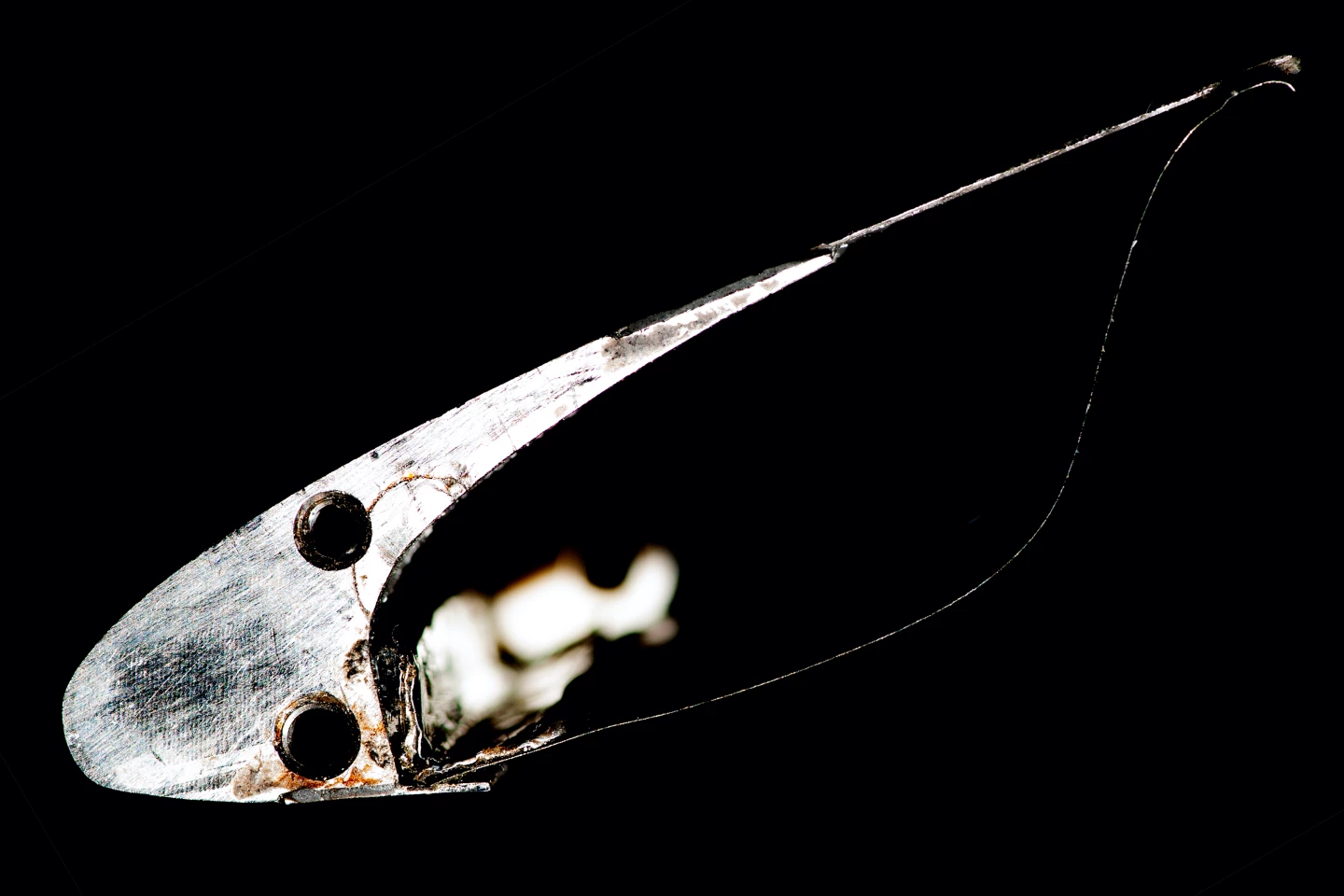
Physical models of a "slat-cove filler" made of the material will snug in against the underside of a model slat when mechanical pressure is applied, but take on the desired convex S configuration when the pressure is released. Additionally, computer models indicate that the membrane should indeed greatly reduce wind noise by lessening air circulation.
A carbon-fiber-reinforced polymer composite membrane also showed promise in the computer simulations, although it would only work within a narrow range of wing/slat designs.
Hartl and colleagues are now planning on conducting wind tunnel tests of scaled-down model aircraft wings equipped with the shape-memory alloy slat-cove filler. They are also investigating whether other shapes might work, as the S shape requires the membrane to be quite large and thus potentially heavy.
A paper on the research, which also involved scientists from the NASA Langley Research Center and the University of Bristol, was recently published in the Journal of Aircraft.
Source: Texas A&M University