At the Yuma Proving Ground in Arizona, the US Army is testing a new reusable parachute cargo-drop system that is 25% faster to rig and 40% faster to remove after landing to allow soldiers, to quickly leave the drop zone and get out of danger.
Developed during the Second World War, air drops have evolved into a standard procedure for resupplying troops or delivering humanitarian relief to inaccessible areas. But even with parachutes, shoving large pallets of equipment or combat vehicles out the back of an aircraft can result in a nasty jolt on landing.
To reduce this, drop parachute systems use several inches of honeycomb-like cardboard on the floor of the steel pallet. On impact, the honeycomb collapses, absorbing the energy instead of passing it along to the cargo.
It works, but the cardboard honeycomb takes time to rig along with the chutes and the restraints, and it's basically a one-and-done system. After the drop, the cardboard has to be stripped off the pallet and discarded using axes, shovels, and pickaxes before cargo like a Jeep can be cleared to move. This is not only laborious, but takes up precious time that soldiers would rather use getting under cover before hostile forces show up.
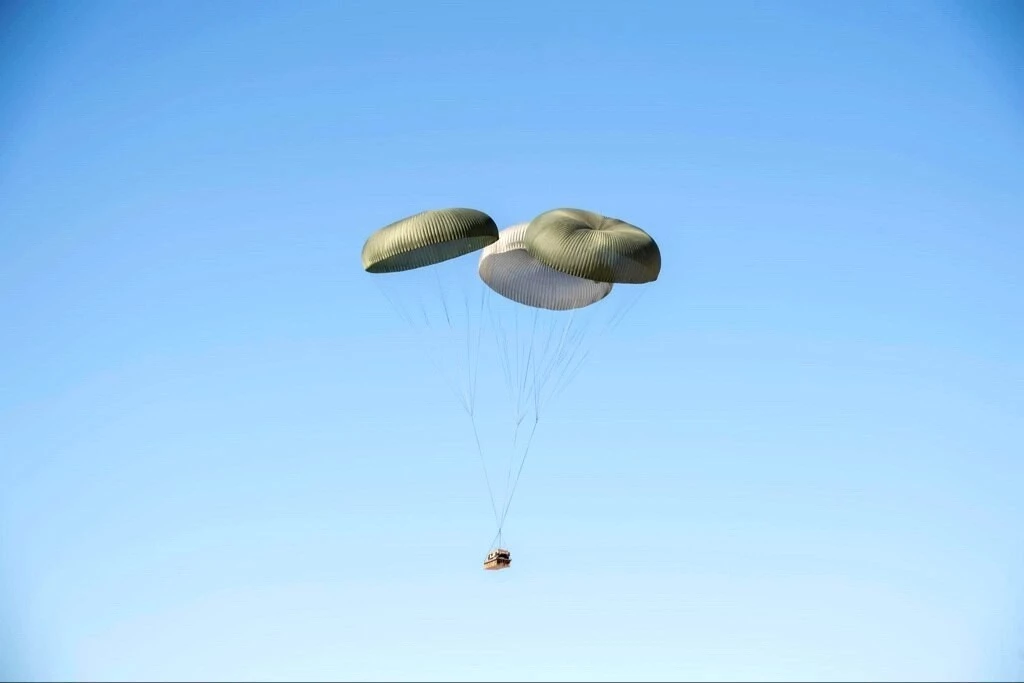
To alleviate this, the Army is testing several options, including the Rapid Rigging De-Rigging Airdrop System (RRDAS). This replaces a large fraction of the cardboard with a set of fabric airbags folded up under the pallet. These unfold and inflate under ambient pressure after the cargo drops, and absorb the impact by collapsing. According to the Army, the bags are reusable, can inflate at an altitude of only 750 ft (230 m) and can handle loads of up to 22,000 lb (10,000 kg).
In tests, the honeycomb reduced rigging time by 25% and de-rigging by 40%. In addition, RRDAS includes outriggers to keep the cargo upright when it hits the ground if it's a bit top heavy.
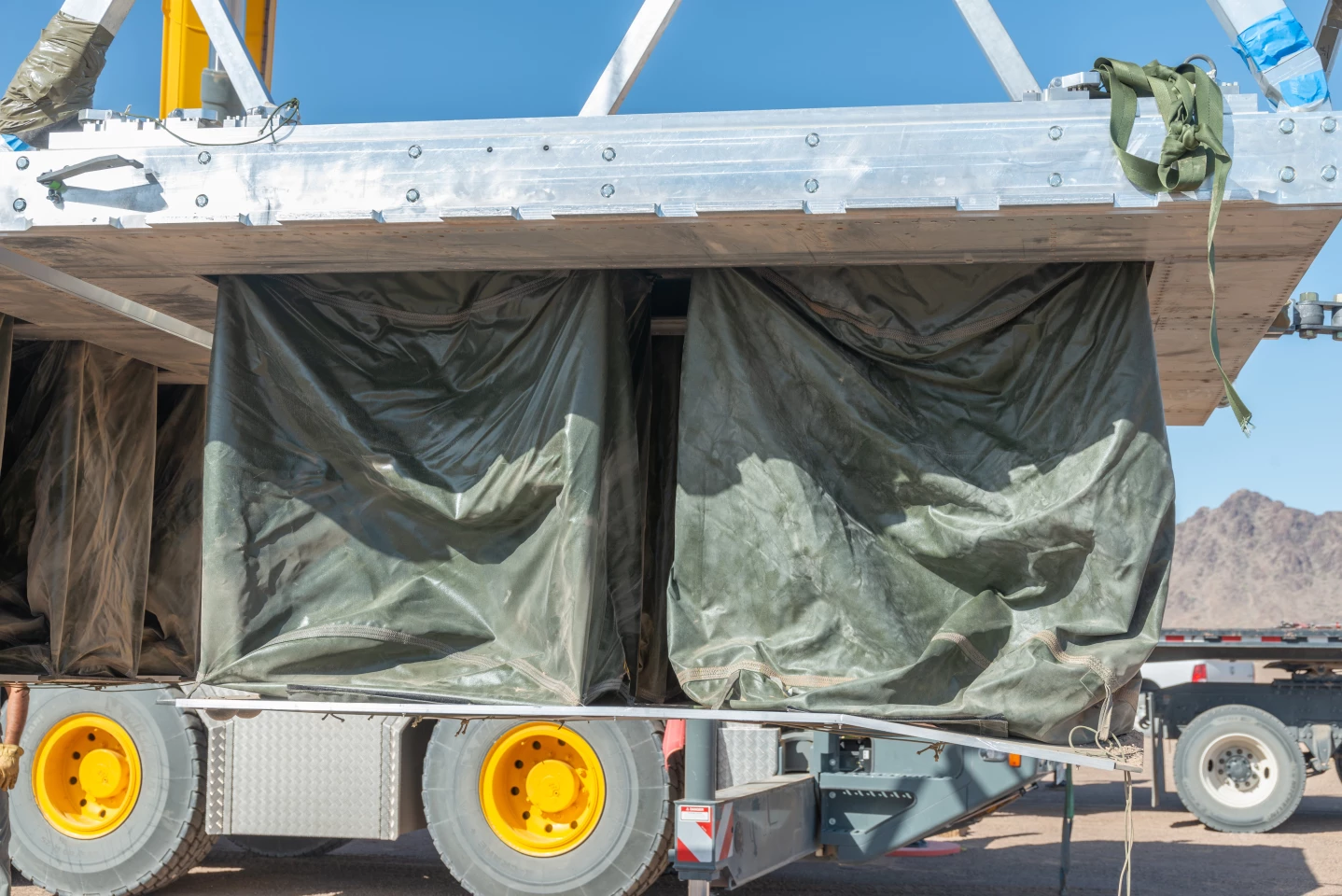
Testing is scheduled to continue this year with full field testing under realistic scenarios to follow in the US fiscal year 2025 to tweak the design.
"We will be able to increase the load of the payload and the length of the platform so we can drop heavier and longer items," said Maj. Matthew Rohe, Assistant Product Manager for Cargo Aerial Delivery at the U.S. Army Program Executive Office Combat Support and Combat Service Support. "We’ll be testing on and off at Yuma for several years to come."
Source: US Army