Soft materials and stiff materials both have their uses, but the two properties typically aren't seen in one substance. RoboFabric is an exception, then, in that it can be switched back and forth between soft and stiff states.
Designed by a team of scientists at Singapore's Nanyang Technological University, the material was inspired by the interlocking protective scales of animals such as armadillos and pangolins.
While the scales of both creatures are made of keratin, however, RoboFabric is composed of a network of 3D-printed interlocking polymer tiles. All of the tiles are linked together by thin metal wires running through and between them.
As long as those wires are kept relatively loose, all of the tiles are able to move around freely relative to one another. When the wires are tightened, however, the tiles get pulled together, instantly causing the "fabric" to become over 350 times stiffer. By releasing the wires' tension, the material softens again.
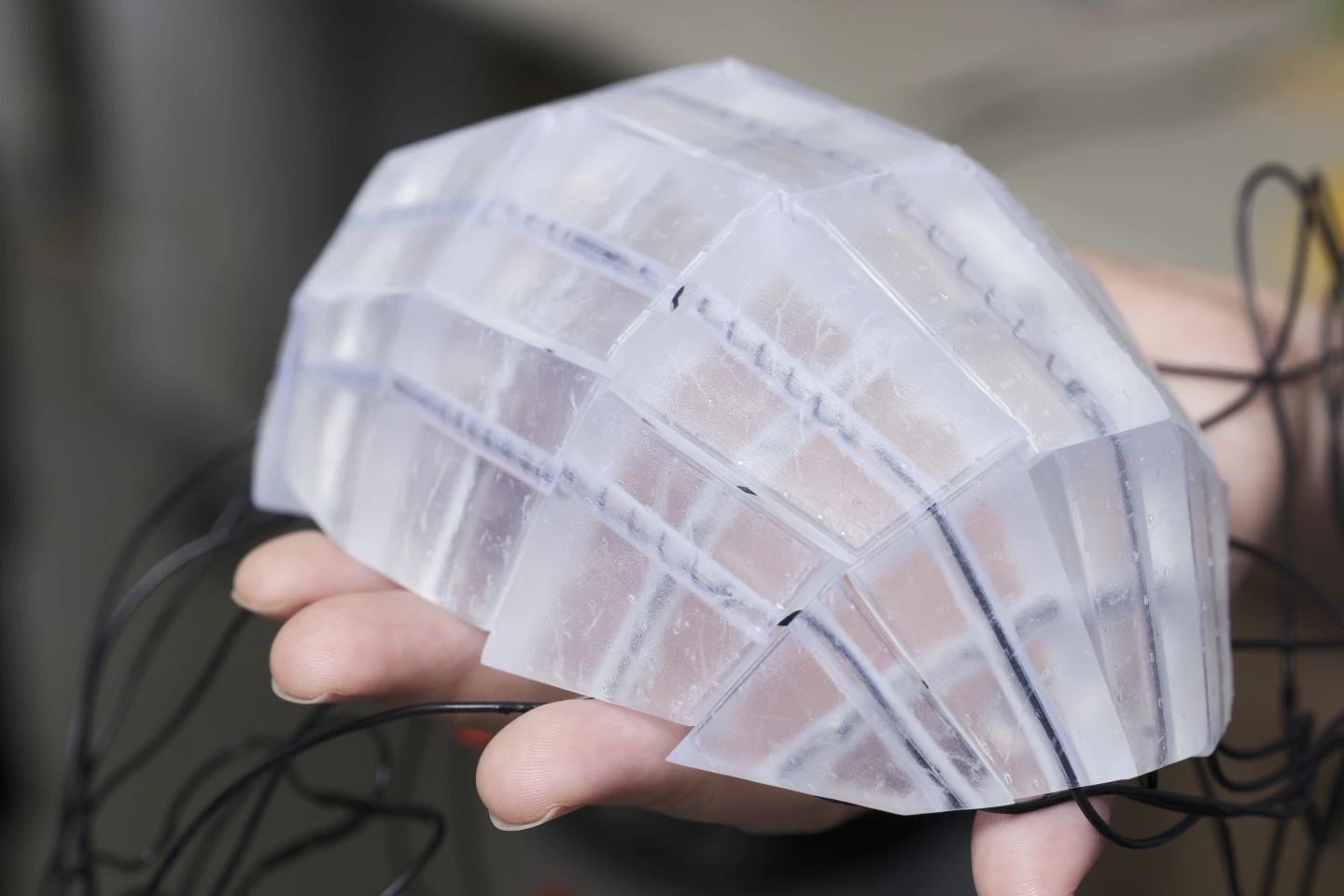
Among other possible applications, the technology could conceivably be utilized in arm casts that remain soft as the injured limb is initially being positioned, then stiffened once it's in the desired orientation. And instead of having to be cut off like a traditional plaster cast, a RoboFabric cast could simply be softened and slid off once no longer needed.
Along those same lines, the tech might also find use in assistive joint braces that would allow wearers to lift objects or perform other demanding physical tasks with less effort. Users could keep a wrist or elbow brace soft for maximum freedom of movement most of the time, for example, then stiffen it for support when lifting heavy objects.
The scientists were able to create such custom-fit braces via 3D scans of volunteers' limbs, then 3D-print the dozens of required tiles in less than one hour. Stringing the wires through those tiles by hand did take some time, but that process could likely be automated as the technology is developed further.
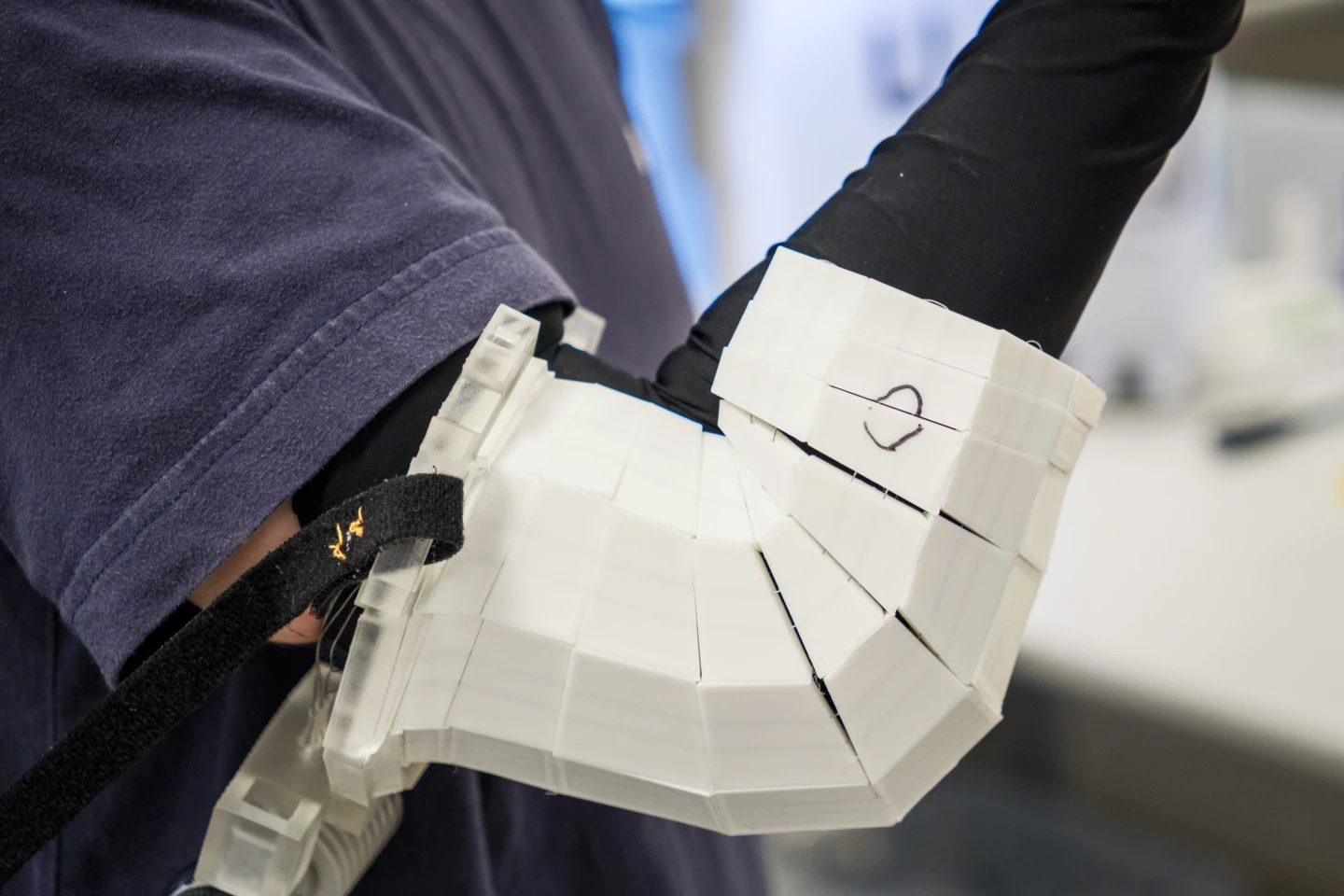
In lab tests, it was found that the volunteers' muscle activity was reduced by up to 40% when the braces were used for lifting tasks. And the possible applications for RoboFabric don't stop with wearables, either.
The technology has already been utilized in a robotic gripper mounted on the underside of a drone. That gripper is able to pick items up by stiffening and curling in around them, then release them by softening.
RoboFabric has also been used in a swimming robot composed of a slab of the tiles sealed inside an elastic envelope. When the air is sucked out of that envelope, the resulting vacuum causes the slab to stiffen, and take on a designated shape. When that vacuum is released, the slab softens, reverting back to its "relaxed" shape. By alternating back and forth between these two states, the device is able to swim through the water.
A paper on the research, which was led by Asst. Prof. Wang Yifan, was recently published in the journal Science Robotics. You can see the material in use, in the video below.
Source: Nanyang Technological University