Cleaning power station boiler tube walls is a dirty and troublesome job that is not only hazardous, but can generally only be done during station down times to minimize the risk to human cleaners. To help address this problem, a new robot has been developed that is specifically designed to climb and clean boiler tube walls, even in confined spaces and at elevated particulate levels.
In steam-driven electric power stations, water circulates in tubes heated by fuel burned in a furnace, creating hot gas which heats water in the steam-generating tubes. Over time, these boiler tubes develop a thick residue on their outer surface from the burning of fossil fuels in the furnace, which significantly affects the efficiency of the boiler itself. Ordinarily, workers clean these tubes by climbing up scaffolding, much of which is very high and dangerous as boiler tubes can be anywhere up to 180 ft (60 m) tall.
To help remove this danger to life and limb, the boiler tube wall climbing (BTWC) robot created by International Climbing Machines (ICM), is specifically designed for the harsh conditions of working in power station boilers, and gets about by attaching itself with electromagnets to standard-size boiler tubes and inching its way up. With a mechanical cleaning head that can utilize a variety of removable brushes, the BTWC also has front and rear mounted cameras – one to provide navigation, and the other to enable remote visual inspection of the cleaned surface.
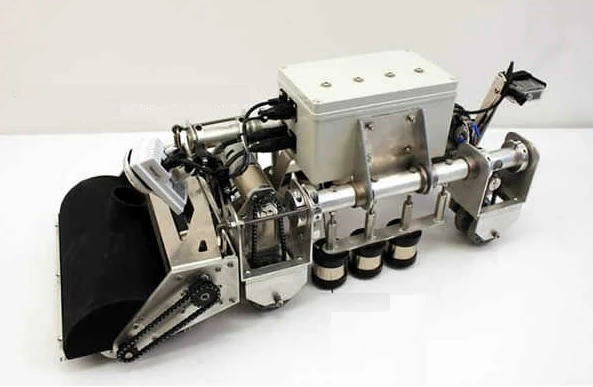
The cleaning head also incorporates a particulate capture shroud that catches dust and debris from the rotating brush, and feeds it through to a HEPA-filtered vacuum source. This helps reduce the airborne particles produced in cleaning operations, further protecting workers from hazardous materials.
Originally designed and built for the Italian energy company Ente nazionale per l'energia elettrica (ENEL), the BTWC takes cues from other robots in the ICM range, such as its submarine-cleaning automaton, that are also designed for hazardous and difficult areas, and with remote inspection capabilities via cable-connected, remotely-operated cameras.
Fitted with a range of detectors and other devices, the company also sees the robot being used in future in non-destructive testing on the metal in the boiler tube walls. Any cracks or defects identified could then be repaired using integrated welding operated remotely.
Source: ICM