A number of groups have already developed so-called "electronic skin," which adds electronic functionality to a user's natural skin. A new magnetic take on the technology, however, does away with the need for integrated electronics and power sources.
Created by a team at Saudi Arabia's King Abdullah University of Science and Technology (KAUST), the material consists of a highly-flexible biocompatible polymer that's mixed with magnetized microparticles. Via an "inexpensive and simple" process, it's manufactured in thin sheets that are temporarily adhered to a user's own skin.
Once the magnetic skin is in place, nearby sensors are able to detect the changes in its magnetic field as the body part in question moves around. In lab tests, for instance, the skin was applied to a test subject's eyelid, and then monitored by an adjacent multi-axis magnetic sensor.
That sensor was consistently able to determine if the eyelid was open or closed. Down the road, such functionality could lead to the technology's use in applications such as human-computer interfaces for the disabled, the analysis of sleep patterns, or the monitoring of driver alertness. In those cases, the magnetic sensor could be built into eyeglass frames, a sleep mask, or even an electronic tattoo applied to the forehead.
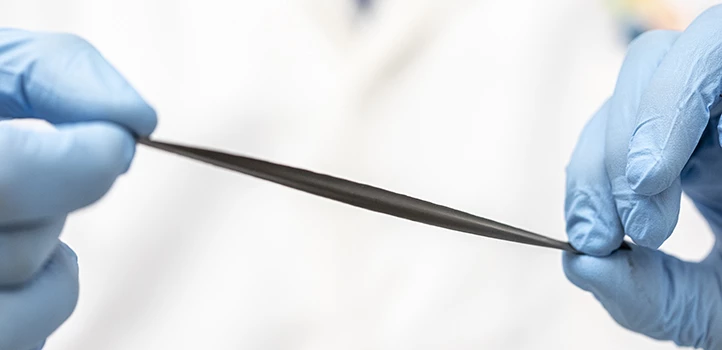
The researchers also applied the magnetic skin to the fingertip of a latex glove, which could then be used to turn a magnetic sensor-equipped light switch on and off without touching it. Among other things, this setup could find use in places where contamination is a concern, such as laboratories and medical settings. A gesture-control system for electric wheelchairs is additionally in the works.
"Artificial electronic skins typically require a power supply and data storage or a communication network. This involves batteries, wires, electronic chips and antennas and makes the skins inconvenient to wear," says Assoc. Prof. Jurgen Kosel, leader of the project. "Our magnetic skin does not require any of this. To the best of our knowledge, it is the first of its kind."
A paper on the research was recently published in the journal Advanced Materials Technologies.
Source: KAUST