We've been hearing a lot about "artificial muscles," which allow robotic devices or prosthetic limbs to perform human-like motions. And while most of them have been produced in labs utilizing high-tech materials, a new type could be made by hobbyists using a 3D printer.
Known as GRACE (GeometRy-based Actuators able to Contract and Elongate) the pneumatic actuating system was designed by scientists at the Istituto Italiano di Tecnologia (IIT, Italian Institute of Technology) and the Scuola Superiore Sant’Anna (SSSA, Sant’Anna School of Advanced Studies).
Each actuator takes the form of a flexible hollow plastic bulb with pleats running along its sides. When air is pumped into the actuator via a connected hose, it contracts longitudinally while expanding radially – in other words, it gets shorter and fatter. When air is withdrawn, on the other hand, the actuator gets longer and skinnier.
Therefore, if incorporated into a robotic finger (as an example), an actuator could pull the finger closed when air was pumped in, and extend it straight when air was withdrawn.
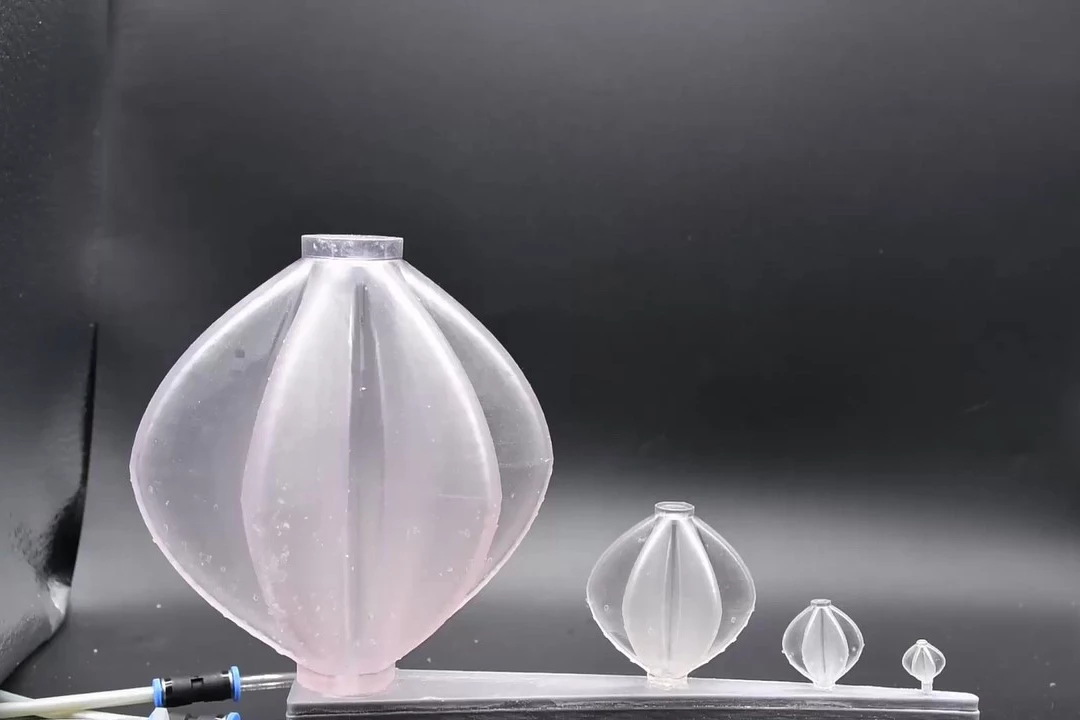
Depending on the intended application, the actuators can be made in various shapes and sizes, in various shell thicknesses, out of various types of plastic. Among other things, these variables help determine how much an individual actuator expands and contracts, the direction in which it moves while doing so, and how much air pressure is required to activate it.
In a demonstration of the technology, a team led by SSSA PhD student Corrado De Pascali created a life-size robotic hand incorporating 18 of the GRACE actuators. It is made entirely of soft resin, and was manufactured in a single 3D print process.
By pumping or withdrawing "a few tenths of a bar" of air, it's possible to make the hand bend or straighten its fingers, rotate at the palm, and rotate at the wrist. The whole thing weighs only about 100 grams (3.5 oz), although each actuator in it is designed to support over 1,000 times its own weight.
The research is described in a paper that was recently published in the journal Science Robotics.
Source: Istituto Italiano di Tecnologia