A new material tackles the carbon problem of concrete production and usage by employing a pretty unusual workforce: cyanobacteria. The bio-cement these micro-organisms help to produce harnesses a process that's existed in nature for 3.5 billion years.
By now, concrete's carbon problem has been very well publicized. According to Scientific American, producing one kilogram of concrete releases one kilogram of carbon dioxide into the air. This comes not only from the chemical reactions used to create it, but also the fossil fuels burned to get giant kilns to the 1,450 °C (2,640 °F) temperature needed to bake limestone, a precursor to making the cement that forms the basis of concrete. Concrete production is now responsible for roughly 8% of the world's total carbon emissions.
That being said, because it's such an effective building material, it's hard to get away from. In fact, according to a report from Arizona State University, concrete is the second most used material in the world, beaten out only by water.
As a result, we've seen some ingenious ways to create it – or substances that mimic it – in much greener ways. Last year alone we reported on a method that replaces limestone kilns with a zero-carbon electrolysis method; the use of baking soda to reduce carbon emissions; and the addition of biochar to cement to create concrete that absorbs 23% of its own weight in carbon dioxide from the surrounding environment.
Three-billion-year-old lab
Now, researchers in Germany have created a concrete alternative that is not only carbon neutral, but carbon negative. To form it, they looked at the way in which structures known as stromatolites have been made in limestone for over three billion years and then they recreated the process in the lab.
To start, they created bacterial cultures from cyanobacteria – commonly known as blue-green algae – by providing them with the ideal light source and nutrients to optimize their growth and ability to photosynthesize. Then, to get the bacteria to undergo mineralization and create stromatolite-like structures, they added calcium chloride and other calcium sources. To this mix they then added hydrogels and other fillers such as sand, in much the same way that aggregates are added to cement to create concrete. Finally, carbon dioxide was pumped into the slurry to support the growth process, which is all driven by light.
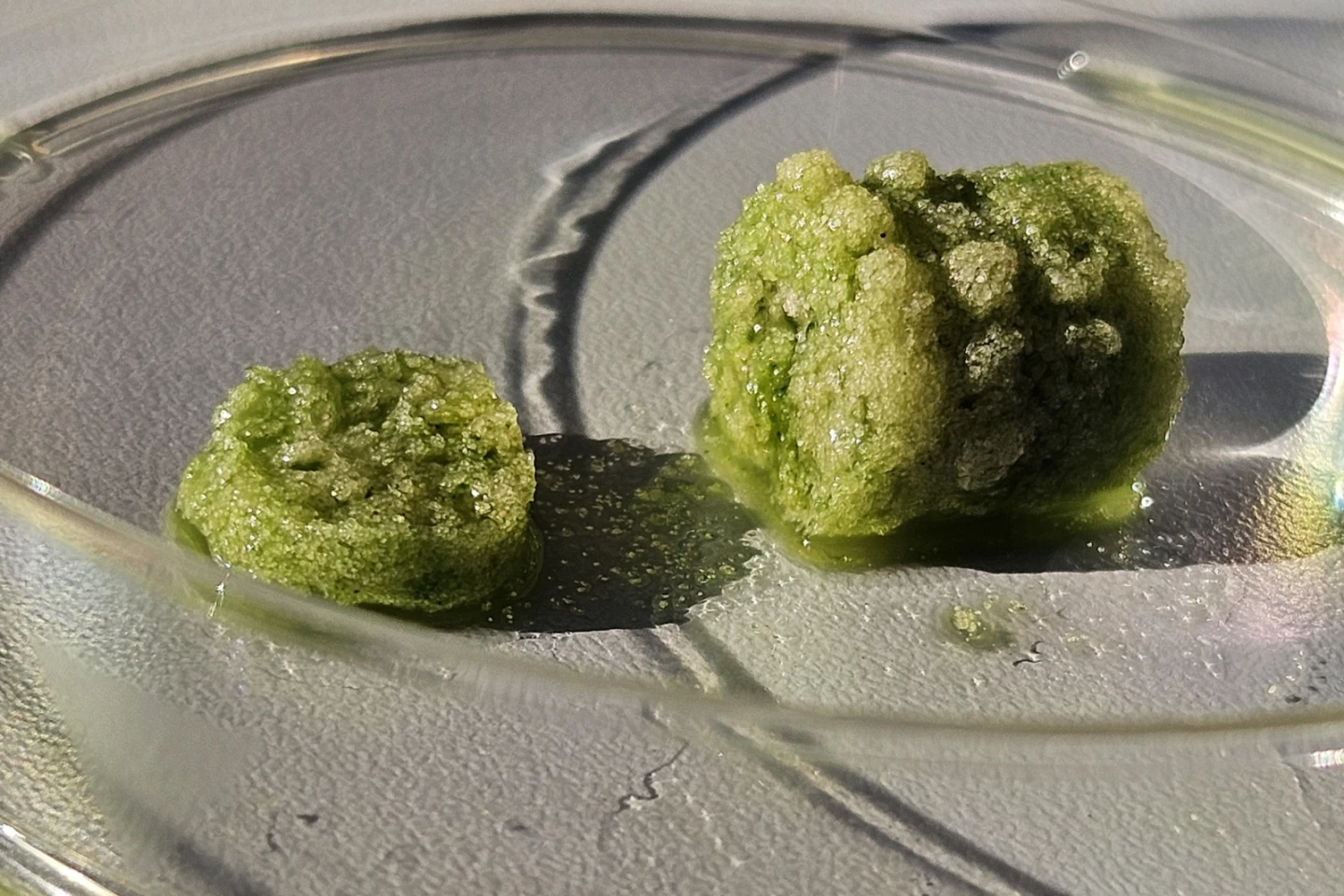
“The developing solid structure is still porous during the process, so light enters the inside and drives the carbon dioxide fixation through limestone mineralization," said project manager Matthias Ahlhelm from the Fraunhofer Institute for Ceramic Technologies and Systems IKTS. "We can stop the process by removing the light and moisture or changing the temperature.” Once that is done, the remaining bacteria die and the resultant material is completely free of toxic substances. It also sequesters a damaging greenhouse gas into its very structure.
The material can be poured into molds or lattice structures to create bricks or a nearly unlimited number of other shapes, it can be extruded or used in additive manufacturing like 3D-printed construction, or it can be applied by spraying.
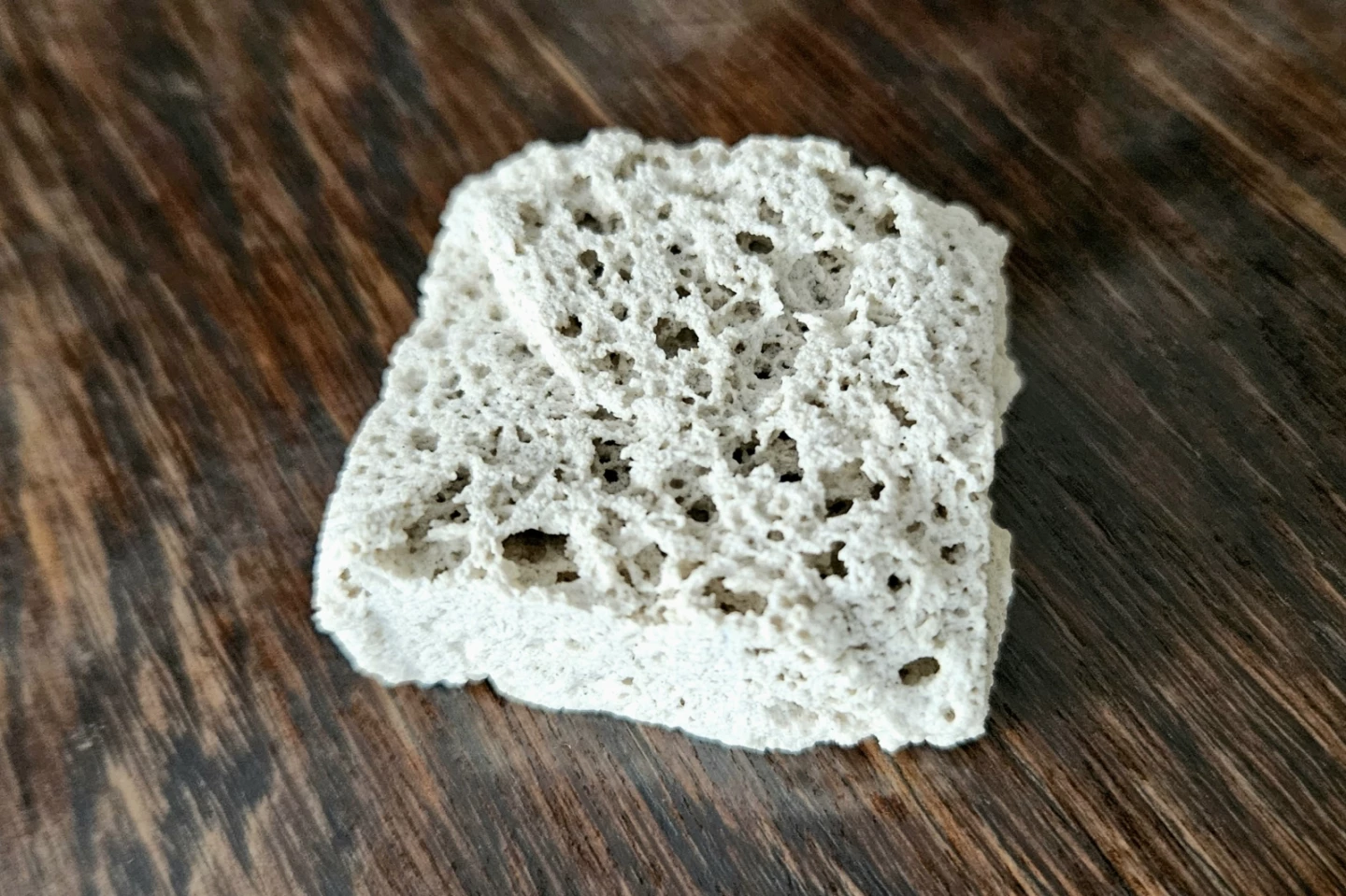
Now the team is looking at scaling up production of the material and making it even greener. For example, the researchers say they could source their carbon dioxide from industrial pollutants and get their calcium from the waste produced by basalt and other mines.
Source: The Fraunhofer-Gesellschaft