With incredible lightness, stiffness and strength, carbon fiber has a lot going for it, but even the dreamiest of materials have their shortcomings. One scientists have been working to address is carbon fiber's tendency to burn at high temperatures, and an international team of researchers has now found a low-cost and scalable solution to this problem, in the form of a protective coating that self-forms within molten salt.
By some measures, carbon fiber is already highly resistant to heat, with an ability to remain stable in the air at up to 800 °C (1,472 °F). This make it highly suitable to all sorts of applications, from bicycle frames, to cars, to medical equipment and even guitars. Where it can run into trouble, however, is when it is subjected to extreme temperatures, such as those experienced in the aerospace industry. Under such conditions, it reacts with oxygen and burns, causing its structure and in turn its desirable qualities to quickly degrade.
“One weakness of carbon fibers is that they are burned easily if you have high enough temperatures and oxygen present,” says Yongfeng Lu, who led the team made up of researchers from the University of Nebraska–Lincoln and France's Institute of Condensed Matter Chemistry of Bordeaux. “If we could make them non-flammable, so that they don’t burn when exposed to fire, that would be exciting.”
Scientists have made inroads in developing more fire-resistant forms of carbon fiber before, but these have involved the use of expensive equipment, complicated multi-step processes and unpredictable chemical reactions. We also looked at promising research last year that used a plant-derived substance to keep the material from burning while also making it easier to recycle. The authors of this new study have come up with a solution they say is simple and cheap, which begins with melted salt.
This process takes place at 1,800 °F (982 °C) and once the salt crystals are reduced to liquid, titanium and chromium powders are added to the mix, before carbon fibers are introduced as the finishing touch. This causes a chemical reaction that results in a protective coating with three distinct layers, owing to the different behaviors and reactions of the materials in the molten salt mixture.
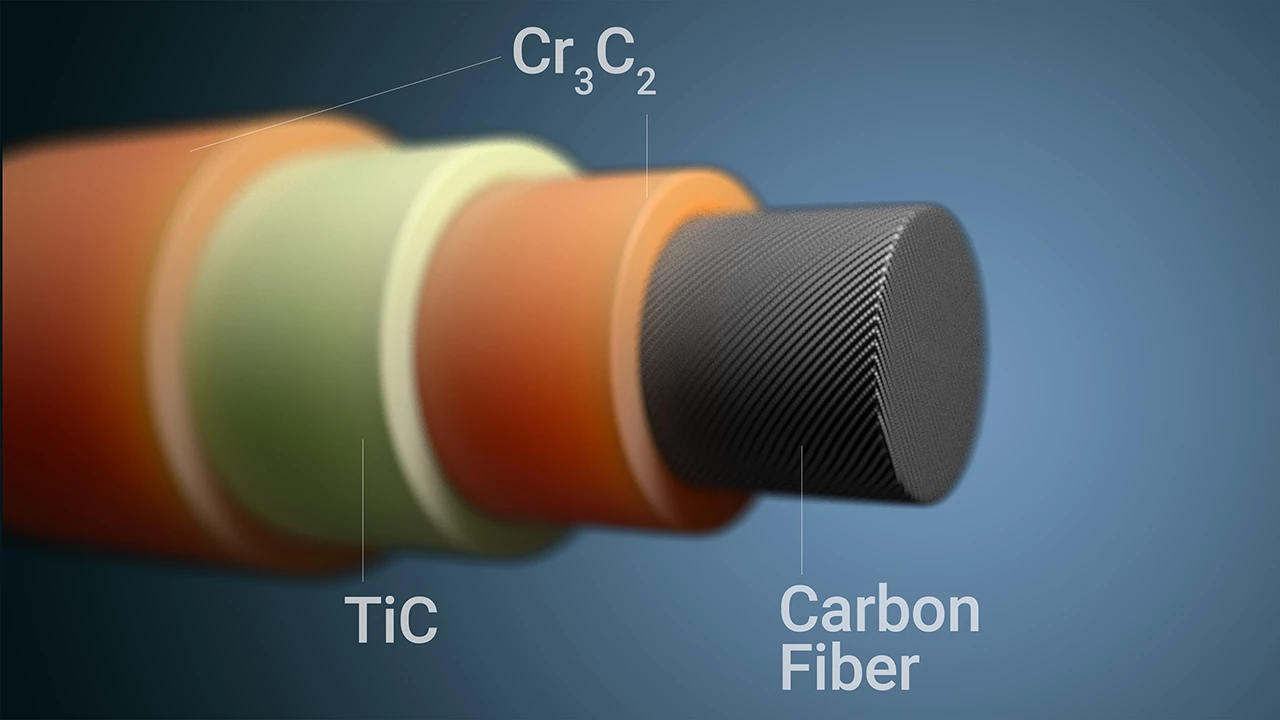
“We’ve found a recipe that can form three layers in a single state,” Lu says. “With one single dip, we can get three layers of coating.”
Its performance was assessed through experiments where the coated carbon fibers were subjected to extreme conditions involving temperatures of around 2,200 °F (1,200 °C) and an oxyacetylene torch, with the carbon fibers successfully maintaining their structure throughout. The triple-coating, which is made up of chromium carbide and titanium carbide, was found to offer more protection than a single layer.
“We are trying to add surface layers that can separate carbon fibers from oxygen so that even under high temperatures, they won’t be burned,” Lu says. “Carbon fibers can be used in many ways – woven into textiles and in parts of buildings, airplanes, electronics equipment – but if they’re flammable, that poses a new risk to the system and limits those applications a lot.”
The scientists describe their new process as fast and clean, and therefore highly suitable to industrial use. As they work towards that goal, they intend to work out exactly how fireproof these coated carbon fibers are compared to conventional ones, and for how long they maintain their structure and properties under extreme conditions.
The research was published in the journal Proceedings of the National Academy of Sciences.
Source: University of Nebraska–Lincoln