Is 3D printing the future of affordable housing? It certainly seems possible. The burgeoning technology has the potential to construct houses faster and cheaper than with traditional building techniques, and has already resulted in a low-cost housing project in Mexico. Now global housing nonprofit Habitat for Humanity is creating a 3D-printed home that it hopes will become a blueprint for affordable housing.
The prototype house is currently under construction in Tempe, Arizona, and is expected to be completed by September and serve as home to a low-income family. It will have a usable floorspace of 1,738 sq ft (161 sq m) and will contain three bedrooms and two bathrooms, as well as a living room and kitchen, plus a garage.
More ambitiously though, Habitat for Humanity aims to build on its experience making the home to produce a series of affordable 3D-printed houses. How affordable? We reached out to the nonprofit and received the following statement.
"We've not yet tallied the complete cost of the home because almost everything from the slab to the lighting was in-kind donated as is often the case with Habitat homes. This first one will not be cheaper simply because the lead time and costs around a 'prototype' process like this. Our hope is that because we’ve been able to prove the technology, others can help us scale it to be more efficient and more cost effective."
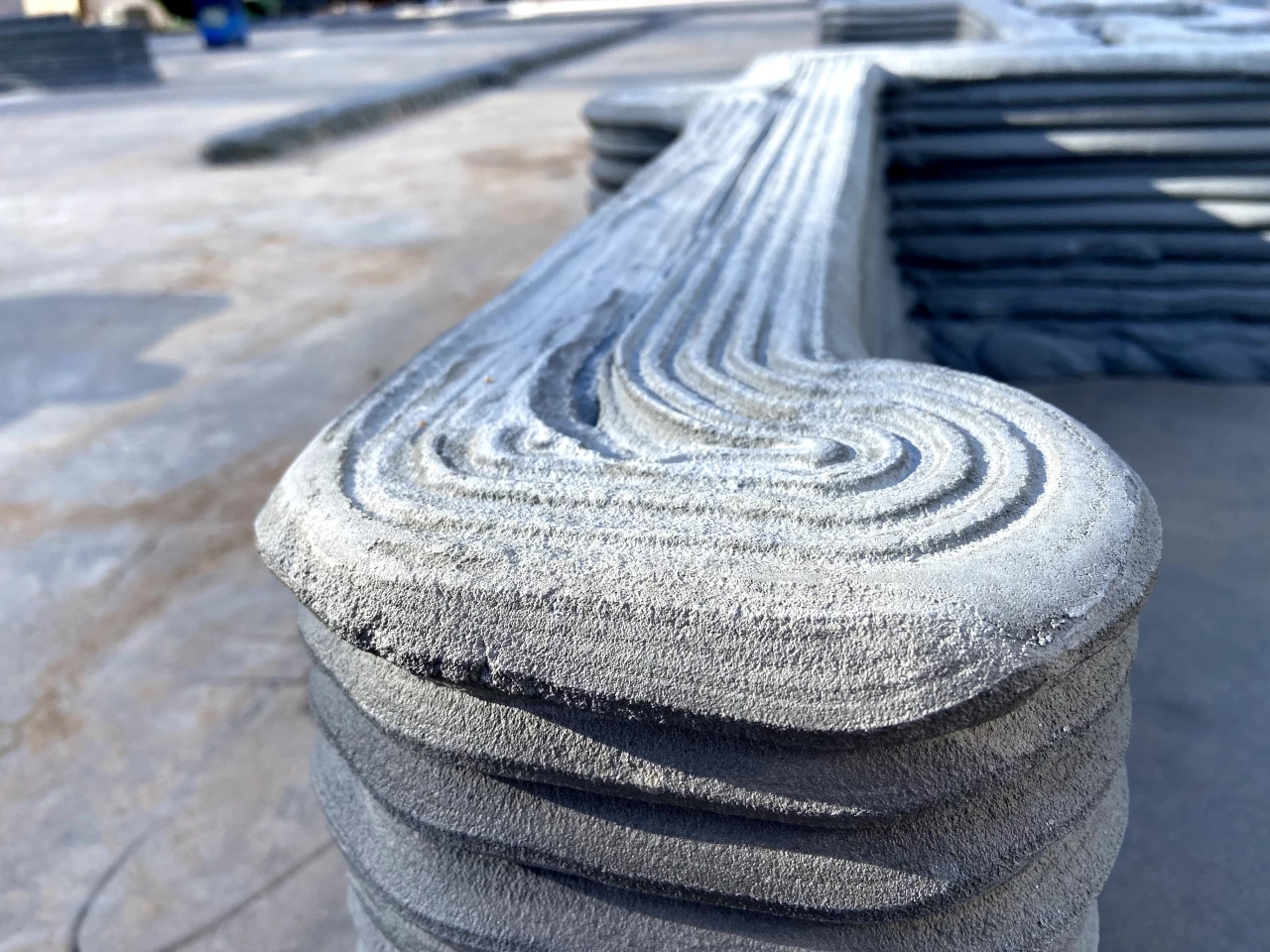
The home is being created in collaboration with formwork and scaffolding firm Peri using the same BOD 2 model of 3D printer used in Peri's other 3D printed housing project in Germany. The build process is essentially the same as other 3D-printed architecture projects we've covered, involving the 3D printer extruding a cement mixture out of a nozzle in layers, building up the basic structure, with humans doing the rest of the work, such as fitting windows and doors, for example.
It will be wired ready for solar power and is slated for the LEED green building standard, as well as an IBHS Fortified Home designation, which was established to prove a building's resiliency to severe weather.
"This is really a moonshot opportunity for Habitat for Humanity Central Arizona," says president and CEO of Habitat Central Arizona Jason Barlow. "When we consider the housing issues facing Arizona, the need for affordable homeownership solutions becomes clear. If we can deliver decent, affordable, more energy efficient homes at less cost, in less time and with less waste, we think that could be a real game-changer. Just think of the implications."
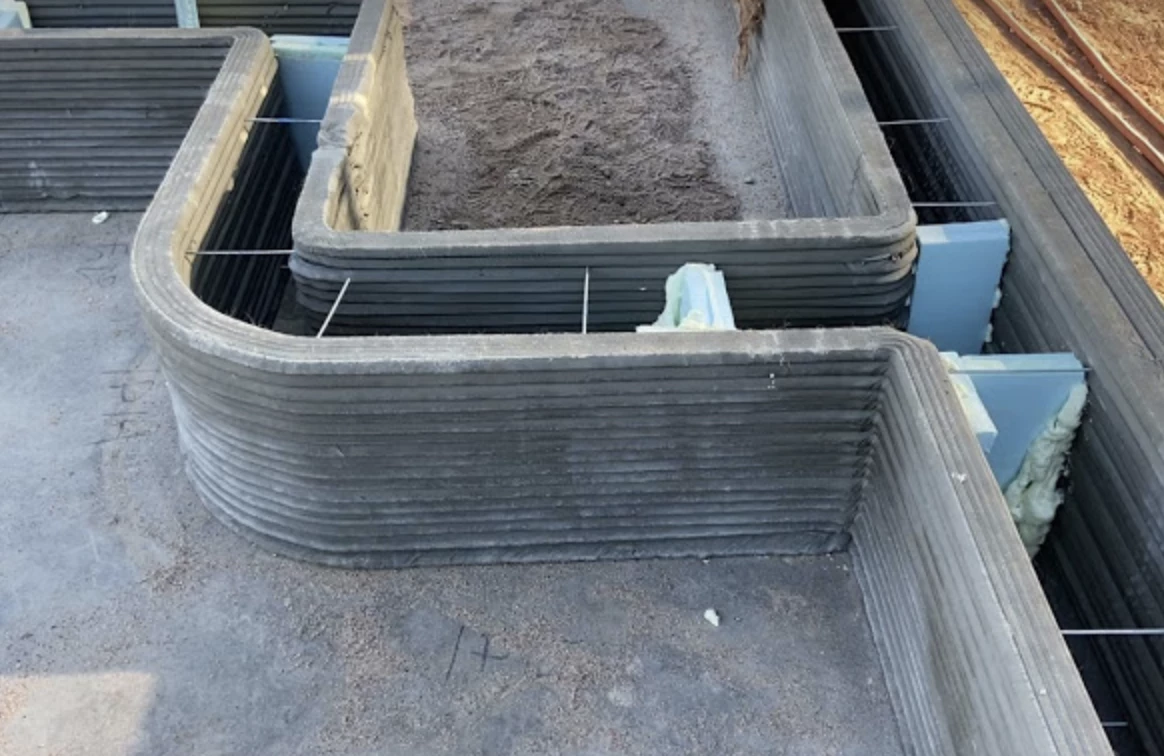
Though affordable housing seems like the most obvious fit for 3D-printing tech, it's also worth pointing out that there are some projects exploring the opposite end of the market too, like the development in Austin, Texas, which includes luxury 3D-printed homes starting at a cool US$450,000.
Source: Habitat for Humanity