While bio-based polylactic acid (PLA) thermoplastic is relatively eco-friendly and easily recyclable, composites such as carbon fiber are much stronger. German scientists are now claiming to have combined the best features of both, with a new all-PLA composite.
Unlike traditional petroleum-based plastics, PLA is made from renewable sources such as corn starch, tapioca and sugarcane. Not only is it fully recyclable (where facilities exist), but it also biodegrades within a few years under the right conditions, and is industrially compostable.
Like other plastics that are used on their own, it doesn't have the mechanical strength or rigidity exhibited by composite materials. Because those composites are made of at least two intermixed substances, though, recycling them is a complex process – often deemed to not be worth the effort or expense.
With that in mind, researchers from the Fraunhofer Institute for Chemical Technology have helped to create a composite made of woven PLA fibers that are set within a PLA matrix.
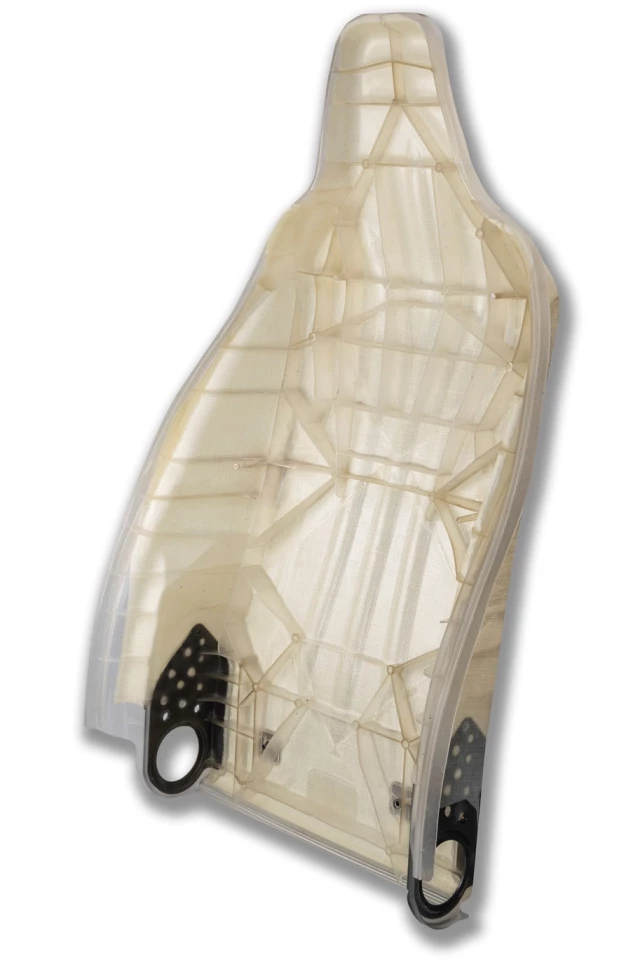
The fibers and the matrix are actually made of two different types of the bioplastic, the former having a higher melting point than the latter. This means that in the production process, the solid fibers are embedded within the liquid matrix (composed of melted PLA granules), after which the matrix sets to also become a solid. The recycling process consists of simply melting down the fibers and the matrix, at different temperatures.
Fraunhofer claims that the PLA composite is much stronger and more rigid than the "pure" form of the plastic, reportedly able to "compete with commercially-available self-reinforced polypropylene composites." What's more, the manufacturing process is said to require about half as much energy as that of petroleum-based composites, and to produce about half the amount of carbon dioxide per kilogram of material.
Once the technology is developed further, it is hoped that the PLA composite could find use in sporting, automotive and medical applications. The material was developed as part of the European Union Bio4self project, which also includes the Technical University of Denmark, Belgian textile research group CENTEXBEL, and Danish firm Comfil.
Source: Fraunhofer