Scientists regularly turn to nature for inspiration in their pursuit of next-generation materials, and a team of engineers studying the porous microstructures of bone and wood has come up with a clever example of biomimicry with wide-ranging potential. Laden with tiny holes, the lightweight new materials could find home in surgical implants and airplanes to offer a high-degree of stiffness in areas under stress.
The new material design was conceived by researchers at Princeton University and Georgia Tech, and feature what are known as spinodal microstructures. These webs of microscopic holes are modeled on the different types of pores found in natural materials like bone, animal horns and wood that take on different shapes such as columns, diamonds or spheres for optimal performance. The orientation, size and shape of pores within the structures can be fine-tuned to offer stiffness in particular directions, for example, or to control the material's density or weight.
"You have the actual structure and the microstructure working together to get superior performance," said Fernando Vasconcelos da Senhora, a graduate student at Georgia Tech and first author on the new study.
The researchers demonstrated the potential of these materials by designing and 3D printing a prototype facial implant out of a photopolymer resin. Featuring pores carefully shaped like columns and lentils, the implant was stiff enough to endure the forces of chewing, while the holes were also sized to promote bone growth and healing by facilitating the flow of body fluids.
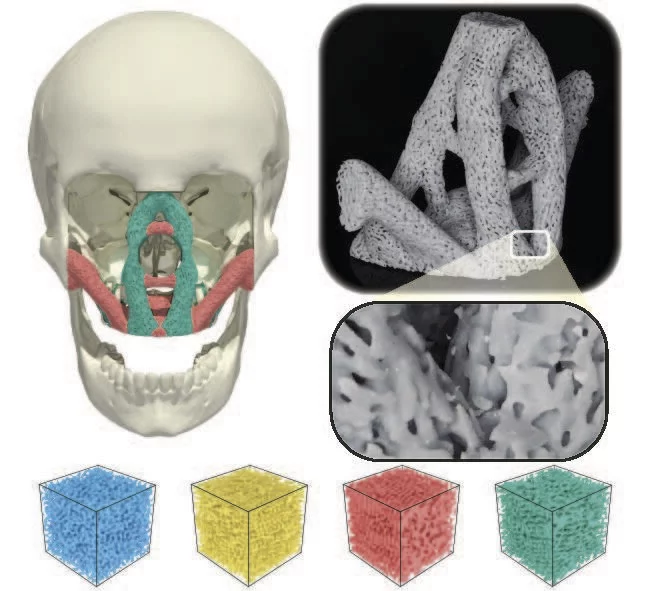
Because the geometry can be so finely tuned, these implants could be made out of many different materials, according to the scientists. In another example, they used the spinodal microstructures as the basis for a strong and lightweight version of a jet engine bracket, which holds the engine in place on an aircraft. For implants in the human body, however, biologically safe materials would be the obvious choice.
"It's not the base material that is better. It is the microscale features that are better," said Emily Sanders, a co-author and an assistant professor of mechanical engineering at Georgia Tech. "In theory, we could make the scaffolds out of any material – most appropriate would be to explore biocompatible materials."
The researchers say that the potential of these creations, which they call architected materials, lies in the way they seamlessly transition between different types of microstructures in the one object. This makes them less likely to have weak spots, while allowing for the stiffness and other properties to be finely tuned.
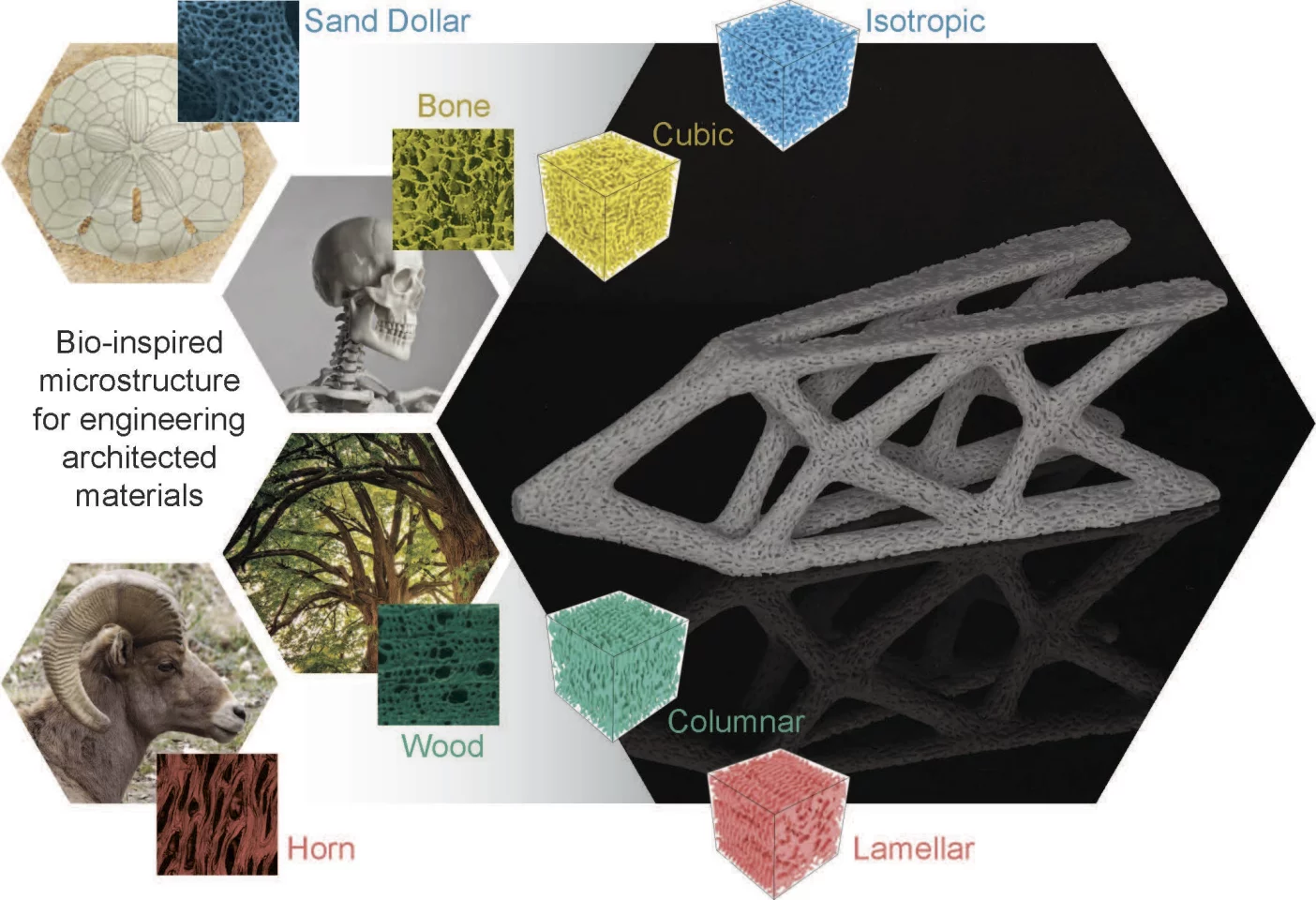
"We have a technique that is quite powerful in the sense that it combines material architectures with optimization at different scales and its integration with additive manufacturing," said Glaucio Paulino, principal investigator on the project. "It can have a broad range of applications in the sense that it scales, so it can be applied in nano- and microtechnology, as well as at meso- and macroscales."
The research was published in the journal Advanced Materials.
Source: Princeton University via TechXplore