Used in the right way, robots they have the potential to make life much easier for humans on a production line, but most factory robots don't have the ability to stop or subtly adjust their motion, so anyone who gets in the way is at risk of injury. Ford thinks it's found a way around this problem, and is putting humans side-by-side with robots in its Cologne factory to validate its approach.
To start with, Ford's new robots are being used to fit shock absorbers to Fiestas. Rather than forcing an assembly line worker to manipulate a heavy shock absorber above their head, workers can use the robots to lift and position the part, before finishing the operation with the push of a button.
"Working overhead with heavy air-powered tools is a tough job that requires strength, stamina, and accuracy. The robot is a real help," says Ngali Bongongo, production worker at Ford's Cologne plant.
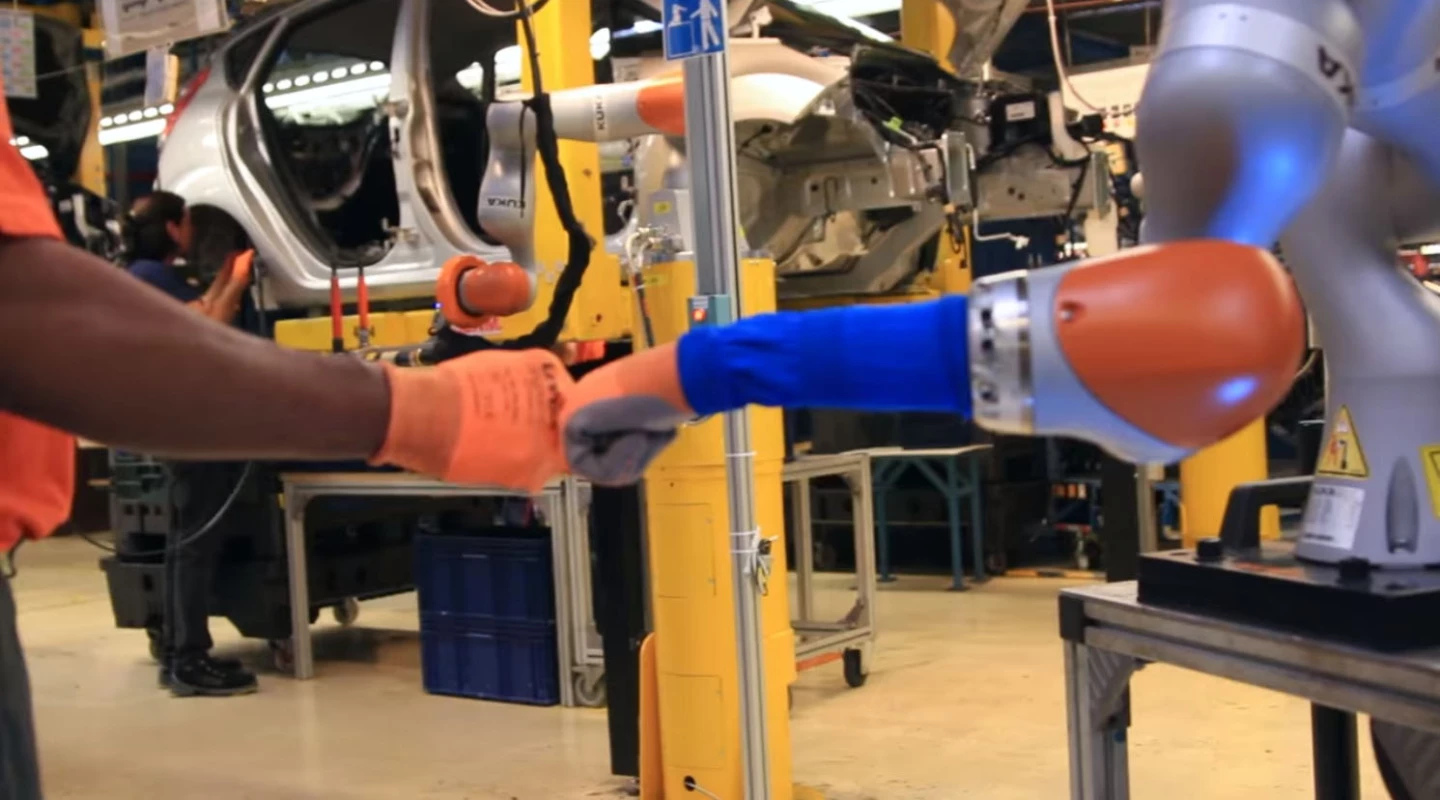
As you'd hope, the robots have been programmed to be conservative when it comes to human contact. If an arm or finger gets in the way, sensors will detect the obstruction and the machine stops moving to protect the worker.
Ford's sense-and-stop system is one of many systems being developed to make robot and human collaboration less dangerous. Researchers at the Max Planck Institute, for example, have been working on a soft-actuator allowing robots to "give" if they make contact with a worker, while MIT researchers have employed "cross-training" techniques that see robots and humans swap jobs so they can see things from the others' point of view and carry out tasks more efficiently when working together.
The next step for Ford involves exploring how far the technology can be pushed, looking for other tasks where collaborative robots can be employed on their assembly line.
Source: Ford