It wasn't that long ago that bamboo-framed bikes were thought of as a weird rarity. Thanks to its combination of durability, stiffness and vibration-damping characteristics, however, the material has been gaining popularity in recent years. That being said, some designers still find that the random nature of pure bamboo makes it a little too unpredictable for producing frames of a consistent character and quality. That's why two frame builders have developed some interesting work-arounds.
Bamboo, meet LamBoo
Slovakian mechanical engineer Braňo Mereš, who previously brought us the eye-catching X-9 Nighthawk concept bike, is now starting to make frames out of what he calls "LamBoo."
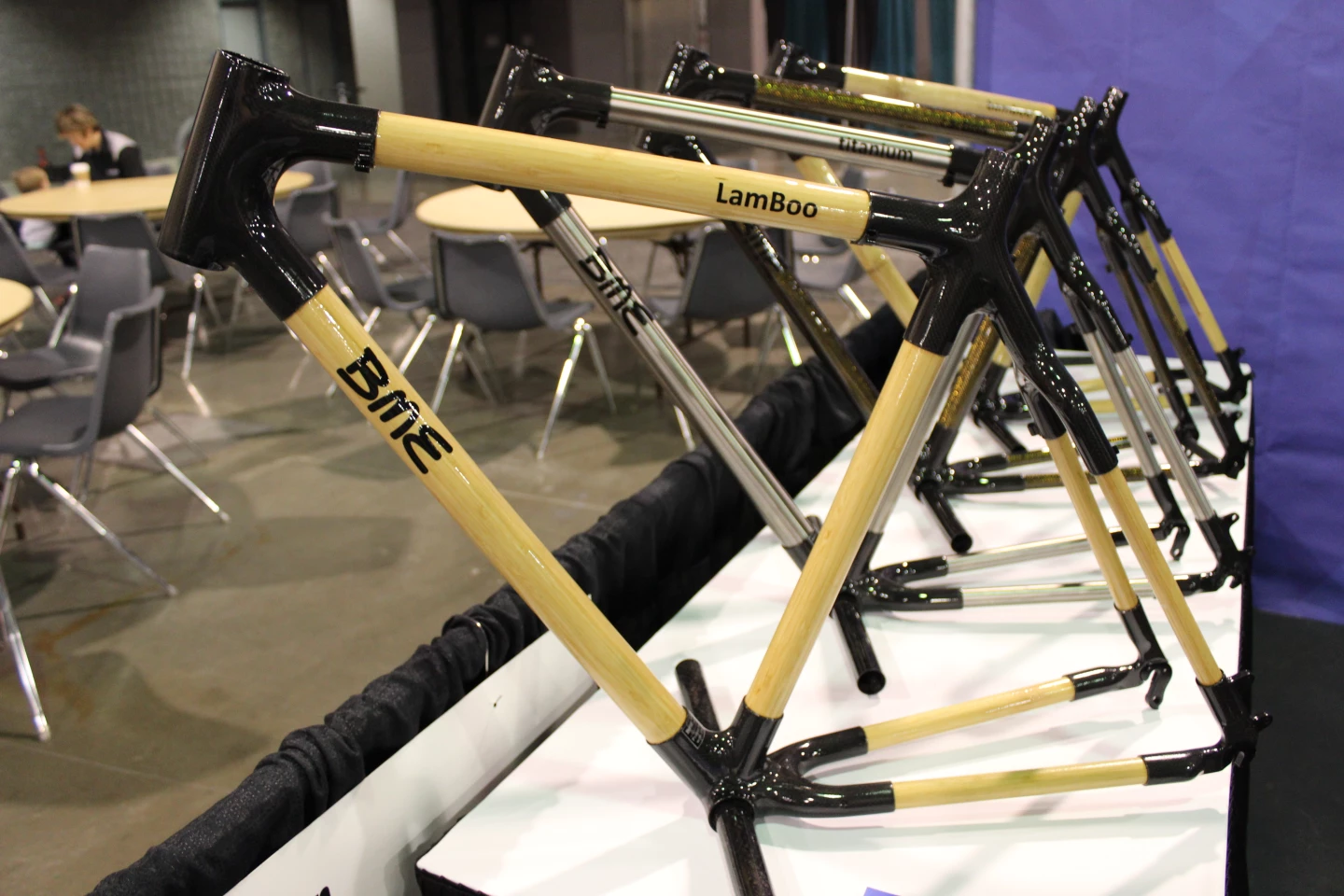
To produce his LamBoo tubes, he starts by wrapping thin sheets of epoxy-covered bamboo veneer around a cylindrical steel form known as a mandrel. He then places it in a mold, where it's subjected to 25 tons (22.7 tonnes) of pressure. Once it's removed from the mold and the mandrel is withdrawn, the result is a laminated bamboo tube that reportedly has the same good qualities as regular bamboo, but with a much more uniform and tweakable composition.
"I was building frames using natural bamboo, and it was quite difficult finding suitable pieces, because every one has different wall thicknesses, different properties," Mereš told us at the North American Handmade Bicycle Show, where his frames were on display. "Now I can design the properties, I can have 100 frames with the same properties."
Weaving it all together
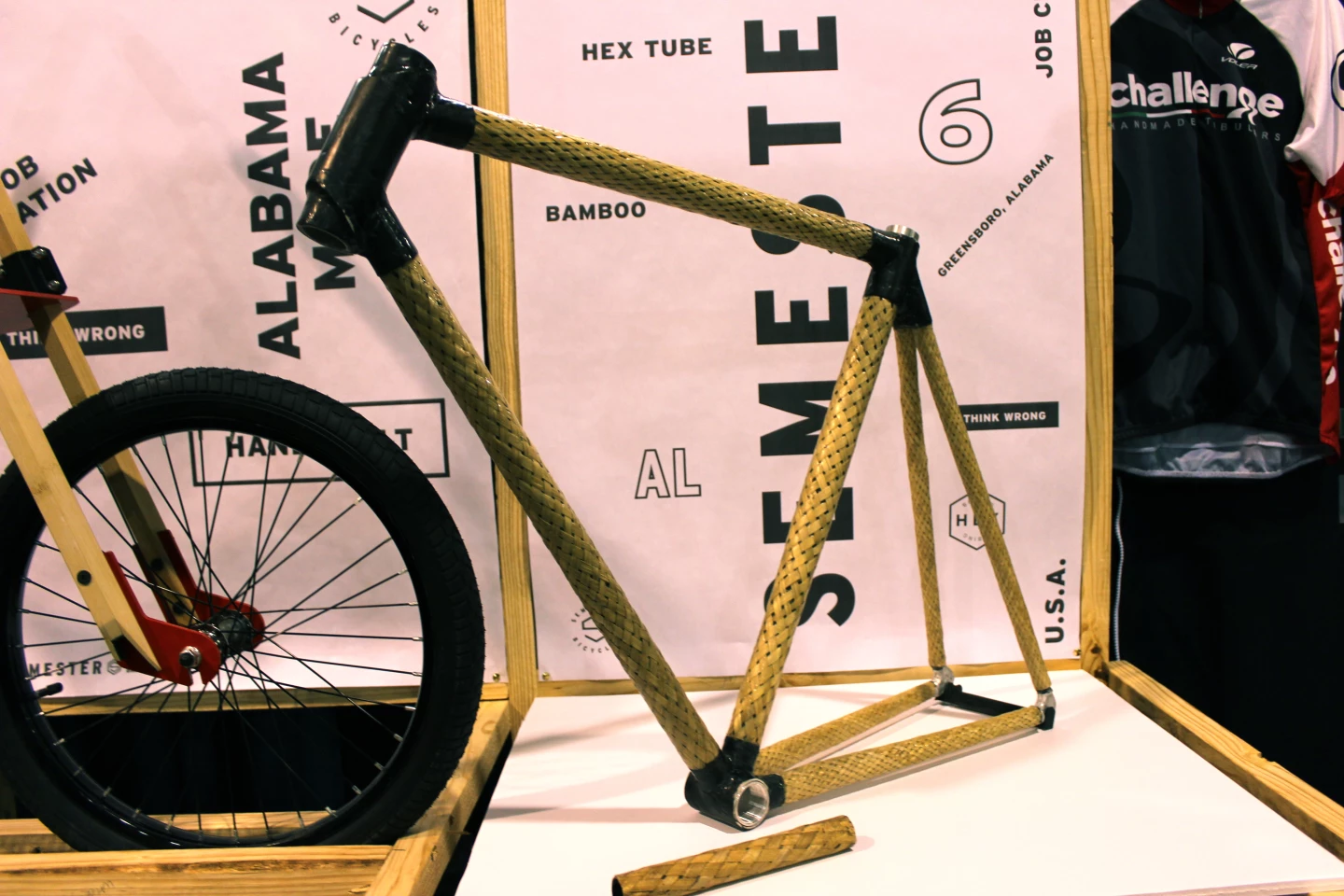
Elsewhere on the showroom floor, Alabama-based HERObike was showing off its own unique wares. Among those was a bamboo composite frame made by Lance Rake, a professor of industrial design at the University of Kansas.
Instead of laminated layers of bamboo, he used thin strips of the material that were woven together into flat mat-like sheets. Each sheet was then rolled into a tube shape, with an uncured cylindrical carbon fiber "sleeve" inside of it, and a sealed-ended length of bicycle inner tube inside of it. The whole tube-within-a-tube-within-a-tube combo was then placed in a cylindrical mold.
When the inner tube was subsequently inflated, the air pressure caused it to press against the carbon fiber, pushing it up against the inside surface of the woven bamboo. Once the carbon fiber had set, the mold was opened and the inner tube was pulled out, resulting in a rigid tube made of woven bamboo on the outside, bonded to carbon fiber on the inside.
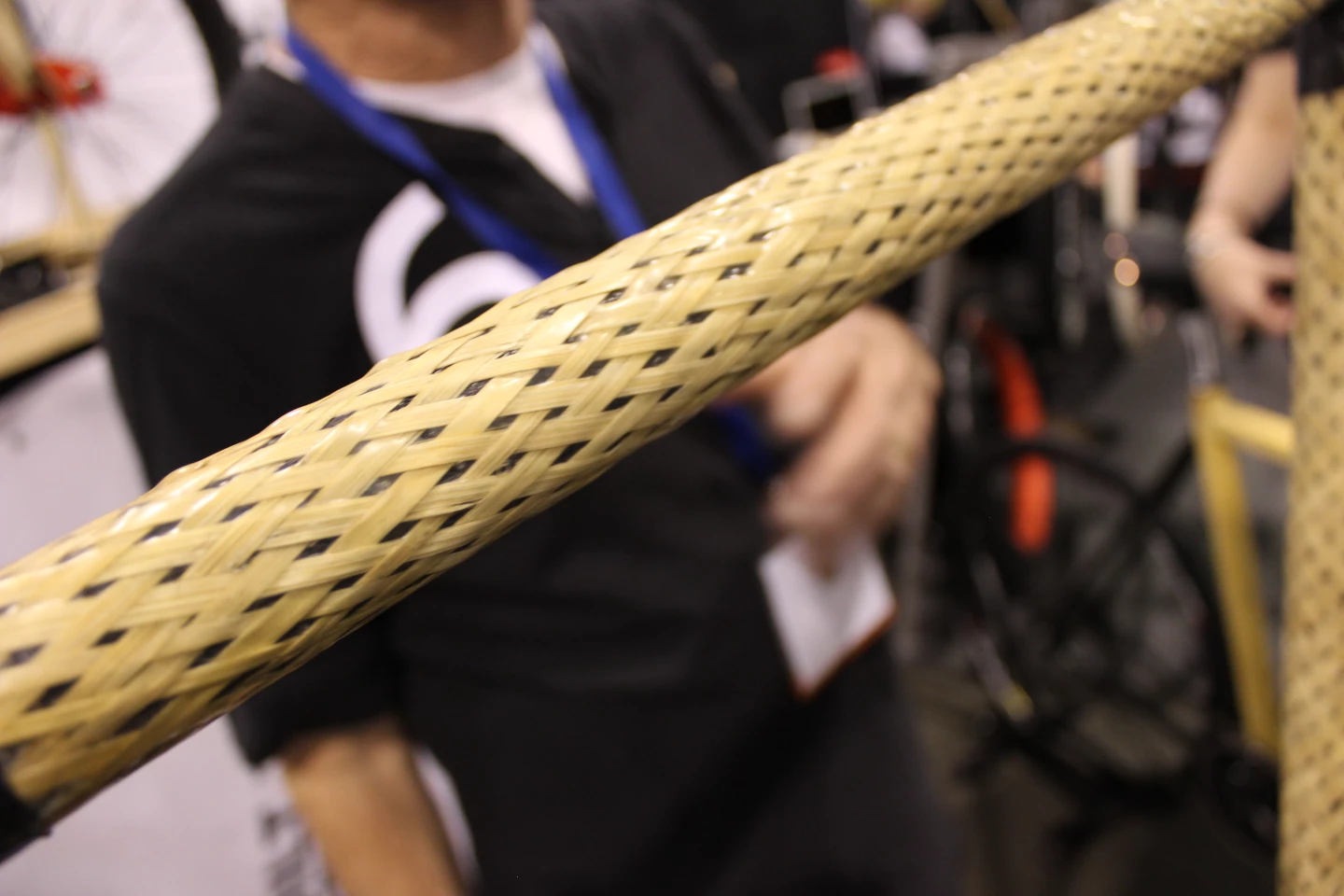
According to Rake, the flexible woven bamboo can be pulled or compressed before curing to alter the diameter of the tube, plus it can be molded into tube shapes that aren't completely straight or cross-sectionally round. Although the one prototype frame is currently all that there is, he hopes to make a whole line of woven bamboo bikes.
"A lot of the things I wanted to find out, I'm finding out," he said. "I think the construction is viable, the direction's good, the weight's great ... I like it."
Company pages: BME Design, HeroBIKE