T-Omega's pyramid-based floating wind turbines are designed with the sole common-sense focus of keeping the cost of offshore wind down to an absolute minimum. With wave tank testing done, the company has now launched its first real-world prototype.
The idea is quite simple: get rid of the large central pole that offshore turbines have inherited from land-based units. A single central tower will only stay upright, reasons T-Omega, if you've got about four tons under the water for every one ton above the water. And given that wind power needs to scale up to become efficient and cost-competitive, that means an enormous amount of weight, a correspondingly high materials bill, and all manner of logistical issues around manufacturing, installation and maintenance.
T-Omega's idea replaces the massive single-sided pinwheel generators of traditional designs with a double-sided axle supported at both ends, and instead of a single tower reaching down to the waterline, you get four diagonal supports leading down to what's effectively a pyramid base, floated at its four corners. This is anchored to the sea bed with a bit of slack, allowing the whole thing to float around in response to changes in wind direction, passively orienting itself toward the wind at all times.
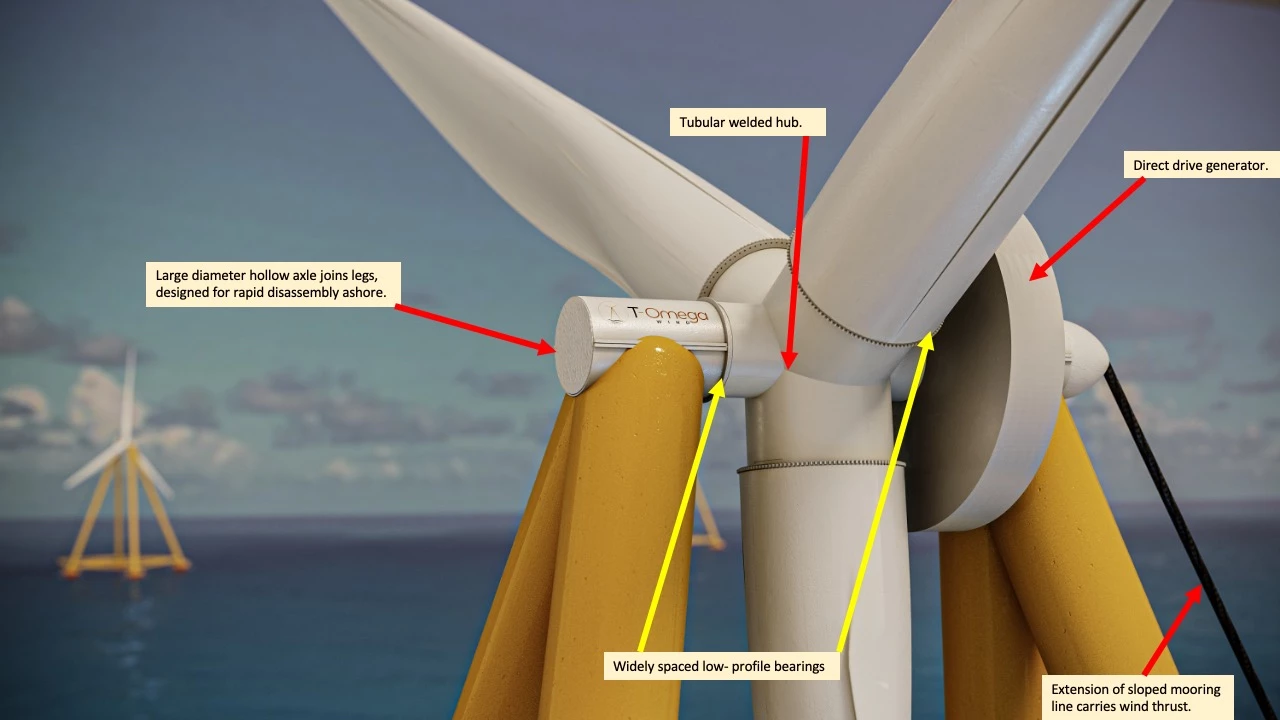
The benefits: vastly reduced upfront cost, thanks to hugely reduced materials, super-simple manufacturing and deployment without any need for specialized facilities, and a wind turbine so easy to install and unhook that you can just tow them back to a dock for maintenance. That vastly reduces operating costs, since you don't need massive crane ships and the like to get out there and fix things.
The company told us in September last year that it was targeting a Levelized Cost of Energy (LCoE) around US$50 per megawatt-hour, which would be "in the ballpark of the best fixed-bottom offshore wind available today."
Now, after wave tank testing of a 1/60th scale model that proved the design was capable of staying upright even if a full sized version was hit by freak 30-m (98-ft) waves, the company has moved to real-world testing with a 1/16th scale prototype.
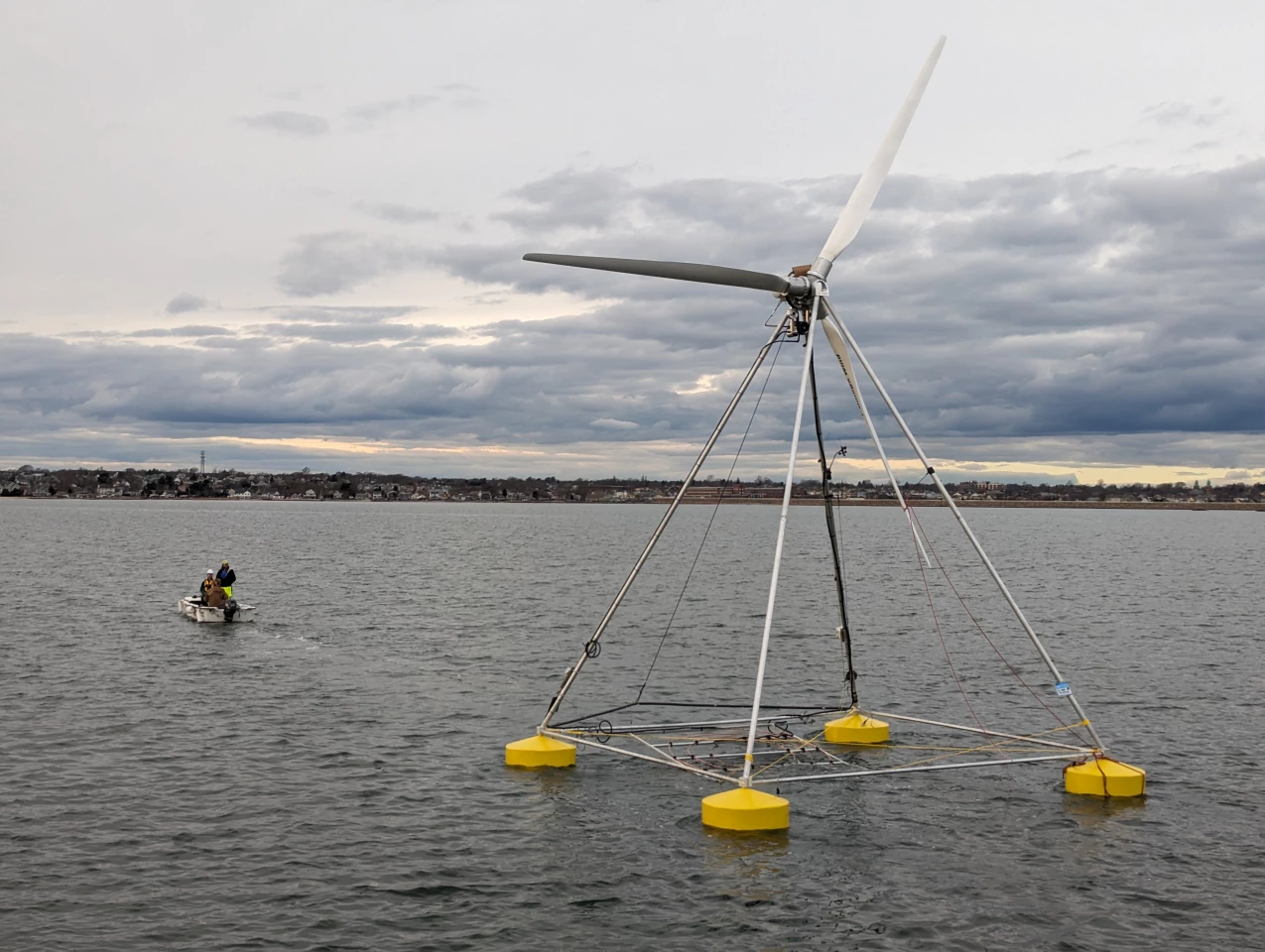
The prototype was launched successfully off New Bedford, Massachusetts, earlier this week, where it will remain for an unspecified duration for evaluation.
A full-size 10-megawatt turbine would place a 198 m (650 ft) rotor, complete with variable pitch blades, on a 119-m (390-ft)-high pyramid with 70-m (230-ft) sides. T-Omega estimates the total system weight would be between 1,200 to 1,800 metric tons.
“Our team is thrilled to take this next step in launching our groundbreaking technology,” said T-Omega Wind CEO, Brita Formato. “Floating offshore wind is a critical energy source for reaching multiple state and federal goals by 2030. The offshore wind industry is facing well documented challenges. T-Omega Wind’s radically redesigned floating offshore wind turbine will solve most of the challenges in an elegant and cost-effective manner. Our technology presents significant cost reductions in both production and installation/maintenance, entirely manufactured domestically. We are excited to showcase this technology to the world’s largest offshore wind developers, and we aim for full utility scale deployments in the coming years.”
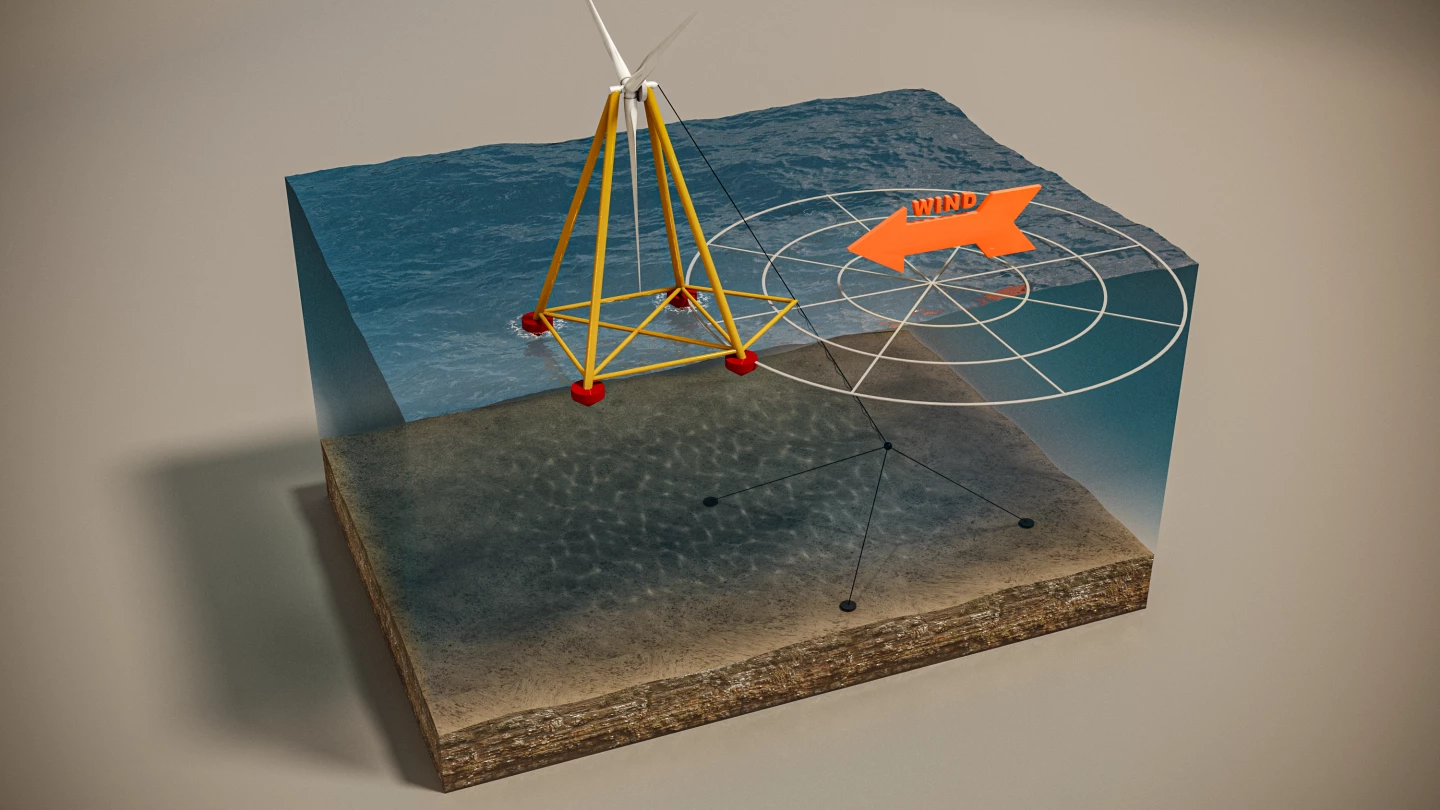
We look forward to seeing this company scale up and prove its technology in a commercial setting; the vast majority of the world's best wind resources are well offshore, in deep waters where ground-anchored towers are impractical to build. Cost-effective floating turbines like these could make a significant contribution.
Source: T-Omega