We’ve been following the progress of the Hadrian X bricklaying robot since it first started flexing its giant telescopic arm back in 2015, and have seen the team behind it make a few notable improvements since. We are now seeing what this type of machine can bring to the real world, with the robot completing the walls of its first display home as part of residential development in Western Australia.
The Hadrian X robot is the handiwork of Australia firm Fastbrick Robotics (FBR), and lays its bricks by way of a telescopic boom that mounts to an excavator or truck. By feeding the system a 3D CAD model of a house, the robot can then go to work placing bricks, along with the mortar and adhesive needed to hold it all together.
Not too long ago, the Hadrian X was capable of laying around 85 blocks an hour, but the team has made significant improvements to its control software that first saw that rate jump to 150 blocks an hour, and then last month to more than 200. This was considered a demonstration of the skills needed to compete with traditional bricklaying services, and now the team is seeing how its machine fares as part of a real-world construction team.
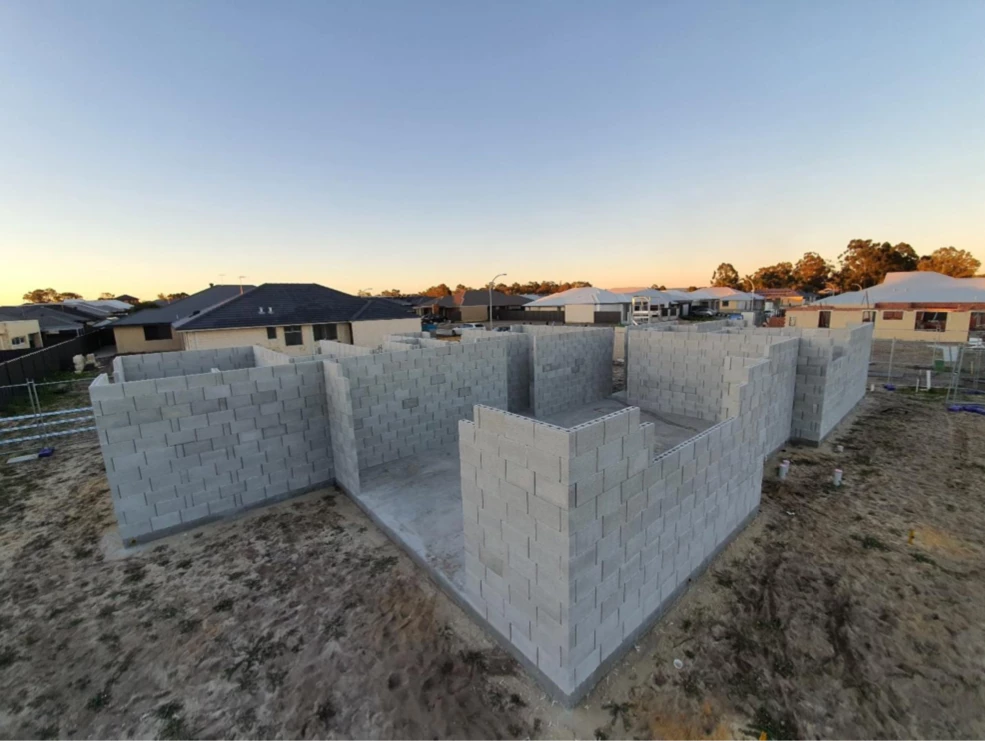
The company deployed the Hadrian X to the site of a display home, which will feature as part of a residential housing development in the town of Dayton. Here it completed the structural walls of the display home in three and a half standard bricklaying shifts, according to the team, and has now retreated to base to allow human builders to take the reins.
Once complete, the home will serve as a display for the public and potential partners to visit and learn more about the Hadrian X’s bricklaying capabilities and automated construction. The company plans to continue improving the technology to boost its performance even further.
“From here, we will review our performance and apply our learnings from this build as part of our continuous improvement program,” says FBR’s Chief Technical Officer, Mark Pivac. “Finishing ahead of schedule for our first build on a residential site is a pleasing result for the company. Following our review, we will calibrate the Hadrian X to handle larger blocks like FBR’s F-Block, which will allow the Hadrian X to build future structures approximately 25 percent faster.”
You can hear from the team and see the Hadrian X in action in the video below.
Source: FBR