After nearly 30 years of service, the Space Shuttle fleet is due to enter retirement with the last ever mission scheduled for takeoff on July 8, 2011. In its lifetime, the world's first Reusable Launch Vehicle (RLV) has provided information that will prove invaluable for the next generation of spacecraft that will succeed it. One such craft is the Skylon, an unpiloted, single-stage, reusable spaceplane currently under development by UK-based Reaction Engines Ltd. (REL). The Skylon got a shot in the arm last month with the release of a technical review of Skylon carried out by the European Space Agency (ESA) that concluded there are "no impediments" that would prevent the continued development of the Skylon and its SABRE engine.
The Skylon design, which grew out of the HOTOL (Horizontal Take-Off and Landing) program by Rolls Royce and British Aerospace that was terminated in 1988, consists of a slender fuselage containing propellant tankage and payload bay, with delta wings attached midway along the fuselage carrying the SABRE engines in axismmetric nacelles on the wingtips.
With a payload bay measuring 4.6 m (15 ft) in diameter and 12.3 m (40 ft) long, Skylon is designed to transport up to 15 tons of cargo into Low Earth Orbit (LEO, approx. 300 km /186 mile) at about 1/50th of the cost of traditional expendable launch vehicles, such as rockets. It could also carry 10.5 tons to a 460 km (286 mile) equatorial space station, or 9.5 tons to a 460 km x 28.5 degree space station, when operating from an equatorial site.
Skylon's fuselage and wing load bearing structure would be made from carbon fiber reinforced plastic, with the aluminum propellant tankage suspended within that is free to move under thermal and pressurization displacements. The external shell would be made from a 0.5 mm thin fiber reinforced ceramic that is corrugated for stiffness and free to move under thermal expansion. During re-entry, heat is radiated away from the hot aeroshell and prevented from entering the vehicle by layers of reflective foil and low conductivity shell support posts.
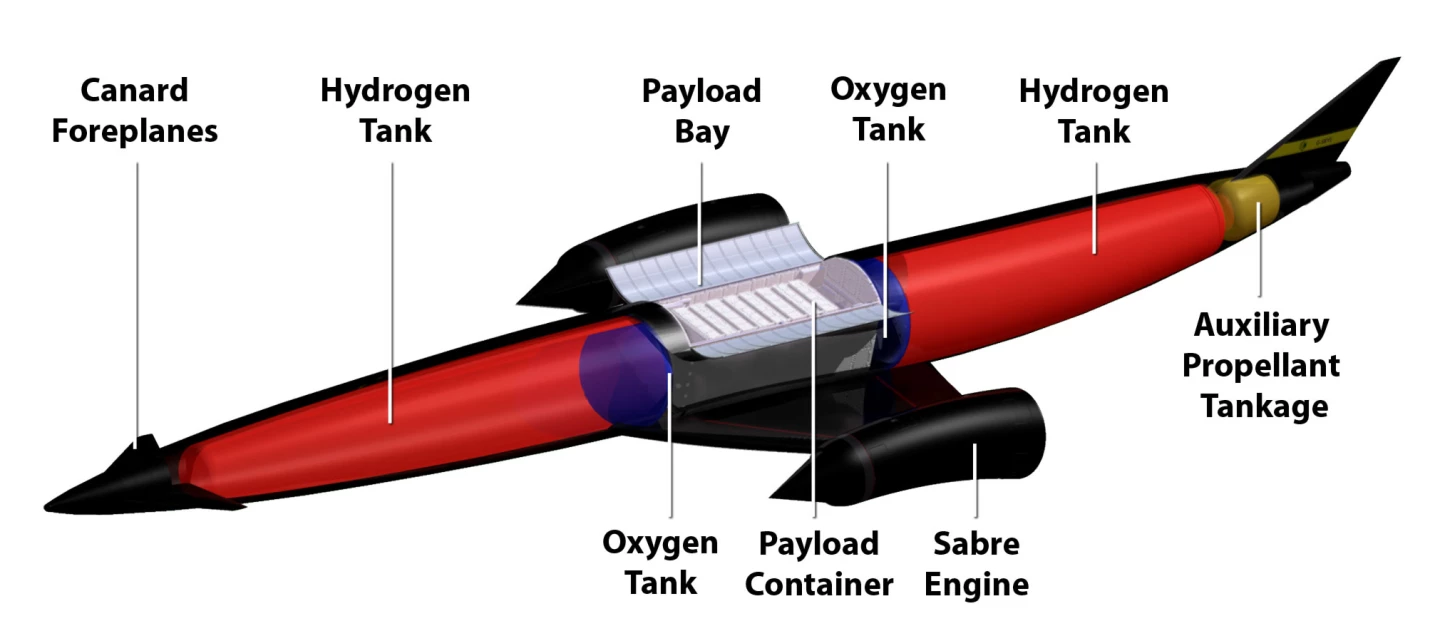
Unlike the Space Shuttles, which launch vertically with the majority of thrust provided by two solid rocket boosters that are jettisoned two minutes after liftoff, the Skylon takes off and lands horizontally on a (heavily reinforced) conventional runway courtesy of its SABRE (Synergistic Air-Breathing Rocket Engine) engines, which have a dual mode capability.
SABRE is not a scramjet like that being used in the X-51A Waverider, but rather a jet engine running combined cycles of a pre-cooled jet engine, rocket engine and ramjet. In air-breathing mode, which is employed from takeoff to when the spacecraft reaches Mach 5, the SABRE engines use atmospheric oxygen in place of liquid oxygen in the combustion process with stored liquid hydrogen. This reduces the quantity of oxidizer that a vehicle is required to carry, thereby enabling a single-stage to orbit (SSTO) spacecraft.
Once Skylon hits Mach 5 at 93,500 ft, the engine switches to a closed cycle using stored liquid oxygen and liquid hydrogen from the on-board fuel tanks. Under this pure rocket propulsion, Skylon is able to reach orbital velocity of around Mach 25.
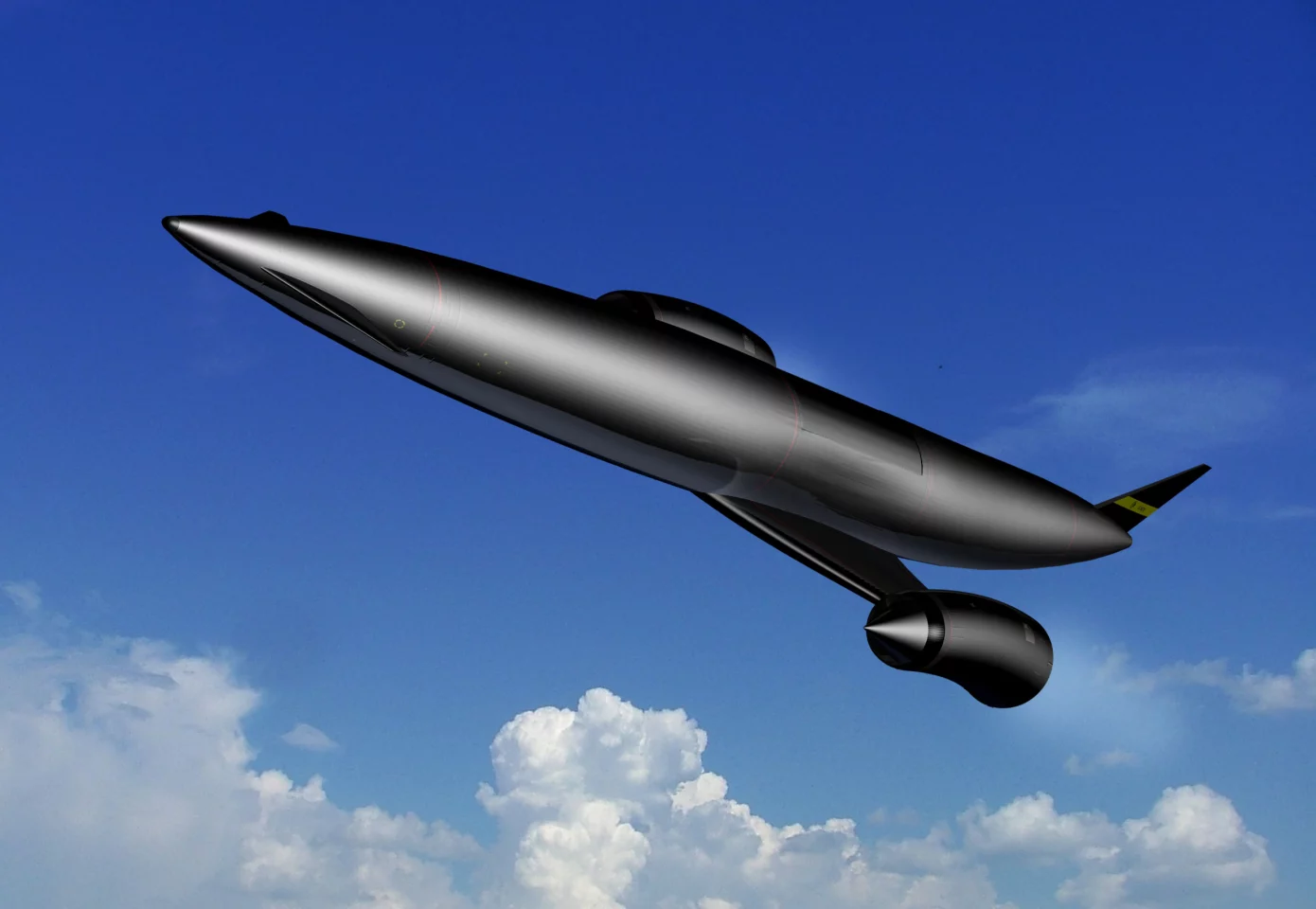
REL's ambitious aim of 10 years development time for the Skylon received a shot in the arm last month when the UK Space Agency's technical assessment on the Skylon, for which the ESA was commissioned, was released. The report stated that the SABRE engine and Skylon vehicle can be developed with "today's current technology," and that, "no impediments or critical items have been identified for either the Skylon vehicle or the SABRE engine that are a block to further developments".
The technical assessment process comprised two parts. The first was a series of visits by ESA technical teams to review designs and tests of component performance, while the second was a Skylon System Requirement Review that saw almost 100 international aerospace experts pose questions and make comments on the proposed spacecraft's technical and economic feasibility.
Calling the review a success, REL is looking to demonstrate its heat exchanger technology later this year before moving onto Phase III of the program. The total cost of the program is about US$10 billion, but REL says Skylon will be able to repay its development costs, meet its servicing and operating costs and turn a profit for its operators whilst being an order of magnitude cheaper to customers than current space transportation systems.
The UK Space Agency's Skylon technical assessment produced by the ESA can be downloaded here.