An ambitious development of a hundred homes named Wolf Ranch looks set to become a major step forward in 3D-printed construction going mainstream in the United States. Located near Austin, Texas, the project's first model home has now been revealed ahead of the first batch of residents arriving in September.
Described as the largest-scale development of 3D-printed homes in the world, Wolf Ranch is being built by Lennar and Icon, and is co-designed by high-profile architecture firm the Bjarke Ingels Group (BIG). The project is part of a larger development by Hillwood Communities Development that will also contain traditionally built homes.
The 100 3D-printed houses range from 1,500 - 2,100 sq ft (roughly 140 - 195 sq m), all on one floor. They come in eight different floorplans and offer either three or four bedrooms and two or three bathrooms. Their overall design is inspired by traditional Texas ranches.
The completed home pictured is being used for would-be buyers to get an idea of what living in a 3D-printed house is really like. At first glance it looks much like any other modern home, though on closer inspection it features the telltale ribbed walls, which reveal it was created using a 3D printer. It looks light-filled and spacious inside, with generous glazing and a large open living area with included kitchen.
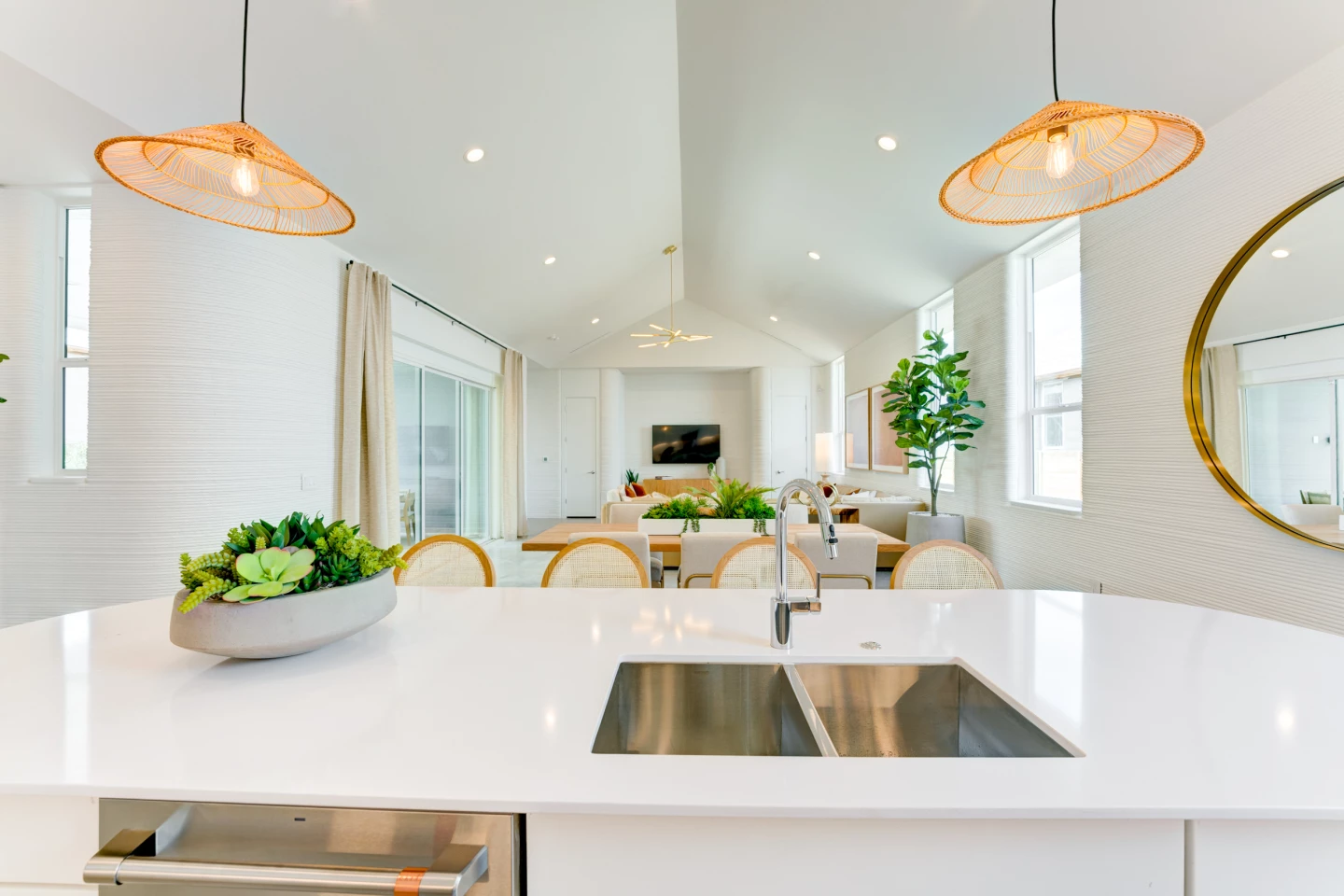
The homes will reduce their grid-based energy usage with a solar panel system. They will also boast some smart home tech, such as a Ring Video Doorbell, Wi-Fi-operated lock, and a smart thermostat.
The Wolf Ranch development is being constructed using Icon's own Vulcan 3D printers. The build process is similar to other 3D-printed projects we've covered before and involves the 3D printer extruding a cement-like proprietary mixture called Lavacrete out of a nozzle in layers, building up the basic structure of the home. Human builders then finish off the house by adding a roof, doors, windows, and anything else required.
There are currently six completed 3D-printed homes available for purchase in the Wolf Ranch 3D-printed development. Pricing ranges from US$475,990 to $559,990 and those interested can virtually tour the homes using the source link below.
Source: Icon