These days it seems the term architecture has broadened to encompass fantastical projects and shapes in the virtual domain. Interdisciplinary design studio MammaFotogramma hope to go someway towards bridging worlds real and virtual through the development of a flexible wood surfacing material named WoodSkin, which, being CNC-friendly, lends itself to all sorts of abstract forms.
WoodSkin is a sandwich of plywood triangular tiles with a textile mesh in between. The production process takes a composite nylon and polymer mesh and encases it between sheets of Finnish plywood, all of which are glued together using a custom mixed adhesive. A three-part compression process then strengthens the material to support its movements. The sandwiched materials are cut into small modules by a CNC mill that creates the 3D pattern and breaks up the rigid surface.
Adaptation to project requirements is key to WoodSkin’s ethos. Users can specify the triangle size, geometry and density within the sheet, as well as the thickness of wood ranging between 4 and 30 mm (0.15 and 1.18 in). WoodSkin is available in modules, sheets or rolls and has the ability to be linked together to form large continuous surfaces. When building your product, stability is achieved through the bends and folds or in some cases insertion of supporting struts. To complete a design, different finishes or waterproofing can be applied, and the company is exploring how it can offer different surface materials without breaking the industrial production process.
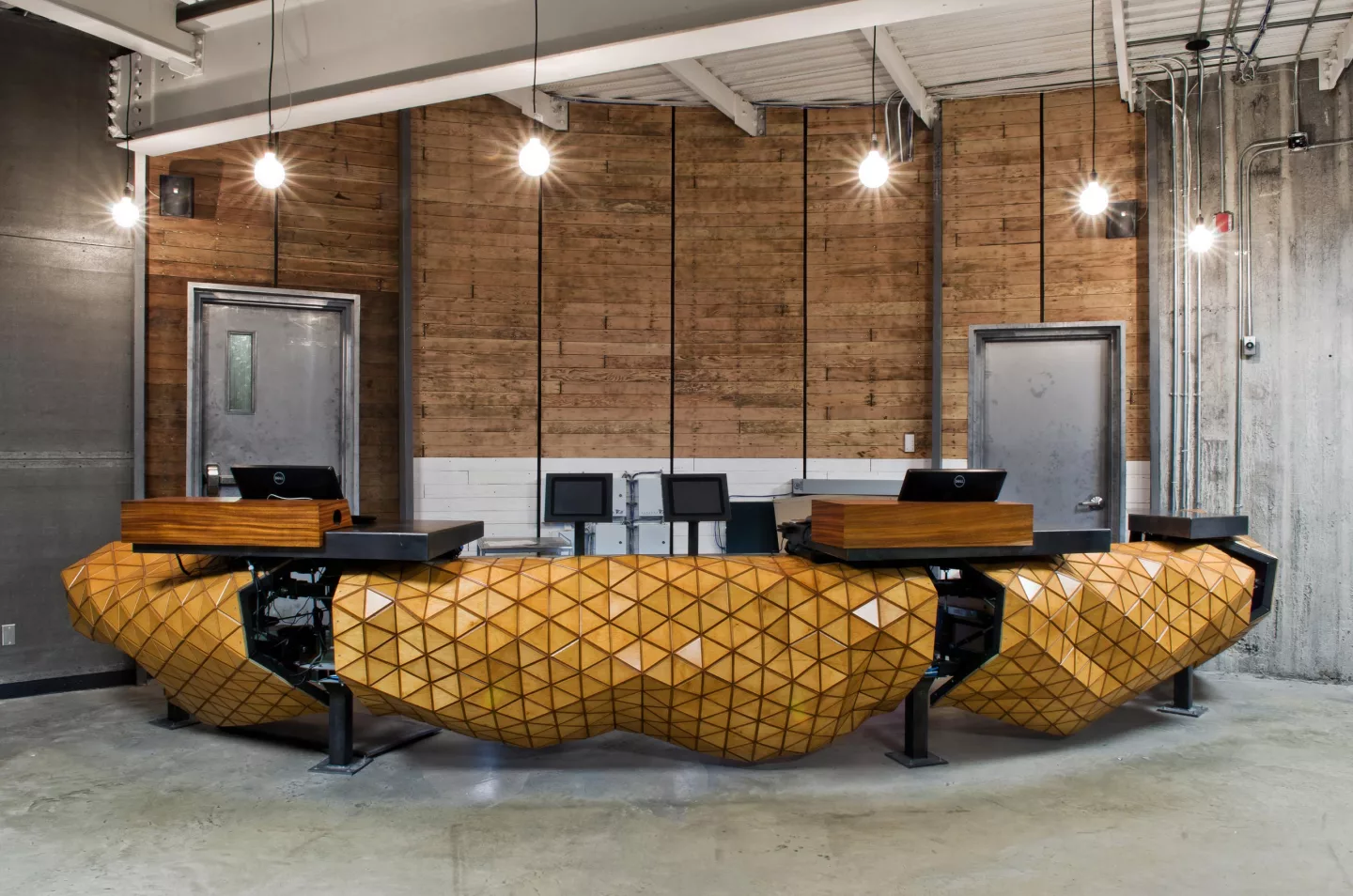
The end result MammaFotogramma hope, is a product that can emulate the meshes and points of computer aided design yet still be applicable to the panels and screws of everyday construction. The team is developing a custom plugin for 3D software package Rhino to assist with the design process and enable users to realize their desired shape at different sizes, materials and contexts.
WoodSkin began as a response to the Autoprogettazione 2.0 open-source design competition in 2012, and has a patent pending following its successful application at a climbing wall in Montreal. From here MammaFotogramma hope to continue product development and define new possibilities of flexibility in architecture and design.
The video below demonstrates the WoodSkin product.
Source: MammaFotogramma via ANBlog