While clay is widely used to build basic structures such as huts, we typically don't see it being utilized in large-scale construction projects. That could soon change, however, thanks to a recently developed process known as impact printing.
By now you've probably heard about 3D-printed concrete houses, which are built up by extruding successive layers of concrete from what is essentially a giant 3D printer.
Among its other selling points, the technology typically allows homes to be built quicker, at less cost and with less waste than homes made by conventional methods. That said, construction does need to be periodically paused so that the deposited concrete can harden before more is added.
Additionally, production of the cement used in concrete is one of the world's largest sources of greenhouse gas emissions.
Which such drawbacks in mind, Dr. Lauren Vasey and colleagues at Switzerland's ETH Zurich university looked to clay. More specifically, they developed a proprietary material consisting of clay, silt and an undisclosed earth-based "common waste product" from industry partner Eberhard AG.
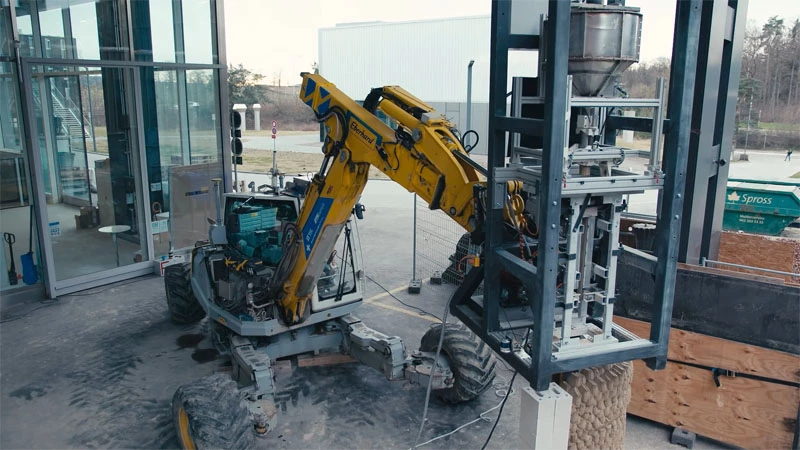
Utilizing a machine that could one day be transported to construction sites, blobs of the material are shot straight downward at speeds of up 10 meters (32.8 ft) per second. Those blobs bond with one another on impact, incrementally forming into solid walls, columns or other structures.
If the distinctive "bunch-of-blobs" appearance of those structures isn't desired, their exterior surfaces can be smoothed down with a rotary tool on a robotic arm. And importantly, the building material contains no cement, and it doesn't need to be left to harden until the entire structure has been printed.

Although the system has so far only been used to print fairly simple structures, the scientists are working on methods of robotically integrating supportive elements into the clay material as it's being deposited. They're also developing computational design software to guide construction of impact-printed structures.
These combined technologies could allow for considerably larger, more complex builds, possibly performed by a printing rig mounted on the university's HEAP autonomous excavator.
You can see the impact printing system in action, in the video below.
Source: ETH Zurich