If the Bloodhound Supersonic Car (SSC) team makes good in its attempt to break the land speed record, the car will be traveling at 1,000 mph (1,609 km/h). At such speeds, the wheels will be spinning so fast that hitting even the smallest pebble could be catastrophic. To protect both the car and the driver, the designers of Bloodhound have had to come up with some high-tech answers to building the wheels and protecting against their failure.
Blasting across salt flats at beyond the speed of sound takes more than engines punching out insane amounts of power. It also requires wheels that can withstand stress than make an F1 race car look like a kiddie wagon. Built by a consortium of companies, the wheels of the Bloodhound have to support 7.5 tonnes (8.2 tons) just standing still, so its no wonder that each 90 cm (35.4 in) wheel disk weighs 91 kg (200 lb).
But it's when Bloodhound makes its run that the problems really begin. At top speed, the wheels will be turning at 10,200 rpm – and even this is an approximation because the Bloodhound is expected to outpace the wheels, so it isn't certain how fast the wheel will actually be turning at top speed. When going flat out, the wheels generate 50,000 radial g at the rim, which means that a 1 kg (2.2 lb) bag of sugar set on the rim would weigh 50 tonnes (55 tons) or as much as a juggernaut lorry.
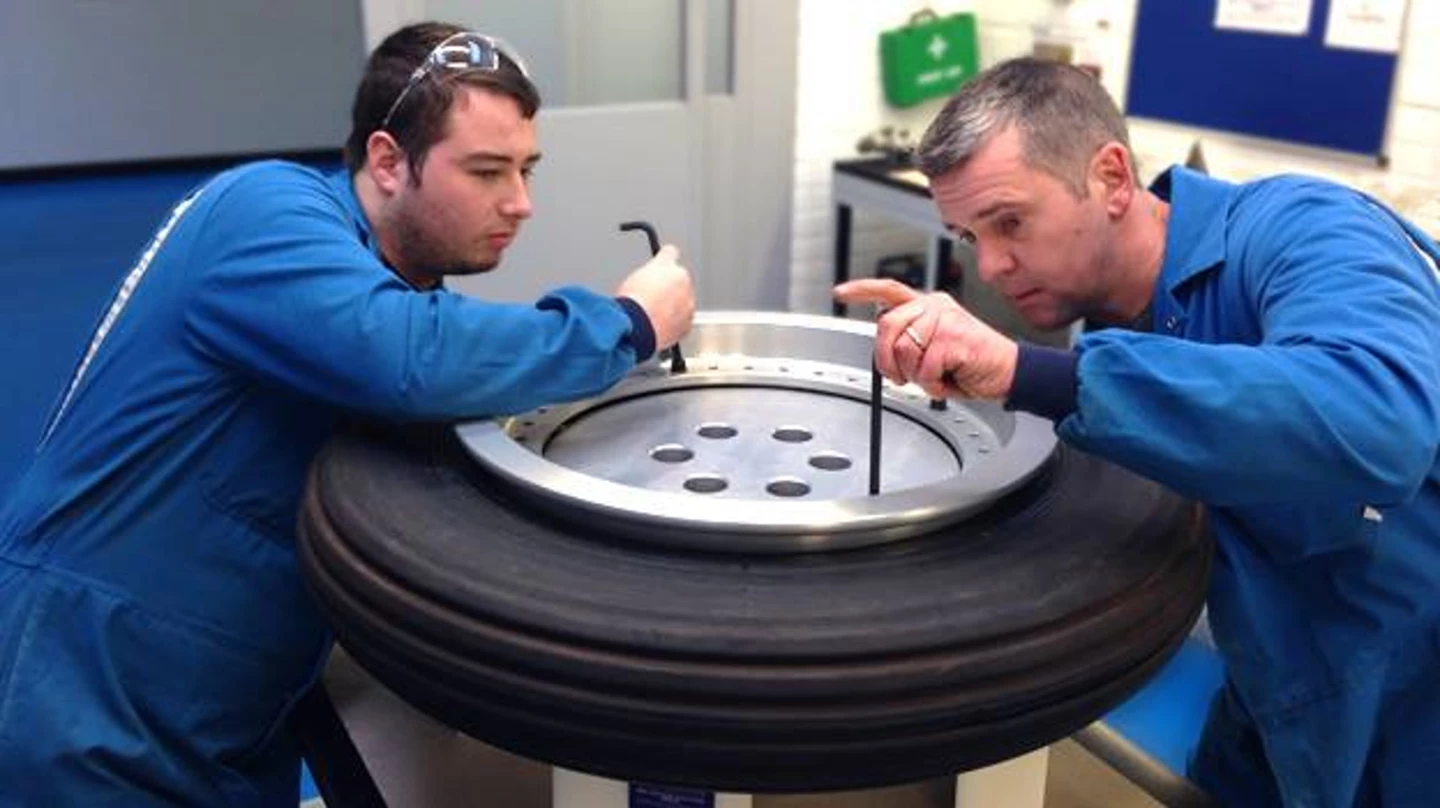
To handle that sort of stress, the wheel discs are made of a special aluminum alloy created for cutting-edge aerospace applications called 7037, which includes traces of zinc, copper, and manganese. This is forged into a "cheese" in a 3,600 tonne (4,000 ton) hot press and a 20,000 tonne (22,000 ton) cold press with a high degree of precision to make sure that each wheel is perfectly balanced.
According to Bloodhound SSC, the purpose of all this heating and squashing is to press the crystalline structure of the aluminum to remove any voids and form a stronger, more compact matrix that has a radial pattern like the spokes of a wheel.
However, such strengthening, followed by precision machining by the Castle company and testing by Rolls Royce, has its limits and should the ground crew overlook a single stone or the car kick one up from beneath the desert floor, the results could be catastrophic. A foreign object hitting the wheel could cause to lose its balance, which would quickly damage bearings and increase the wobble until the wheel tore itself apart in a manner normally only seen in an exploding jet turbine.
Another danger is that the front wheel could fire a pebble at the rear wheel or into the body of the car at supersonic speeds. This could be extremely dangerous for the driver Andy Green despite the carbon composite cockpit. To protect against this, Morgan Advanced Materials is developing lightweight composite ballistic panels to guard the cockpit and other vital areas.
These panels are slightly curved to fit the cockpit and other points, but this has the additional advantage of providing a surface for flying objects to strike at an angle rather than dead on. The panels are made out of millions of woven glass fibers that act as energy absorbers. They work not by stopping the projectile, but by dissipating the energy. According to Morgan, as the projectile hits, it tears the fibers. Each tear takes energy and as the projectile rips through the laminated mats, it loses a lot of energy and minimizing damage.
Morgan has been subjecting the glass fiber mats to tests involving a gun designed to produce the force of a cricket ball traveling at 2,000 mph (3,218 km/h). The company fired metal sabots that simulate the largest piece that could come off the wheels prior to a total failure, and results so far have been positive. The test panels look as though they've been attacked by a buzz saw, but they manage to adequately decelerate the projectile.
If all goes according to schedule, the Bloodhound will make its attempted record run next year in South Africa using its triple power plant of a hybrid rocket motor, F1 racing engine, and the jet engine from a Typhoon fighter.
The video below shows the composite ballistic panels being tested.
Source: Bloodhound SSC