As autonomous vehicle technology advances, their designers and the companies behind them are exploring new ways to exploit them. Daimler has been developing heavy-duty applications for self-driving vehicles for a while, and its most recent take is particularly practical – airport snowplows.
An airport is a closed system of paved surfaces, and most modern airports already have GPS markers and other technologies to indicate runway locations and the like. Daimler thinks they are ripe for automation, so the company is demonstrating automated snow removal operations at Germany's former Pferdsfeld airbase. The project is being called the Automated Airfield Ground Maintenance (AAGM) project.
The project includes four Mercedes-Benz Arocs tractors outfitted as snowplows. The benefits from this idea are obvious. Snow removal at airports is crucial – an autonoumous approach would save staff scheduling, could clear runways with more precision, and would have lower costs.
This snowplow project was done in cooperation between Daimler's Lab1886 innovation incubator and Fraport AG, which operates one of the world's largest air traffic hubs. Joint testing is ongoing and involves key areas of research and development that Daimler has not undertaken before.
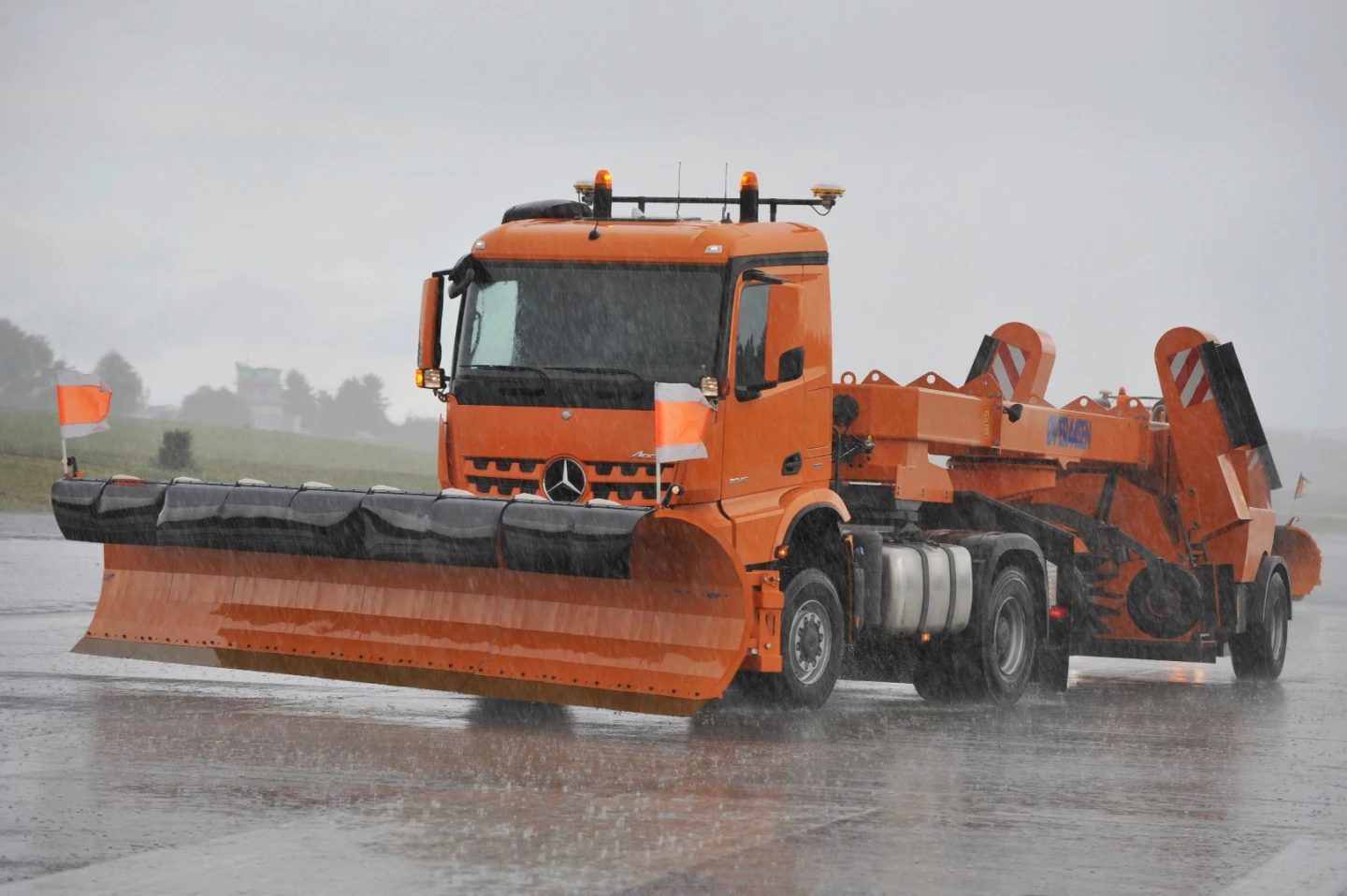
The development of heavy-duty, commercial vehicle automation has been going on for some time at Daimler. We've reported on Daimler self-driving trucks driving on the Autobahn and platooning in Germany, for example. This current project, however, involves telematics-based vehicle control technologies the company has not used previously, as it involves remote-control options. Daimler is calling this the Remote Truck Interface (RTI).
Vehicle functions are remote-controlled even as the trucks exchange data with one another. This allows the controller to operate not just a single truck, but multiple trucks in unison – up to 14 of them. The trucks can lead or follow in convoy, as with HPC systems, but can do so in formation through secured, closed-loop control systems.
The RTI design utilizes dual GPS tracking, vehicle-to-vehicle communications technologies, and secure remote control unit connections. A full data exchange between vehicles and the control unit takes place every 0.1 seconds using Digital Short Range Communications (DSRC) technology. Daimler envisions the snow removal as only the beginning of precision remote-controlled convoys of work machines. All manner of runway maintenance could be done, of course, but applications for mining, container terminals, and others are feasible.
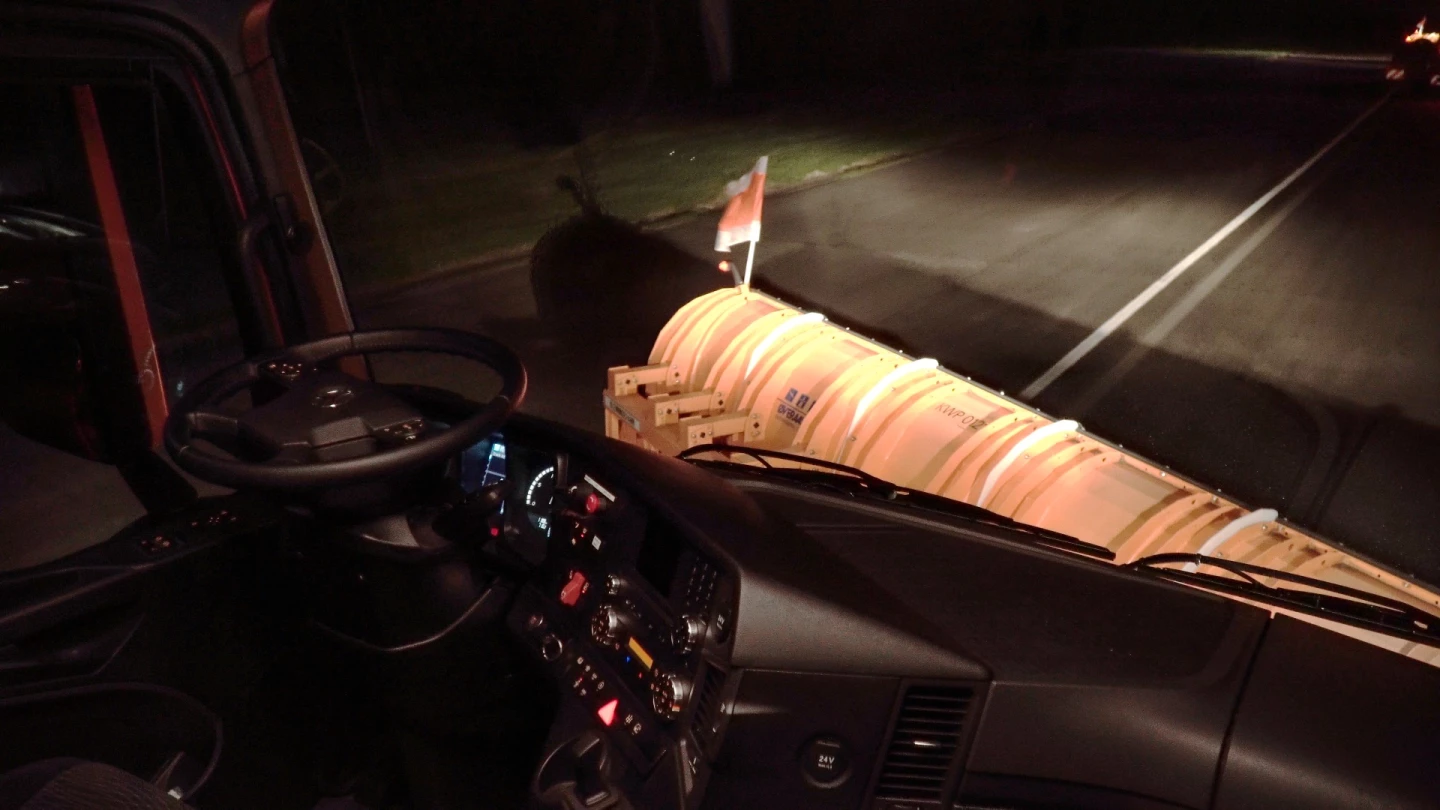
Safety is obviously a big focus for the project, too. "An important component of the RTI control unit is the integrated safety concept," said Martin Zellinger, Head of Advanced Engineering at Daimler Trucks. "This means that all vehicle functions are monitored. The safety routine is executed as soon as an error occurs. In this way we can ensure that the vehicles can be stopped safely and quickly if needed, and can then simply be operated manually."
Source: Daimler