Diesel engines are some of the simplest combustion concepts in use today, with a design that has not changed much in half a century. But what has changed is the complexity of the systems that surround the diesel engine block to overcome inherent inefficiencies in emissions. A research team at the New ACE Institute in Japan has developed a new diesel combustion engine concept using multiple fuel injectors that doesn't require waste heat reduction. With a brake thermal efficiency of greater than 50 percent, the new engine could reduce engine manufacture costs.
Waste heat recovery (WHR) is commonly used as a method of capturing the engine's heat to maintain a temperature in a particulate filter and other emissions control systems. WHR is relatively expensive, but aids the vehicle's overall efficiencies in both fuel use and emissions reductions. The automotive research team at New ACE sought a way to optimize combustion that overcomes the complex tradeoffs between emissions, brake thermal efficiency (BTE) and energy losses on conventional diesel combustion.
The team's engine utilizes three fuel injectors in a variant of the Sabathe cycle. This limited pressure, dual cycle controls heat by holding constant volume and pressure in the cylinder. The modification with this new concept is to control fuel injection to temporarily create an isolation between the premixed combustion area and diffusion combustion area of the cylinder, which enables consecutive heat release.
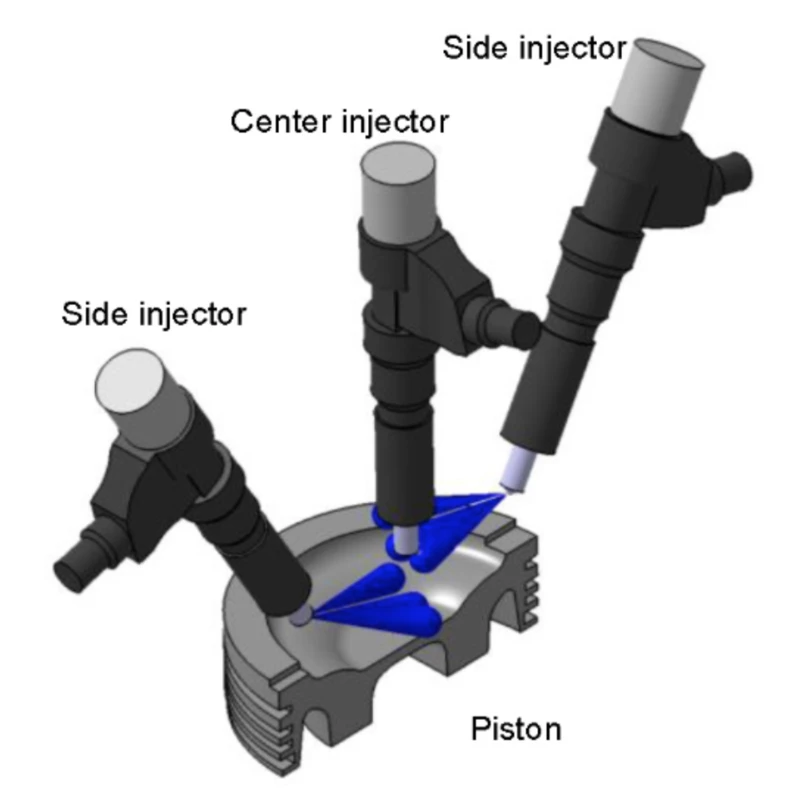
This is accomplished by fitting the cylinder with three injectors. One is vertically mounted at the center and two more are positioned at an angle on either flank at the piston cavity's circumference. The side-angled sprays are directed along the swirl direction of the airflow, improving mixing and preventing spray interference and impingement on the cavity wall. This improves air mixing at the center of the cavity, which creates a more dense combustion point. Shaping of the piston cavity (crown) helps prevent injection interference between injectors.
By controlling injection timing and duration under constant fuel pressure, heat can be controlled at a variety of compression ratios and operating temperatures. The center injector fires first followed by precision timing of the side injectors.
Experimental results for the engine concept showed that friction and heat losses were reduced. This produced lower smoke and NOx emissions when compared to conventional diesel combustion.
The New ACE Institute plans to further develop this engine concept.
Source: SAE International