Bicycle seats are padded with foam, and that's the best way of doing things … right? Well, maybe not. Specialized has teamed up with Silicon Valley tech company Carbon, to create a 3D-printed saddle that's reportedly comfier than "old school" foam-filled models.
Known officially as the S-Works Power Saddle with Mirror, the seat is made via Carbon's proprietary Digital Light Synthesis process. Previously used to produce 3D-printed shoes for Adidas, the technique involves projecting ultraviolet light through an oxygen-permeable window into a UV-sensitive liquid resin. That resin then cures into a desired shape. The technology is said to be much quicker and more efficient than traditional "additive manufacturing"-style 3D printing, in which objects are built up by depositing successive layers of material.
Instead of consisting of a separate outer covering and inner padding, the finished elastomer resin saddle is all one piece … although that piece is in turn made up of a complex lattice-type structure consisting of 14,000 tiny struts, and 7,799 nodes between them. This is the Mirror technology, and it allows for each strut to be tuned individually while still in the design process – "mirroring" a pressure map of a typical human butt.
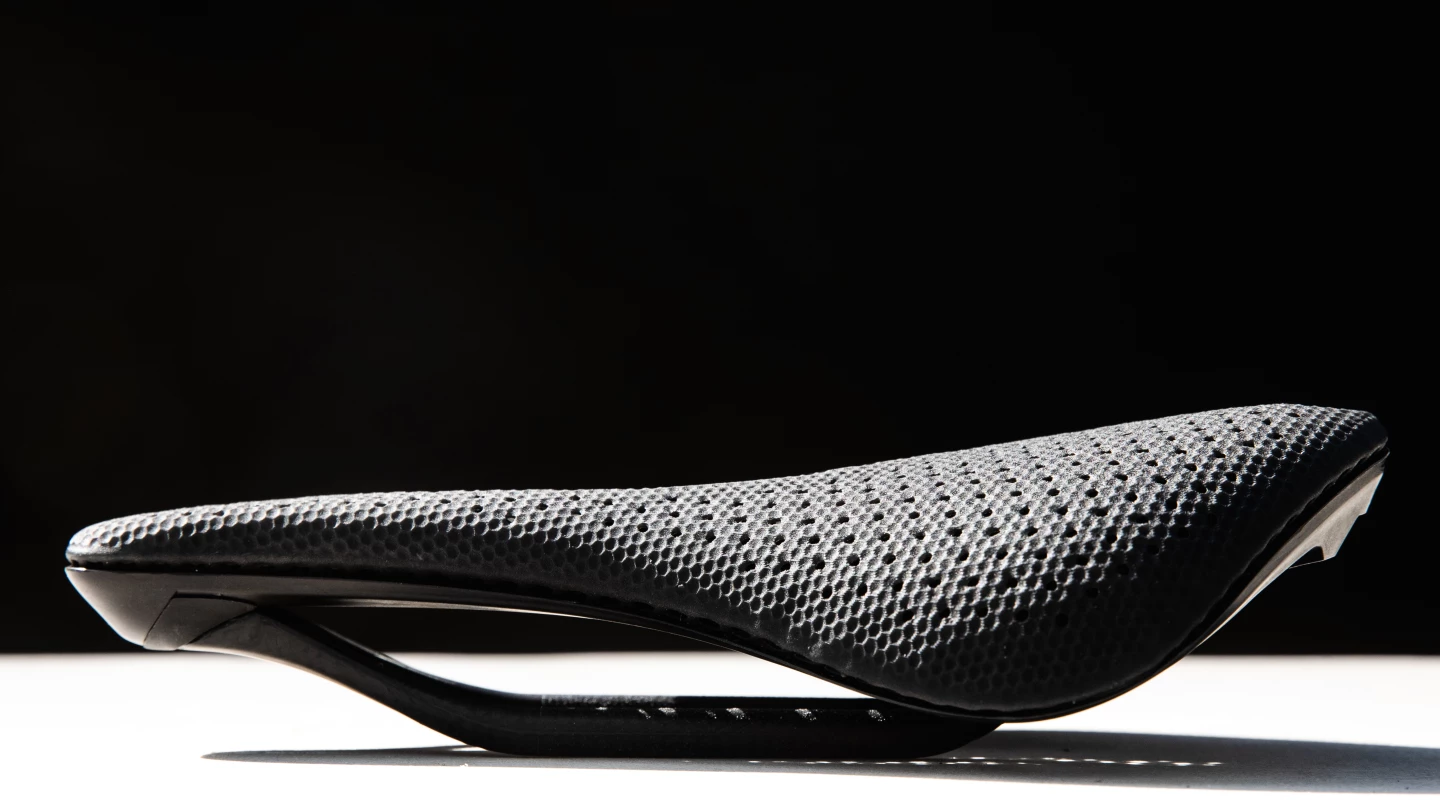
As a result, the material is claimed to excel at absorbing impacts and then quickly rebounding, in a sense providing a suspension for riders' derrieres. It's also said to be very good at dispersing pressure on the user's "sit bones" and tender bits, improving stability, and maintaining breathability.
Plans call for the S-Works Power Saddle with Mirror to be commercially available sometime next year. No pricing information has been released yet, although it will be made in two widths – 143 and 155 mm. The smaller of the two reportedly tips the scales at 189 grams (0.4 lb), which is "on par" with the weight of Specialized's current non-3D-printed Power Saddle.
There's more information in the following video.
Sources: Carbon, Specialized via Pinkbike