The extraordinary Hadrian X bricklaying robot rocks up to a building site looking like a regular truck, then extends a 32-m (105-ft) boom arm and starts precisely laying up to 300 large masonry blocks an hour. It's pretty remarkable to watch.
We've had our eye on this Australian bot since it was an excavator-mounted prototype back in 2015. Even then, it was capable of laying the brick framework for a full-sized home in about two days – some 20 times faster than human bricklayers, according to Fastbrick Robotics, now known as FBR and the creator of the robot.
Now, in 2023, it's starting to roll out commercially. FBR has built its first "next gen" Hadrian-X system, and last month it set a new speed record on its first outdoor test build, demonstrating a sustained rate over 300 USA-format masonry blocks per hour on a testing and calibration run.
Extrapolate that rate to the largest blocks it can handle – 45-kg (99-lb) monsters measuring 600 x 400 x 300 mm (23.6 x 15.7 x 11.8 in) and you're looking at a machine capable of putting down some 70 sq m (753 sq ft) of vertical wall every hour – that's about a quarter of a tennis court. Oh, and FBR actually expects it to get a lot faster; its rated top speed is 500 blocks per hour.
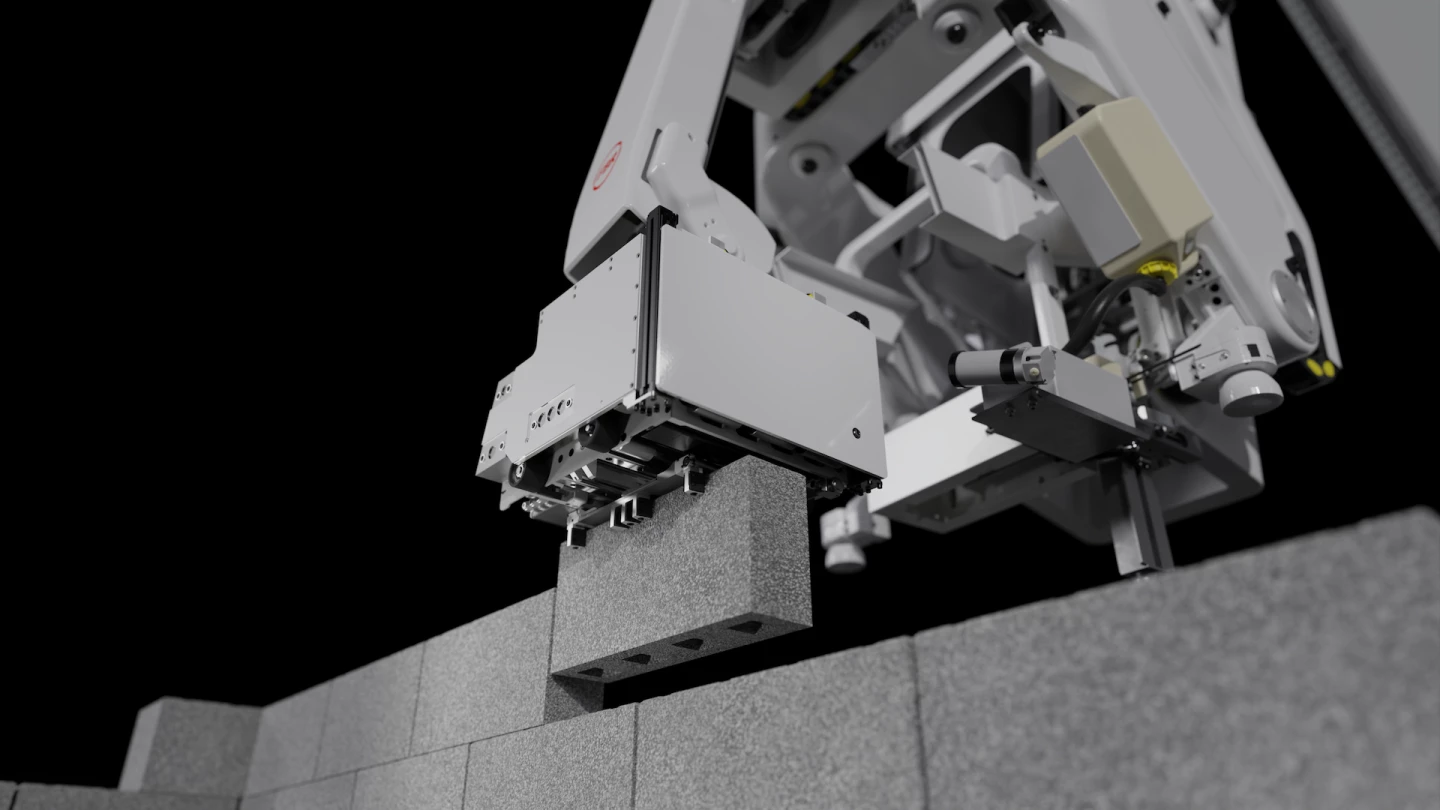
Arriving on site, the Hadrian X is operated by tablet, and will lay bricks with precision according to a CAD plan. Workers feed masonry blocks into the back of the truck by the pallet load, whereupon "dehacker" robots unpack them and cut them to size if necessary using a circular saw.
Then they're sent one by one down the middle of the boom arm on little shuttles, painted with a special construction adhesive in place of mortar, and laid down in place, where they're dry and secure within 45 minutes.
The Hadrian X's telescoping boom arm is long enough to build three-story structures from street level without a ladder to be seen, and it can work 24/7, apparently under most weather conditions.
As for the final result, well, FBR's first outdoor test build as shown in the video below might result in some harsh words from an employer – take a look around the 1:08 mark, where the lighting shows some clear inaccuracies in brick placement. But given that this was literally the first testing and calibration run for the next-gen robot, we'll assume that's not likely to remain a problem for long.
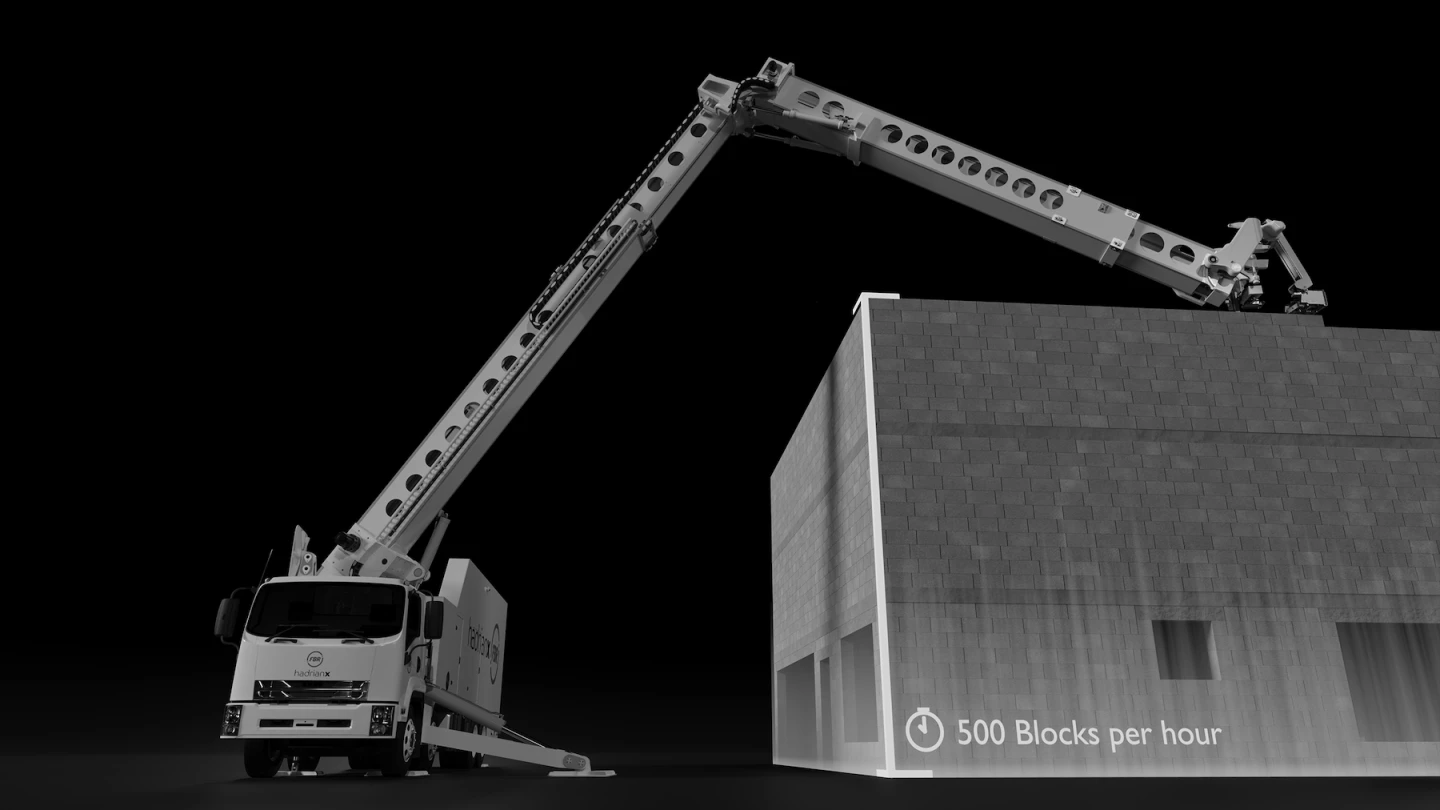
FBR has second and third robots under construction, and the first and second will soon be sent to the USA to run demonstrations, and to get straight to work in FBR's Florida-based "Wall as a Service" business.
Check out the record-breaking first test of the new system below.
Source: FBR