When most of us think of freshly poured concrete, we picture a material that should be left to dry as smooth as possible. A new wheeled robot drives right over the stuff, however, gouging its surface to make structures stronger yet also cheaper to build.
If wet concrete is poured in a single layer that is too deep, cracks will form in it as it dries and contracts. For that reason, the material is typically poured in successive stacked layers, each one of which isn't deposited until the one beneath it has cured.
One potential problem with this approach lies in the fact that if the layers are simply poured one on top of the other, the finished structure will lack shear strength at the interfaces between those layers. In other words, it won't take much force to make one layer slide horizontally relative to the one beneath it.
For this reason, the concrete is poured around an array of vertically-oriented lengths of steel rebar. Those reinforcing rods end up running through all of the layers, from top to bottom, boosting the structure's shear strength.
That said, rebar does cost money and add weight. Workers will therefore often manually add grooves to the surface of each layer while it's still wet, providing more surface area for bonding with the next layer. This increases the shear strength at the interface, meaning that less rebar is needed.
Of course, some of the costs that are saved by using less rebar are offset by the added worker-hours required for adding the grooves. That's where the Conit Runner robot comes in.
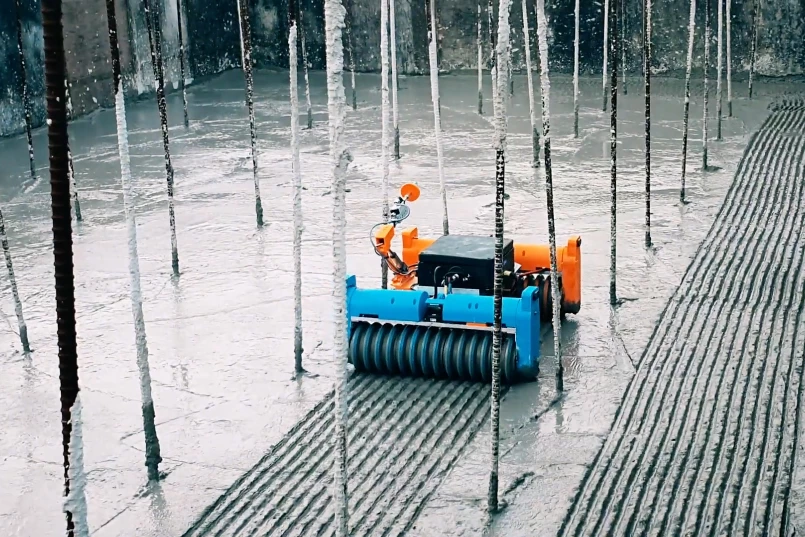
Developed via a partnership between Korean robotics company Itone and construction firm Posco E&C, the device autonomously makes its way across wet concrete surfaces at a speed of up to 10 mph (16 km/h), adding rows of grooves via its two 15-inch (381-mm) wheels as it does so.
The robot navigates those surfaces and avoids obstacles – such as the rows of rebar – utilizing LiDAR, ultrasound sensors, cameras and an IMU (inertial measurement unit). It's also able to measure the hardness of the concrete, ensuring that the material is firm enough to support the bot's 10-kg (22-lb) weight, yet soft enough for creating grooves that are at least 0.24 inches (6 mm) deep.
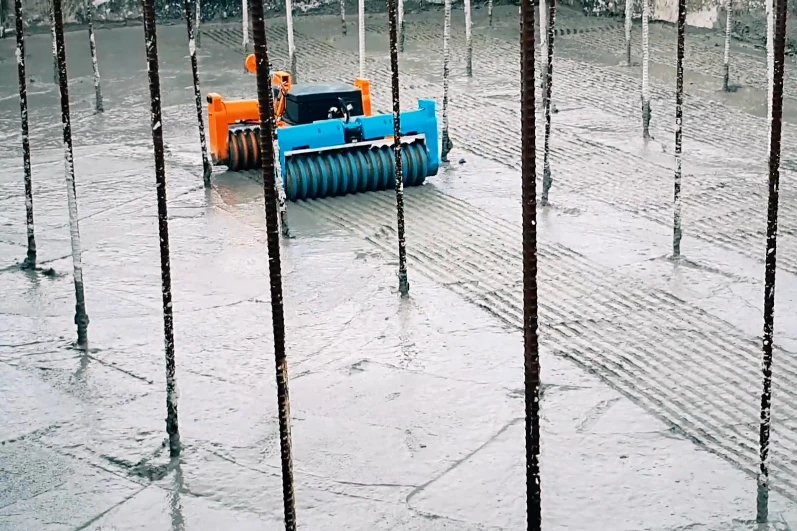
According to Itone, use of the Conit Runner reduces the need for rebar reinforcement by up to 30% and accelerates construction time by as much as 85%, reportedly matching the productivity of eight human workers.
There's currently no word on when the robot may enter wide use. For now, you can see it in action in the video below.
Source: Itone