A new offshore wind farm system that promises faster, cheaper installation and operations will be tested in the Mediterranean. Called the NextFloat+ Project, it received a €13.4-million (US$14.4-million) grant from the European Commission.
Setting up wind farms at sea seems like a logical idea. Sea breezes tend to blow regularly and open water provides a more predictable and dependable wind pattern than on land. Plus you don't have to worry so much about compulsory purchase of the building site.
However, the engineering challenges of setting up turbines at sea are so great that they often outweigh the benefits. This is because not only do the turbines need to be very robust, with blades that won't bend under load and strike their own mast, they also require heavy mooring systems to keep them in place that are expensive to install.
NextFloat+ is a consortium led by Barcelona-based X1 Wind and includes Technip Energies and NextFloat Plus SAS. Its purpose is to build a prototype 6-MW wind station called X90. This is a triangular floating platform with a single turbine that is assembled onshore and then towed to the installation site.
The X90 uses Single Point Mooring (SPM) and a Tension Leg Platform (TLP) system that doesn't require special heavy equipment to install. In a TLP, the triangular structure floats on the surface and three cables connect to a mooring on the seabed at depths of over 1,600 ft (500 m). These are then tensioned to keep the platform precisely in place. For the X90, the TLP uses a SPM to the cable trio that allows the platform to passively turn into the wind. Before the platform is floated out, the SPM is installed with a quick-connect system that lets the platform be snapped into place on arrival.
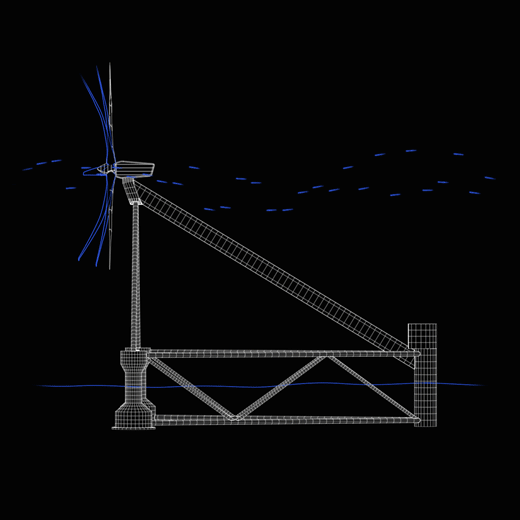
This setup is designed around what at first seems like a backward turbine. Conventionally, wind turbines face into the wind and the assembly turns on top of a mast as the wind shifts. This means that the mast must be able to withstand a lot of strain and the rotor blades must bend as little as possible or they could end up striking the mast, which would be most unfortunate.
With the X90, the rotor is fixed on the platform, which does all the turning. In addition, the turbine pivots like a weathervane and faces away from the wind, so the air pushes the blade from behind. Since there's no mast to strike, the blades can pretty much bend as they please. This not only makes for a simpler and lighter design, but one that is cheaper and easier to maintain.
In all, the platform, mooring arrangements, and turbine reduce the installation's seabed footprint. It also lends itself to scalability thanks to its modular design, with a new mass-produced commercial platform of over 20 MW already on the drawing board.
"We’re thrilled to receive support from the Innovation Fund," said X1 Wind CEO and co-founder Alex Raventos. "The grant represents a cornerstone in the fundraising for the NextFloat+ Project, adding to finance already secured through the European Commission under the Horizon Europe program, finance secured through the French Government as part of the France 2030 plan operated by ADEME, plus private funding from partners and shareholders. Crucially, it will provide an opportunity to drive substantial improvements in the competitiveness of floating wind as we prepare for long-term mass deployment in locations around the world."
The video below shows a prototype of X1 Wind's PivotBuoy system in storm conditions.
Source: X-Wind