3D printers may allow individuals or small companies to produce prototypes, but the machines aren't really suited to mass production. That's where the Mayku Multiplier is intended to come in – it's billed as being the world's first desktop pressure former.
Users start by loading a sheet of heat-moldable material into the Multiplier, after which they place the item to be copied on its forming platform, located beneath the material. Once activated, the machine then heats the material to soften it, while also subjecting it to four atmospheres of air pressure. This causes the material to be pressed onto the item, precisely conforming to its shape and size. It captures the object's surface topography down to a resolution of 3 microns.
When the now-molded material is subsequently removed from the Multiplier and allowed to cool, it can be used as a mold to manufacture batches of the original item – that mold could be filled with pourable substances like concrete, resin or even chocolate. That said, the molded material could also be a finished product, such as a product casing, packaging or a custom-shaped tray.
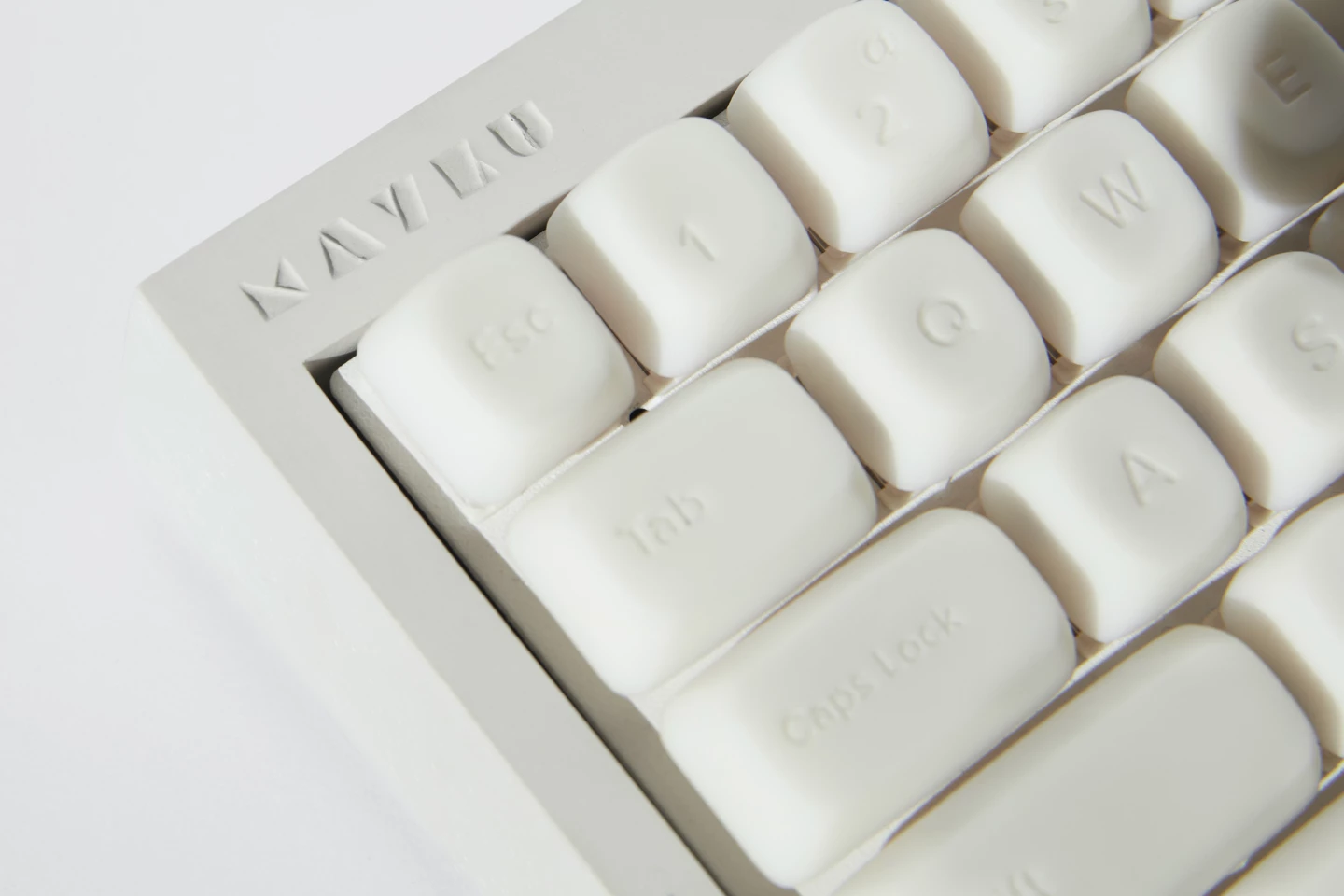
The whole process reportedly takes about four minutes, and only requires the machine to be plugged into a standard electrical outlet – the Multiplier utilizes its own 1,200-watt heaters, compressor and stainless steel air tanks.
Mayku plans on providing sheets of material such as PETG (polyethylene terephthalate glycol), HIPS (high impact polystyrene), LDPE (low-density polyethylene) and EVA (ethylene-vinyl acetate), although third-party sheets can also be used – as long as they're between 0.25 and 8 mm thick. The machine's forming platform can accommodate items measuring up to 160 mm (6.3 in) tall and 400 mm (15.7 in ) wide.
The Mayku Multiplier will be available for preorder via the company website starting in October, and will initially sell for an "early bird" price of US$1,999. You can see it in use, in the following video.
Source: Mayku