Lured by their superior sustainable qualities, high-rise developers around the world are increasingly turning to timber materials for construction, and a newly completed office tower in Australia is the latest shining example of this. Billed as the nation's tallest timber structure, 25 King tastefully pairs its wooden skeleton with a shimmering glass facade, leaving the exposed timber beams to become part of the aesthetic inside as well as out.
Opened last week, 25 King by Australian architecture firm Bates Smart stands 10 stories and 45 m (147 ft) tall in Brisbane. According to the developers, this makes it Australia's tallest timber structure and pushes the boundaries of building design for the commercial world.
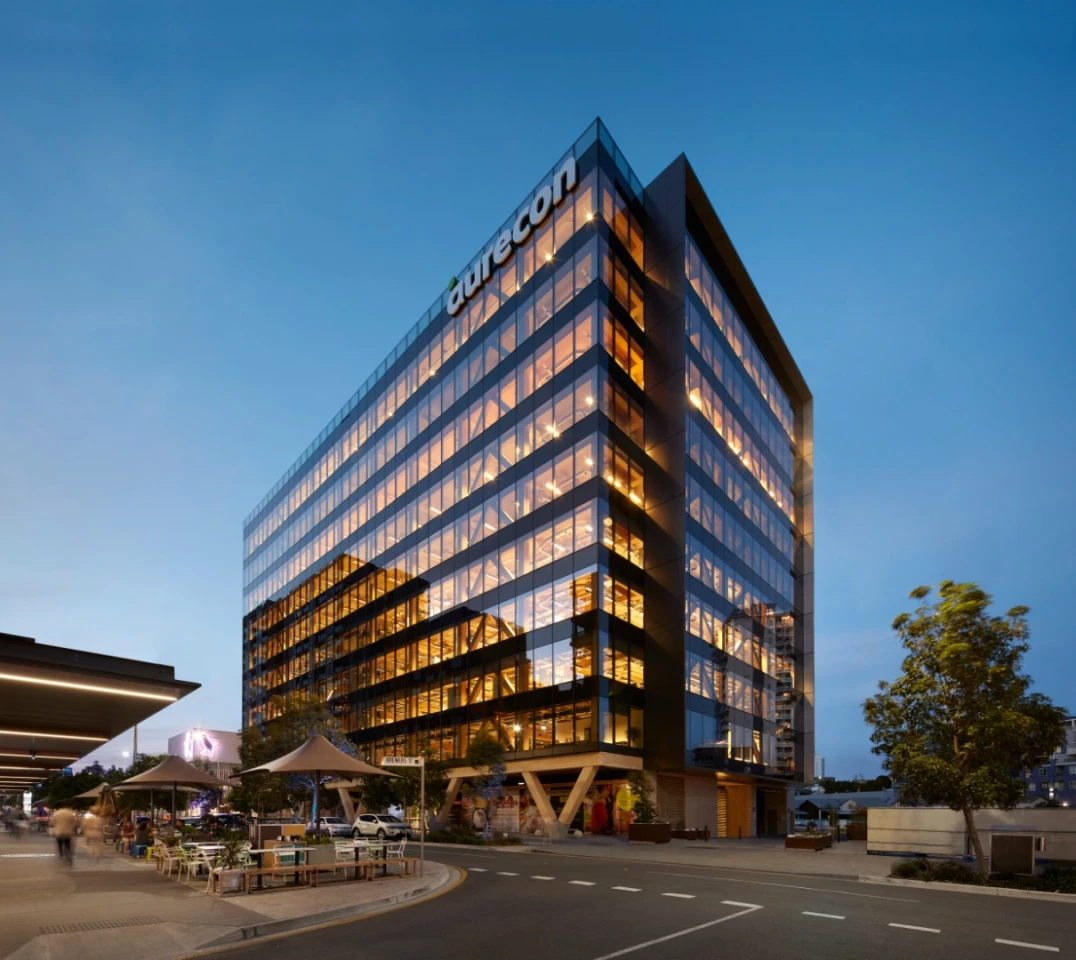
Where steel and concrete might have otherwise been used in the construction, the firm deployed forms of highly engineered wooden materials instead. These consist of Glulam (glued laminated timber) and CLT (cross laminated timber), and their manufacturing results in far lower carbon footprint than that of resource-intensive concrete and steel.
This also meant that a lot of the building's components could be pre-fabricated off-site, greatly reducing on-site wastage and construction time with the entire structure going up in 15 months. Floor by floor, huge exposed V-shaped columns were stacked on top of one another to support the timber slabs used for floorplates and exposed ceiling soffits. This has the added benefit of creating a pleasant aesthetic inside.
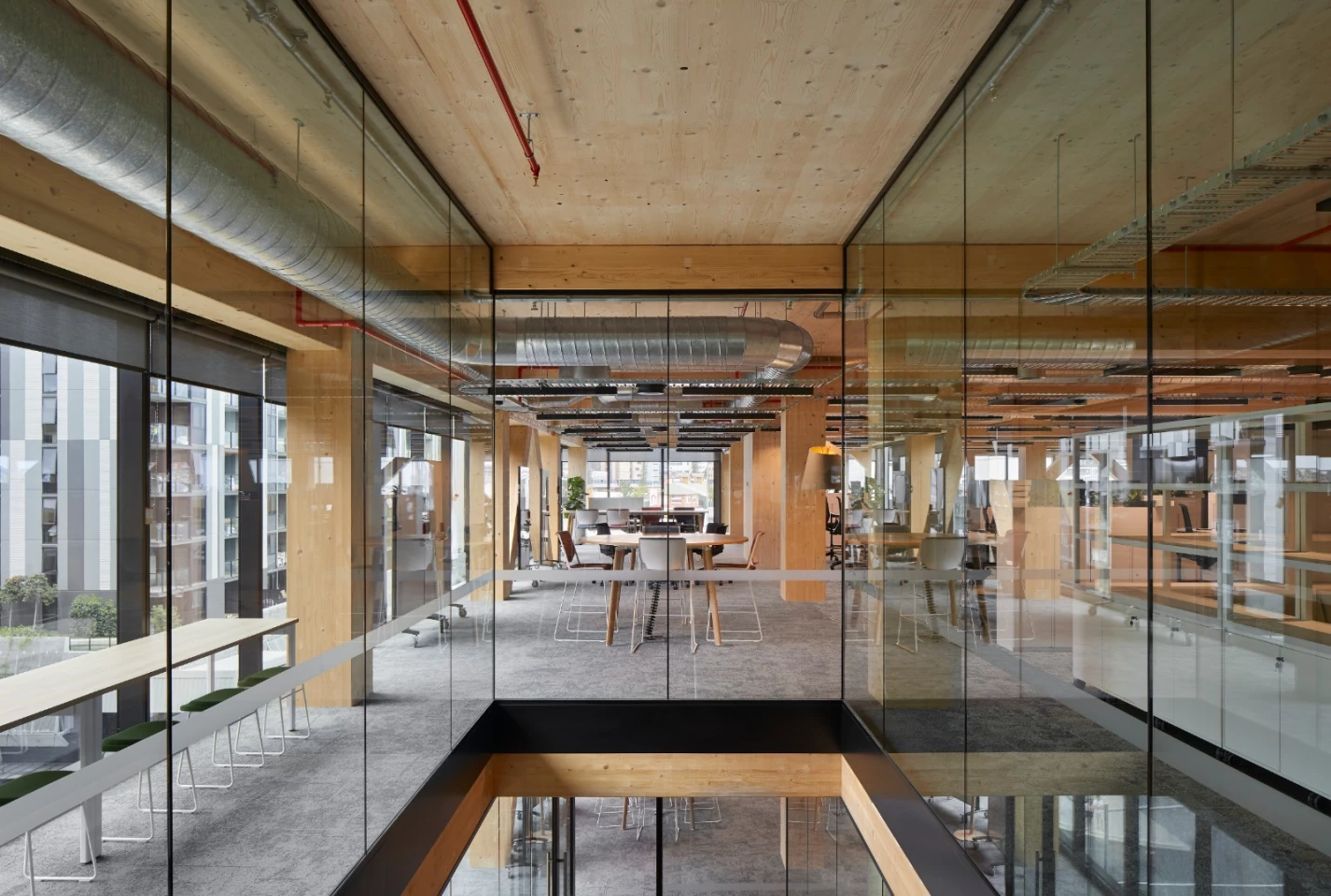
"25 King reflects a turn towards making buildings and spaces that are warm and inviting," says Philip Vivian, director of Bates Smart. "We know that people want to connect to nature, and using timber on the exterior and interior of buildings helps complete the connection, making people feel more at ease within the built environment."
The bottom floor consists of a shaded colonnade home to cafes and restaurants, while the nine floors above it are used as open-plan office spaces. Support columns are arranged strategically throughout to keep their individual size to a minimum and allow maximum flexibility of the space.
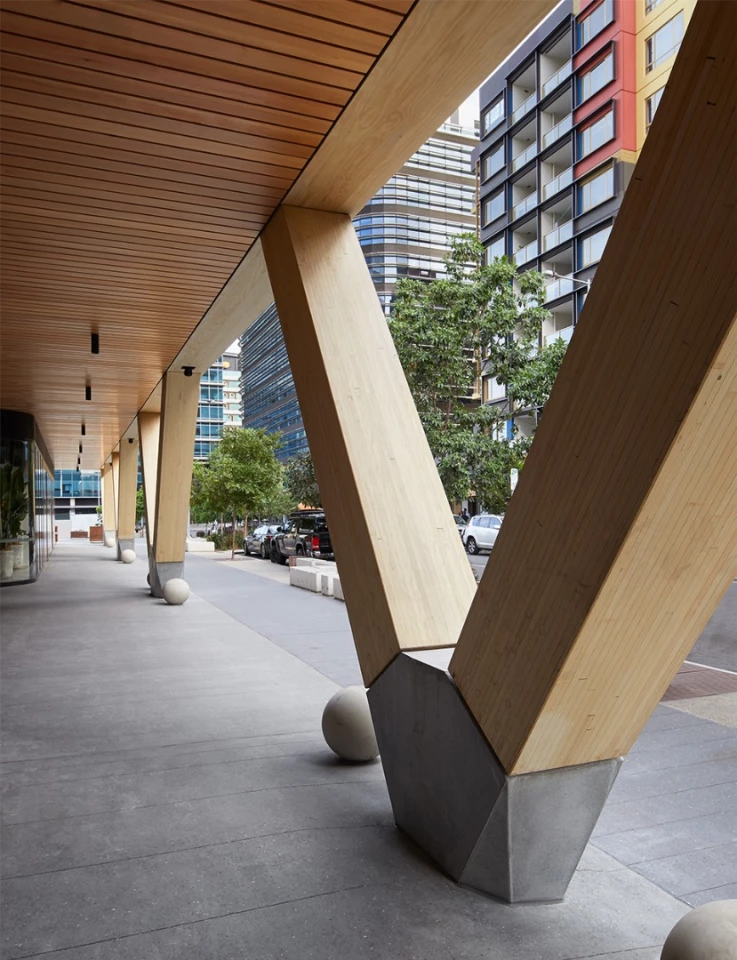
According to Bates Smart, its method of construction when compared to conventional building practices brought a 46 percent reduction in energy use, a 29 percent reduction in potable water use and a 74 percent saving in embodied carbon, thanks to the C02 sequestered in the timber structure. Other sustainable features include rainwater harvesting, energy efficient lighting, a greenery-covered wall in the entrance lobby, "optimized air-conditioning" and aluminum sun-shading to keep the interior cool.
"Each time an engineered timber project completes, architects learn more about CLT's potential as a new building material and how we can work and innovate with it on all types of buildings," says Vivian. "This building marks a genuine commitment to CLT from the industry. It's exciting to see the ideas take hold and evolve across the globe, and we're happy to contribute with the lessons we've learned on 25 King."
Source: Bates Smart