U.S. military uniforms may not be the most fashionable of clothes, but there are a lot of them. Every year, the Pentagon spends US$4 billion on uniforms and over 50,000 people are employed in their production. In an effort to cut costs and increase efficiency, DARPA has awarded a US$1.25 million contract SoftWear Automation, Inc. to develop “complete production facilities that produce garments with zero direct labor is the ultimate goal" - in other words, a robot factory that can make uniforms from beginning to end without human operators.
Robots have been used in the mass production of garments for decades, although this has mostly involved lasers cutting patterns in stacks of fabric or automated sewing machines carrying out very simple tasks. Machines in general and automation in particular have speeded up the making of uniforms, but it is still labor intensive. Worse, U.S. law requires that domestic sources be used whenever possible, so the costs are even greater than if the work was outsourced overseas.
Completely automating the process would allow for considerable savings, but garment making is one industry that has not easily lent itself to the introduction of robots. For one thing, fabric is very tricky to work with. It’s floppy, it folds, it creases, it crumples and the edges are often very irregular even if cut with a laser. At the same time, the pieces of fabric have to come together exactly right or stitches won’t go in properly, panels won’t match, buttons and holes won’t align and even something as simple as a zipper won’t work.
Worse, even something as uniform as a, well, uniform comes in a wide variety of shapes and sizes that need to be accounted for. Over the past 30 years, roboticists and engineers have sought solutions to these problems, but with only limited success and with few solutions that were cost effective.
Softwear Automation’s solution is to focus on the industrial sewing machine and working out how to modify it and add robotic support mechanisms to cover all aspects of garment making. Sewing machines require the fabric running through them to be kept at constant tension. Also, the floppy and irregular fabric needs to be properly positioned. The Softwear system does this by first using a standard “pick and place” robot to move the fabric from station to station.
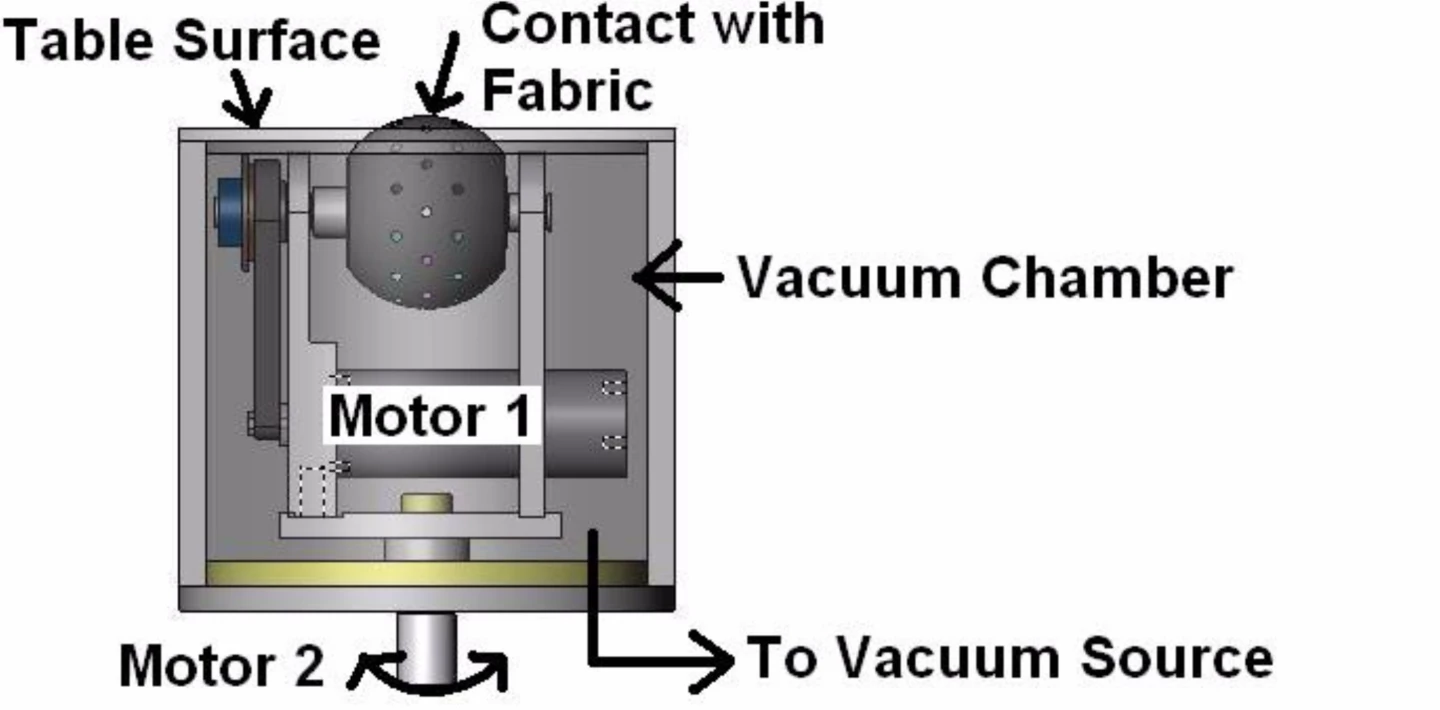
Once on the station’s sewing table, “budgers” come into play. These are robotic actuators made out of a hollow rubber ball with holes in it. These use a vacuum to “budge” the fabric into position. The sewing machine itself has a modified working head with servo-controlled dogs doing the work of an operator's hands to guide and maintain pressure on the fabric.
The key, however, is the imaging system that uses uses inexpensive, high-resolution cameras that weren’t available until now. This imaging system doesn’t use linear measurements like centimeters or inches. Instead, it counts the threads in the cloth to calculate position and distance with an algorithm taking into account fabric folding, thread flaws, and fabric edge irregularities. This imaging system and the robotics that it serves needs to be very fast because a human operator can make 5,000 stitches per minute, so there’s no time for the machines to pause and think.
The implications for a successful robot garment factory goes beyond trimming the U.S. military’s wardrobe budget. It also holds out the possibility of moving such jobs back to the developed world where robots would replace sweat shops. It also means that another class of unskilled labor would vanish along with so many others.
Sources:Federal Business Opportunities,Softwear Automation, Inc.,Proceedings of 2010 ISFA 2010 International Symposium on Flexible Automation (PDF)