Sail technology has come a long way since the days tall ships were carried along by billowing clouds of canvas. In fact, new aerodynamic discoveries coupled with exotic materials have turned modern sails into veritable works of high tech art. Today, sailmakers know that the less a sail distorts (through stretching, shear, compression or shrinkage), the more force or drive remains available to power the boat - especially helpful when you're in a close race for that final buoy. Now, the innovative designers at North Sails have woven an interesting array of tricks into their unique new 3Di line of "canvas" - laminated, heat-molded sails that hold their shape so well, they come close to performing like rigid airfoils.
If you've ever tooled around in a wind-powered boat, you know that sailing is about change: constantly shifting wind speed and direction, variable currents and waves ranging from ripples to breakers - all conditions that can affect sail shape and negatively impact its performance. Key to the North sails' ability to resist both stretch and compression is their construction from various lengths and multiple layers of "spread filament tape" (SFT) oriented along several axes. SFT starts out as a single length of thread that has had its component fibers spread out and laid parallel to one another, then sprayed with thermoset adhesive for an overall thickness of about 35 microns.
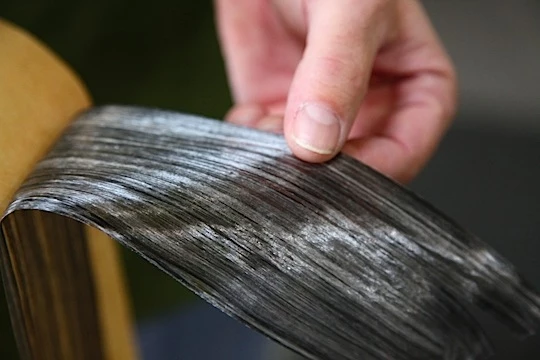
Depending on the particular sail design, the SFT can be made of various combinations of Aramid (aromatic polyamide), carbon fiber or Dyneema (ultra-high-molecular-weight polyethylene or UHMWPE). Aramid is strong and resistant to both tension and compression, but is easily damaged by UV rays (none is exposed in completed sails). Carbon fibers are also resistant to tension and compression, but are stiff and fragile. Dyneema is resistant to tension but not compression, yet it's durable and resilient. North makes 20 different Aramid/Carbon/Dyneema SFT blends at its Nevada facility, each with a different set of properties, which provides great flexibility in customizing the final product. Special software guides the precise placement of each SFT strip, adding an extra dimension of quality control to the whole process.
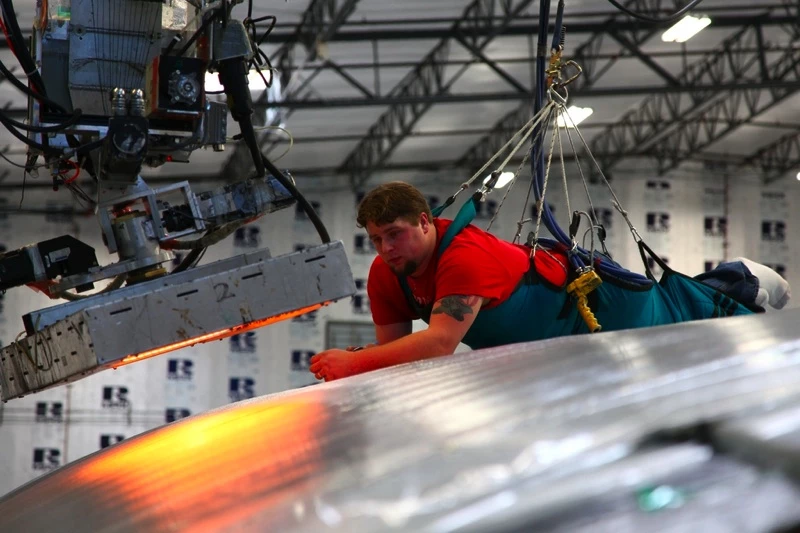
Once the SFT strips are assembled, they are sandwiched between layers of non-woven polyester, then placed on heated 3D molds for consolidation (the bonding of materials with like properties). The end result is an almost isotropic sail (resistant to omnidirectional forces) that holds its shape well over a broad range of wind speeds, stretches less and maintains its designed structure for a longer period of time. Ultimately, it may seem like a lot of trouble to go through for a sail, but history shows the pursuit of optimal performance seldom occurs on the path of least resistance.
Source: North Sails
Check out the video below to see some of the sails in action: