Magnesium alloys are very attractive for a range of weight-sensitive applications. They have the largest strength-to-weight ratio of the common structural metals, are lighter than aluminum and are particularly favored for being easy to machine and for their ability to be die cast to net shape. Unfortunately, magnesium alloys tend to corrode too easily. A team at Monash University in Australia has now discovered a novel and potentially game-changing approach to the problem: poisoning the chemical reactions leading to corrosion of magnesium alloys by adding a dash of arsenic to the recipe.
Magnesium alloys are of great interest as lightweight replacements for aluminum, titanium, and steel components in a range of transportation and aerospace applications. However, such alloys corrode easily, and this often prevents their use as replacements for noncorroding metals, particularly in applications requiring high reliability over a range of environments. As a result, the use of magnesium alloys at present is less than a million tons per year, while nearly 50 million tons of aluminum alloys are used each year.
Research and development carried out over the past decade have solved certain problems presented by magnesium alloys. Their tendency toward high-temperature creep was tamed by inclusion of scandium and gadolinium, and their flammability has been greatly reduced by introducing a small amount of calcium into the mix.
Corrosion resistance in magnesium alloys has not improved to the same degree. The main discovery is that the presence of iron, nickel, copper, and cobalt in a magnesium alloy strongly activates corrosion. This is due to their low solid solubility limits (meaning that above a very small percentage they precipitate out as intermetallic compounds within the alloy structure) and the fact that they have the right electrochemistry to behave as active cathodic sites that reduce water while causing the loss of magnesium from the alloy.
If a magnesium alloy has small enough quantities of these metals, it will have improved corrosion resistance. Also, the presence of iron can be overcome by the presence of a larger amount of manganese. Maintaining such precise control over the composition of structural magnesium alloys, unfortunately, forces the price skyward, and doesn't really solve the corrosion problem.
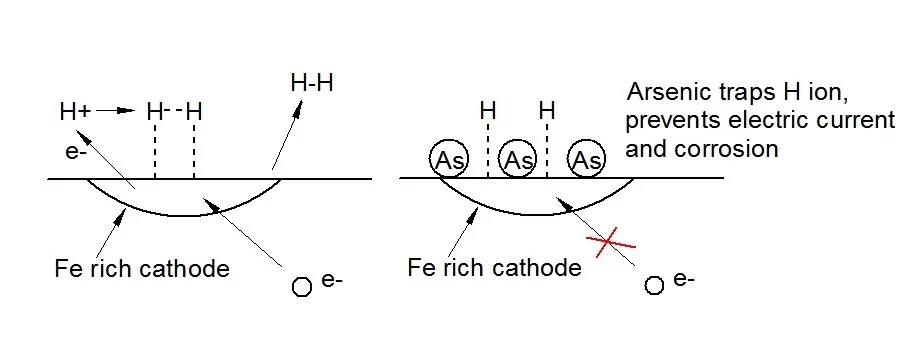
Led by Associate Professor Nick Birbilis, the Monash team attempted to apply an additive known as a cathodic poison to a standard magnesium structural alloy. Cathodic poisons act by capturing atomic hydrogen within the structure of a metal. This prevents the formation of free hydrogen gas which is required to balance the corrosive chemical processes. A number of alloying elements, including arsenic, antimony, sulfur, selenium, and tellurium, are known to act in this manner in other alloy systems.
The result was that addition of about one-third of a percent of arsenic to the magnesium alloy reduced its corrosion rate in a salt solution by a factor of nearly ten. In this initial study the intent was to prove the principle of the use of cathodic poisoning. Prof. Birbilis' lab is currently working with corporate sponsors on developing a series of commercially practical stainless magnesium alloys.
"This is a very important and timely finding," says Prof. Birbilis. "In an era of light-weighting for energy and emissions reductions, there is a great demand for magnesium alloys in everything from portable electronics to air and land transportation. Magnesium products are rapidly evolving to meet the demands of industry, but presently are hindered by high corrosion rates. The arsenic effect we discovered is now being trialed as a functional additive to existing commercial alloys. Our breakthrough will help develop the next generation of magnesium products, which must be more stainless.”
Considering the enormous impact of stainless steels on our society, the game-changing potential of stainless magnesium is clear.
The University of Wales and CSIRO also took part in the research, the findings of which are published in the journal Electrochemistry Communications.
Source: Monash University