Concrete has been around for millennia, but that doesn't mean we can't cook up new ways to build with the world's favorite construction material. It's been electrified to melt snow and used as an "ink" in 3D printers to quickly print entire buildings. Now, engineers at ETH Zurich have developed a more efficient method for building with the material, erecting an ultra-thin, curved prototype roof that's 5 cm (2 in) thick on average, and designed to support energy-saving systems in the building.
Although it's since been dismantled to make way for other test structures, the prototype stood 7.5 m (24.6 ft) tall and was ultra-thin, measuring 12 cm (4.7 in) at its thickest and just 3 cm (1.2 in) at the edges. It had a surface area of 160 m2 (1,722 sq ft) and covered an area of 120 m2 (1,292 sq ft), and that discrepancy was down to the fact that the roof arched over, forming shapes that concrete normally wouldn't be capable of without complex support structures.
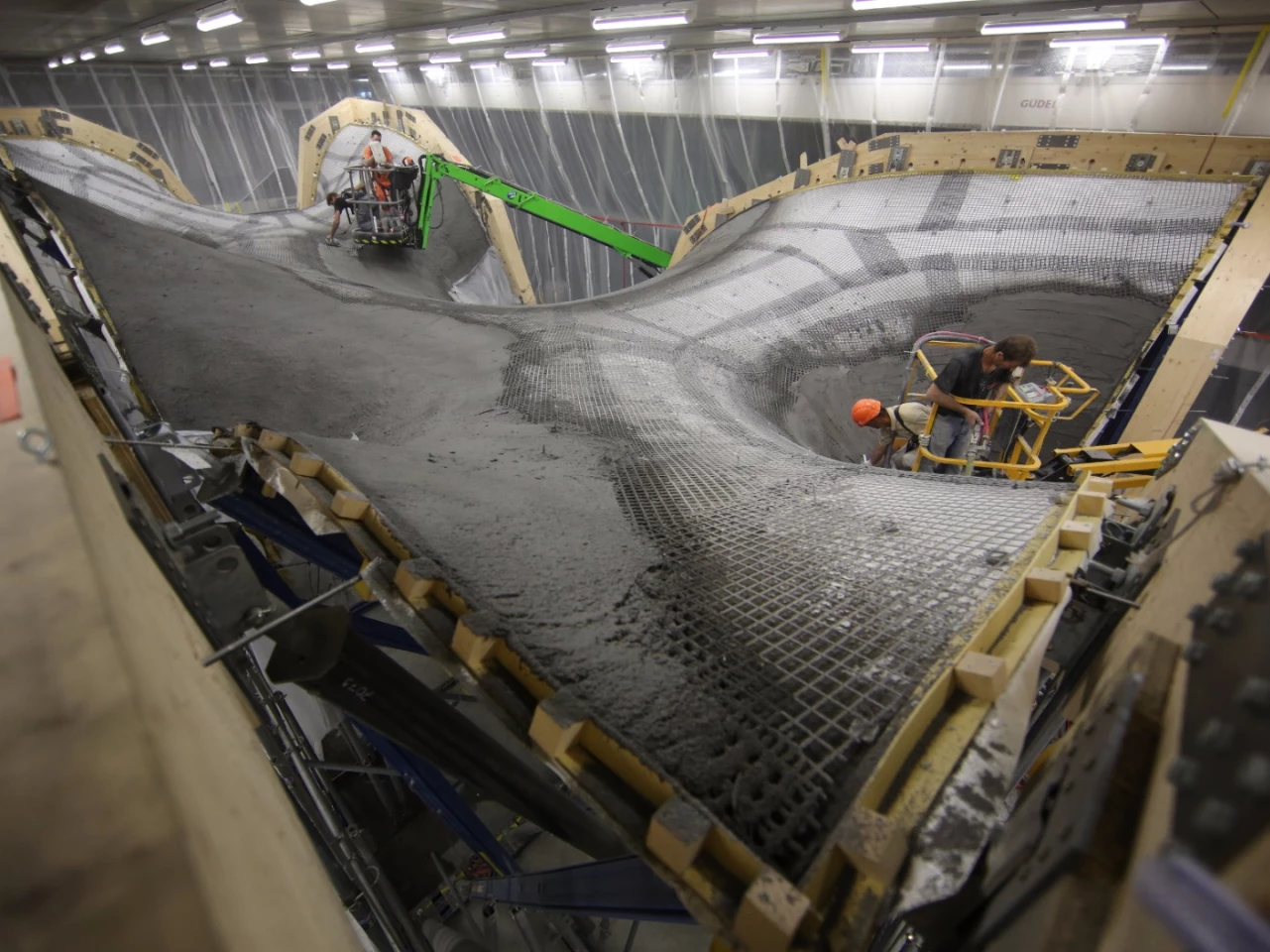
Instead of using custom-built, single-use wooden or foam scaffolding, the engineers tested a new technique of their own design. A net of steel cables was stretched into the desired shape, and a polymer textile was laid over the top to create a flexible formwork. The shape was controlled by algorithms that distribute the force evenly between the cables and determined just how much concrete needed to be applied to each section. Afterwards, the cable net can be dismantled, reused and reshaped as needed.
Altogether, some 20 tons of wet concrete were supported by 500 kg (1,102 lb) of steel cable and 300 kg (661 lb) of textile. Further tweaking went into how the cement was made and applied to the support structure. The mixture needed to be just right – thick enough that it would stick to the vertical surfaces, but runny enough that it could be sprayed on, using an application method that was specially designed for the project.
The prototype concrete shell was designed to cover a residential rooftop apartment called HiLo, which will be built next year on the top floor of the NEST lab in Dübendorf, Zurich, Switzerland. The roof is designed to help out with HiLo's energy-neutral goals: inside the ultra-thin covering, insulation and heating and cooling coils were sandwiched between two layers of concrete, and that's capped off with thin-film photovoltaic solar cells.
After four years of prep work, this practice run took over six months to set up, and next the researchers are shooting to build the same structure at NEST in eight to 10 weeks.
"We've shown that it's possible to build an exciting thin concrete shell structure using a lightweight, flexible formwork, thus demonstrating that complex concrete structures can be formed without wasting large amounts of material for their construction," says Phillipe Block, led researcher on the project. "Because we developed the system and built the prototype step by step with our partners from industry, we now know that our approach will work at the NEST construction site."
Source: ETH Zurich