Rubber and metal are usually thought to sit at opposite ends of the stiffness spectrum, but a new composite material developed at Iowa State University could switch from the flexibility of the former to the stiffness of the latter after being bent, twisted or squeezed.
To develop the material, the team built on work in "undercooling," a technique that lets metals remain in a liquid state at temperatures far cooler than when they'd usually solidify. Some of the same Iowa State researchers previously experimented with the stuff as a heat-free alternative to soldering.
In the new research, the team first exposed droplets of melted metal to oxygen, creating an oxidized shell around them that keeps them in a liquid form. These tiny bubbles of undercooled metals are then gently mixed into an elastomer material.
Those bubbles will break open when the rubber in which they're embedded is flexed, bent, twisted, squeezed or put under any other kind of mechanical pressure. The liquid metal flows out and fuses together, hardening to form a kind of metal mesh inside the rubber. In their lab tests, the researchers found the material would stiffen by up to 300 percent, allowing it to support up to 50 times its own weight.
"A device with this material can flex up to a certain amount of load," says Michael Bartlett, co-lead author of the study. "But if you continue stressing it, the elastomer will stiffen and stop or slow down these forces."
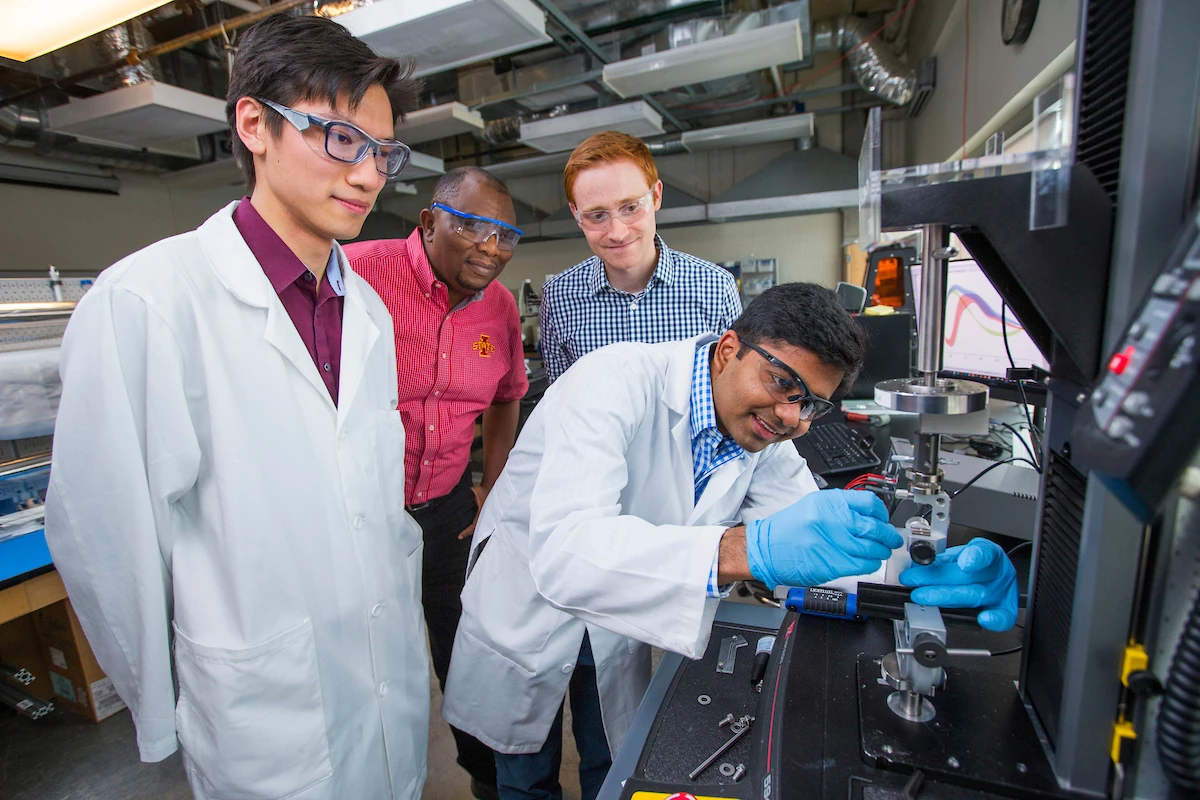
Judging by the technique, it sounds like a one-way street. Once it's metallic and hard, the material is not likely to return to its original rubbery state. Other stress-induced stiffness-switching materials aren't so permanent, like the one developed last year at the University of Michigan that used a unique surface geometry of struts and hinges.
Its stiffness may not be reversible, but the new material would still have plenty of applications. The researchers say it could be used to protect vital sensors or components of soft robots or wearable electronics, or to support delicate tissues in biological uses.
Since you don't necessarily want a rubber that will turn to metal at a sneeze, the researchers say the material could be tuned to withstand a certain amount of stress, and only harden up after a set threshold is crossed. This kind of tuning could be done by changing the metal inside the particles (currently a bismuth, indium and tin alloy), using different-sized particles or changing the soft material surrounding them.
The research was published in the journal Materials Horizons.
Source: Iowa State University