On Saturday, a tunnel boring machine (TBM) so large that it looks like something out of Thunderbirds was dedicated in the city of Seattle. “Bertha,” as it’s known, is the world’s largest TBM and will spend the next 14 months boring a 1.7 mile (2.7 km) tunnel under the city as part of a US$3.1 billion project to replace a viaduct damaged in a 2001 earthquake. As part of a press tour, the Washington State Department of Transportation (WSDOT) allowed New Atlas inside the giant machine.
The first thing that hits you when encountering Bertha is its sheer size. At 326 ft (99.3 m) long and 57.5 ft (17.5 m) wide, its 7,000 tons (6,350 tonnes) of steel and machinery fill most of the 80-ft (24.3-m) deep launching pit where it was assembled. If seeing wasn't enough, the descent into the pit down an eight-story open scaffold stairway drove the scale home for New Atlas’ acrophobic correspondent. A glance at the brownish water trickling between the seams of the temporary steel and concrete retaining walls of the enormous trench showed that we were well below the local water table.
Led by KaDeena Yerkan, Manager for Communications and Public Involvement on the Alaskan Way Viaduct Replacement Program, the tour consisted of half a dozen members of the Fourth Estate tricked out in hard hats and high-visibility vests, several trailing formidable camera rigs. Despite it being a weekend, the pit was a hive of activity as workers went about the intricate business of putting together the last pieces of Bertha.
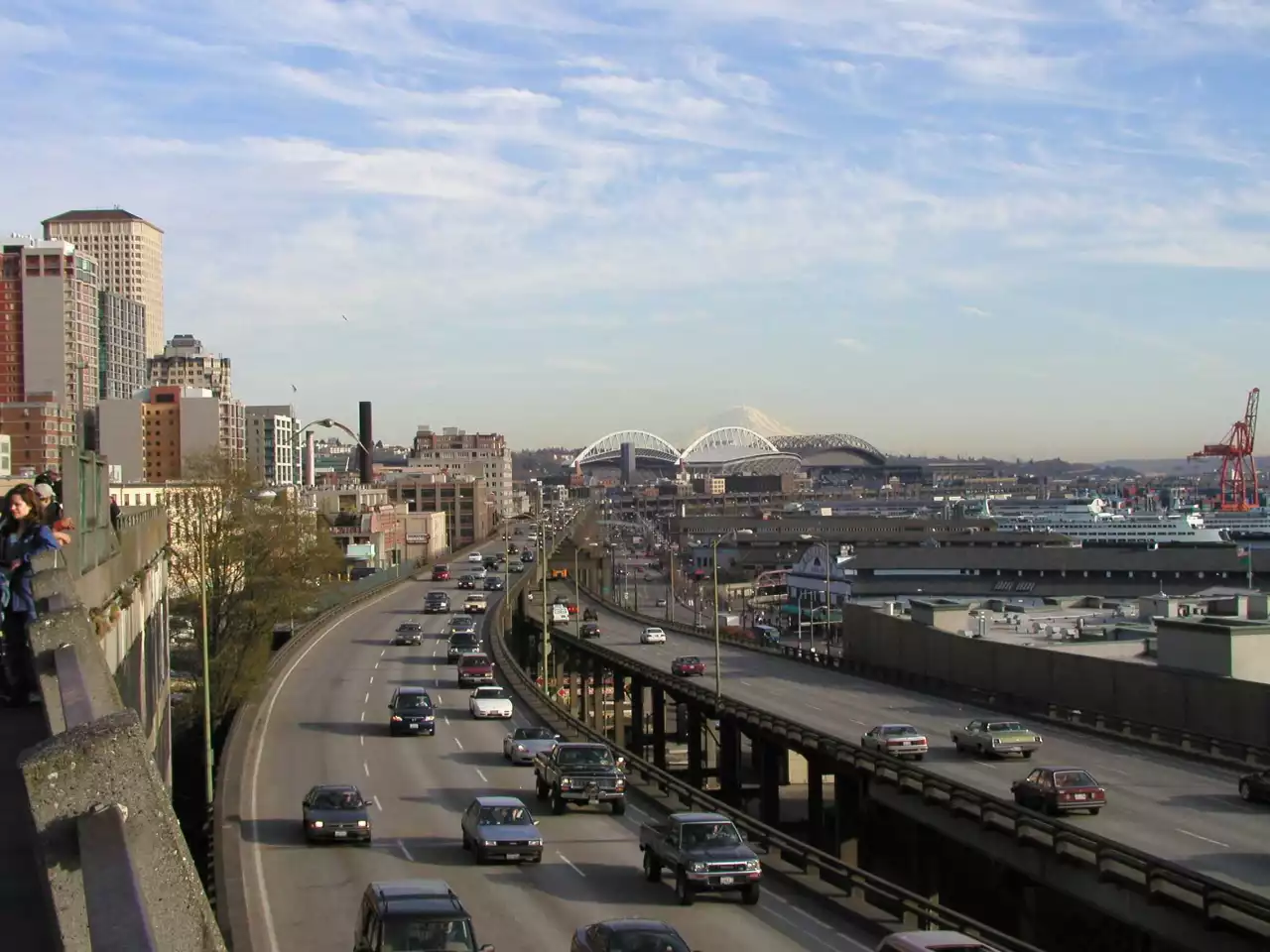
Above the pit, we could see and hear the reason for all this activity. Bertha’s job is to dig the replacement for the SR 99 Alaskan Way Viaduct, which skirts around the Seattle waterfront. Built in the 1950s, it’s a reinforced concrete double-decker highway carrying 110,000 cars daily and for over half a century it’s been loved and hated by local residents. To some, it’s a chance to enjoy beautiful views of Puget Sound during the daily commute. For others, it’s a concrete monstrosity hovering over the waterfront and cutting it off from the city.
From viaduct to tunnel
Those opinions became moot on February 28, 2001, when an earthquake measuring 6.8 on the Richter scale struck the Puget Sound region, causing 400 injuries, one death by heart attack and a considerable amount of damage to older buildings, many of which had to be demolished. A massive effort was made to retrofit the area’s bridges with new concrete collars to reinforce them against future tremors, but the Alaskan Way Viaduct was badly damaged. Though it was repaired and most of it remains in use (the southern end was demolished recently as part of the tunnel project), engineers determined that the basic design was much too light and that its foundation on pilings floating in the soil was too unstable. The fear was that another earthquake could cause the viaduct to pancake, as happened in 1995’s Great Hanshin earthquake in Japan.
Over 90 alternatives were considered by WSDOT, ranging from replacing the old viaduct with a new one to a cut-and-cover tunnel, but the final plan was to dig a tunnel away from the waterfront and under the city center at a depth of 200 ft (61 m) to avoid a forest of pilings, cables and pipes from the some 160 buildings above. Bertha and the buildings above are both monitored to detect any significant movements. The planned tunnel itself is a double-decker four-lane highway with room at the sides for utility lines and emergency pedestrian walkways.
Because of the width of the tunnel and the peculiar nature of the soil on which Seattle is built, a specially designed and constructed TBM was required for the job. Custom built and tested in Japan by the Hitachi Zosen Corporation, Bertha took over a year to build before being broken into 41 pieces and shipped from Japan aboard the Jumbo Fairchild to Seattle, where it was unloaded using special cranes with reassembly starting in April of this year. Its name was selected in a competition by the students of Poulsbo Elementary School and is in honor of Bertha Knight Landes, who was elected mayor of Seattle in 1926.
As we entered Bertha, I understood why we were offered earplugs. Even at rest, it’s a cacophony of noises, though it isn't like being on a factory. There’s no sense of being in a building filled with machinery, nor is it like a train or a ship. Though it moves, it isn't a vehicle. It’s a solid mass of machinery designed to process and move soil. The overwhelming sense was that we were crouching, (and in a couple very low spots spots that was almost literally true), through a huge engine made up of gigantic moving parts keeping a frightening amount of power that is very close by at bay.
The cutterhead
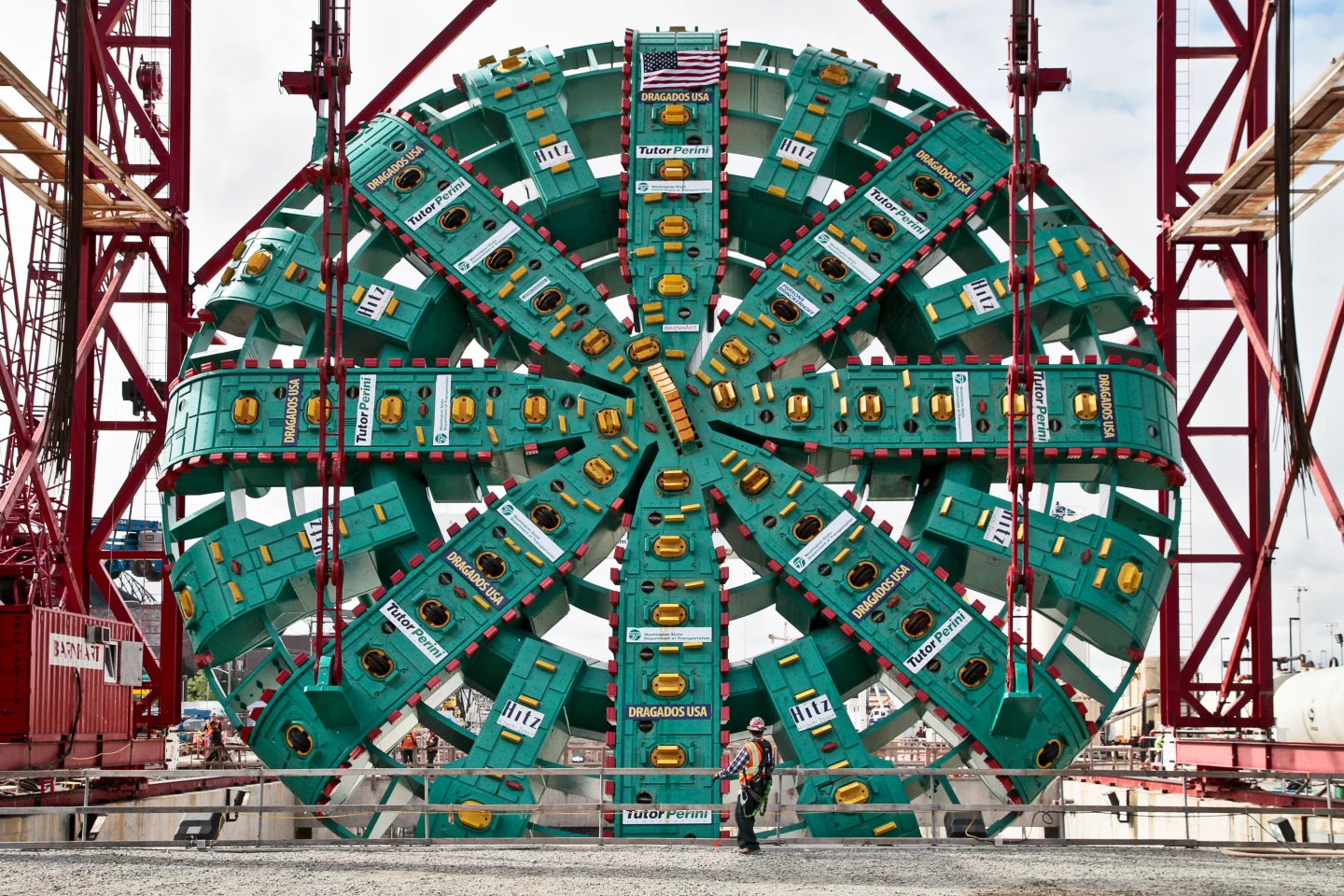
At the very front of the TBM is the cutterhead. We didn't get this far from the inside, though we could see it from the top of the pit. It is possible to get that far forward from the inside, though that’s reserved for those unlucky enough to draw the short straw at making repairs, replacing worn cutters, or cutting up any unusually large boulder that gets wedged in the workings. It’s particularly nasty duty because once underground, that means entering a muck-filled space between the cutterhead and the rest of the machine in a bubble of compressed air.
The cutterhead covers the entire front of Bertha and rotates to bring its 260 teeth into play. These teeth are specialized cutters with each designed for a specific role. Some teeth are designed to break up soft soil. Others collect the soil and guide it through gaps inside the cutterhead, while others are grinders intended to chew up large boulders.
Tunnel boring isn’t an easy job. The TBM uses 25,000 bhp (18,600 kW) and moves at a speed of about 35 ft (10 m) per day. Though the system is largely automated, Bertha still needs 25 people at a time to keep it going. One reason why Bertha was custom built is that Seattle sits on an extremely varied collection of eight different soils left behind by glaciers during the last ice age. This soil is so varied that it isn't even expected to be the same across the span of the cutterhead.
The slurry pipe
The boring operation isn't just a matter of chewing up soil. It also requires getting the soil out of the way without the tunnel collapsing or flooding. Bertha does this by injecting water and other chemicals into the broken soil until it turns into a soft paste slurry, which is collected behind the cutterhead. Here the machine maintains a constant pressure on the trapped soil. If there’s too little, the slurry just churns inside the cutterhead and the front face of the tunnel could fall in. Too much and the machine is pushing a wave of slurry ahead of itself.
However, the key purpose is to reduce the pressure of the slurry to that of the normal atmosphere when it leaves the space behind the cutterhead. Otherwise, the results would be messy. "If it was the same pressure when it got to the back of the machine, it would be shooting all over the place," says a project engineer.
The shield
Directly behind the cutterhead is the shield. It’s a huge steel cylinder that holds up the sides of the tunnel wall and protects the machinery and workers from muck and water. As it bores, Bertha crawls like an inchworm with the shield creeping forward and the rest of the TBM rolling up behind. The design is very old. having been invented by Marc Isambard Brunel and used by his son Isambard Kingdom Brunel to dig the first tunnel under the Thames at Wapping in 1825. The principle is still the same, though instead of machines, Brunel used men digging through little windows in the front of the shield and the tunnel was lined with hand-laid brickwork.
Inside the shield are the bits for powering the cutterhead, shifting the soil, lining the tunnel, and controlling Bertha. As we entered one of the forward-most compartments of the shield, we had to duck past the slurry pipe, which is a massive steel tube running at an angle from floor to ceiling that just begs you to hit your head on it.
Inside the pipe is a screw conveyor that collects the slurry and sends it back inside the machine. The screw is an open steel ribbon with a gap in the center from front to back that allows boulders up to 3 ft (1 m) in diameter to pass. In all, it’s expected that 850,000 cubic yards (650,000 cu m) of soil will pass through the pipe before excavation is completed.
The slurry is deposited on a conveyor belt and is then sent offsite to the waterfront where it’s loaded onto barges that transport it to Port Ludlow, where it will be used to reclaim an old gravel pit. When we saw it, the conveyor was a small add-on in the back of Bertha’s launching pit all coiled up on itself like a package of snakes, but as Bertha moves forward, the conveyor belt will stretch out from tunnel workhead to freight terminal until it’s over 9,000 ft (2.7 km) long. Also trailing behind are thousands of feet of cables and hoses carrying power as well was chemicals and water to Bertha both for drilling and to cool the machinery and other hoses to carry back reclaimed water.
The shield itself is self-propelled and drags along the rest of Bertha as it advances. Inside the back rim are hydraulic jacks that push it forward as the machine cuts. In addition, there are other jacks used to align and steer the shield. The tunnel is lined with 2-ft (0.6-m) thick concrete panels or segments. The rams bush against the forward-most ring of panels and inches forward like a worm. An indication of the force used can be seen in the huge steel brace in the launching pit, which the rams will shove against when Bertha starts its journey. After that, its job is complete.
Lining the tunnel
The arms of the jacks form a ring inside the shield and it’s here that the concrete lining of the tunnel is assembled. The lining rings are made of ten concrete panels and each ring weighs 360,000 lb (163,000 kg). The panels are lined with rubber gaskets to keep water out and some panels are shorter than the standard size to allow the tunnel to curve in certain sections.
An overhead conveyor system brings the panels from the rear of the TBM and into the shield. Here, two erector arms take the concrete panel segments two at a time and as the jack arms retract, the erectors place the panels against the shield hull. Bolts and dowels are used to lock each panel in place and the panels are laid in a staggered pattern for greater strength. Having two erector arms is unusual for a tunneling machine and allows it to operate at twice the speed in lining the tunnel.
When the ring is completed, the jacks push against the ring and the shield moves forward as the cutterhead resumes boring and exposes the new ring. The outer surface of the ring where the shield once was is pumped full of grout to stabilize the tunnel wall and make it waterproof. Then the sequence repeats.
Also inside the shield is the control room. This consists of a computer panel that allows the operators to monitor all of Bertha’s systems, supervise operations by means of video cameras, steer the machine, and watch out for any indications of the earth shifting unexpectedly or if the cutterhead comes up against a boulder too big for it to handle. It usually has two people at the controls and definitely was never designed for half a dozen reporters and cameramen fighting for a clear shot while balancing voice recorders in the other hand.
Directly behind the control room is a break room, which was the most spacious and normal looking area we saw on the tour. At the moment, it seems a bit of a luxury with the amenities of downtown Seattle a two minute walk away, but once drilling commences it will be better than eating lunch perched on a ventilator fan housing.
Trailing gear
Articulated and resting on massive rollers, 300 ft (91.4 m) of Bertha is the trailing gear section, which is sort of the digestion system for Bertha’s head. It supplies the machine with grout and grease, and contains the pumps and ventilation equipment as well as restrooms, a kitchen for the crew, and a rear control room to handle the section’s operations.
One of its most important functions is to collect the concrete panels. These panels are loaded at the tunnel mouth by gantry crane and carried ten at a time on a small electric railway car called a Segment Transport Truck. When the truck reaches the trailing gear, it enters through a special passage and an overhead trolley uses suction to pick up each panel, turn it 90 degrees, and send it forward into the shield and the waiting erector arms.
The inside of the trailing gear section is so cramped and complicated that it was easy to get lost just looking at it, never mind navigating through it. Headroom is at a premium, as I learned when by hardhat went flying after encountering a pipe. It isn't simply a matter of the number of machines, but the necessity of mounting them all inside a latticework basket of steel beams and then sticking the whole thing on wheels. In fact, the wheels are a bit unnerving. Looking down, you expect to see the girders ending in plates bolted to a flat floor. You don’t expect bogies resting on a curved surface that will one day carry over 100,000 commuters to and from work.
Dedication
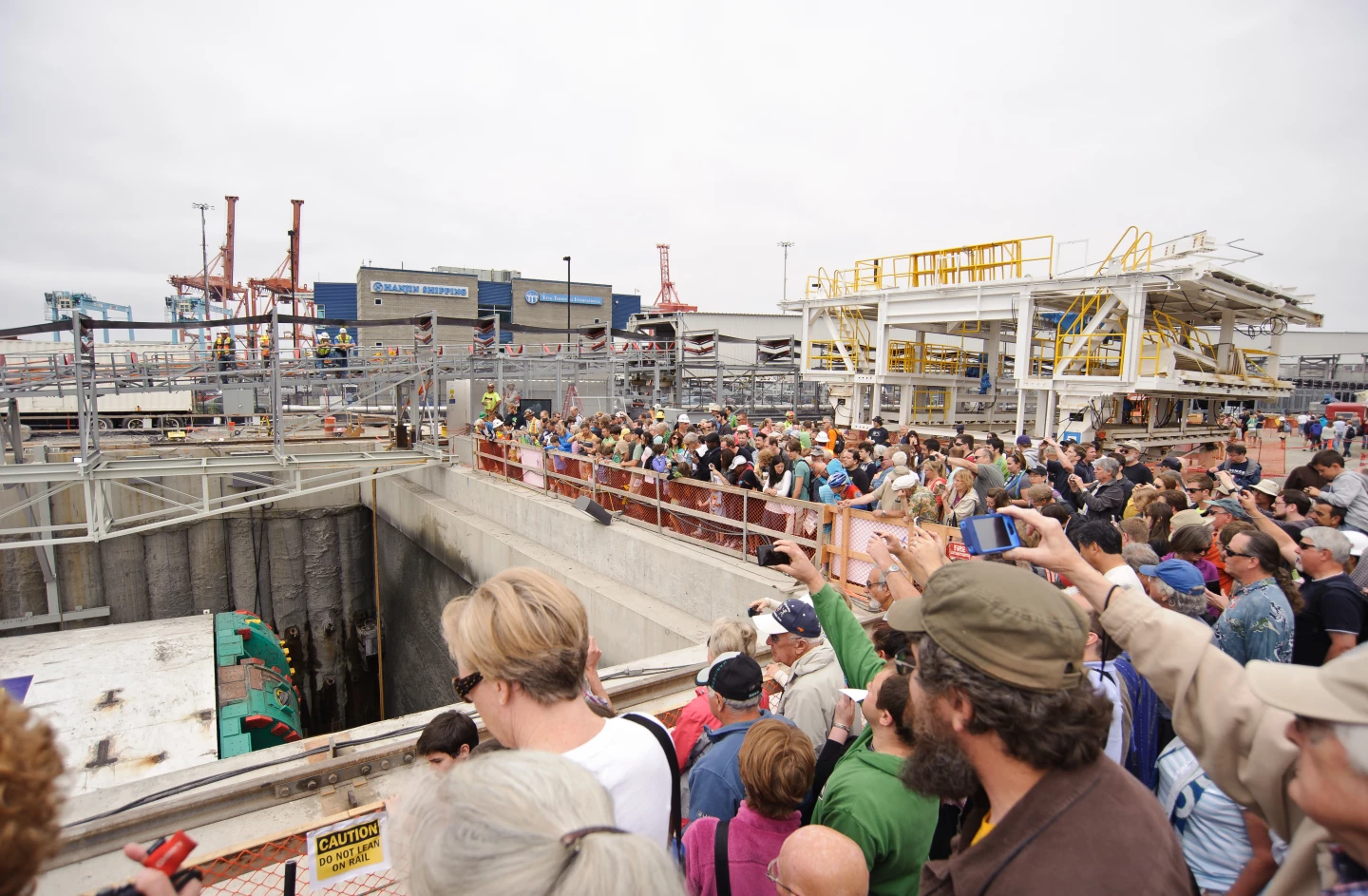
After the press were cleared out of Bertha and the pit, there was a dedication ceremony to formally christen Bertha that was attended by 5,000 members of the public at the tunnel site. Project staff talked to the public, who were invited to sign their names on a tunnel segment and were allowed to see Bertha from the top of the pit.
“This is a historic day,” said Washington State Governor Jay Inslee. “When I look down into this pit, I don’t just see a big machine. I see determination, I see innovation, I see teamwork, I see a symbol of a community that worked together to move us forward.”
Drilling is scheduled to begin at the end of this month with the boring operation expected to be completed in 14 months and the new highway opened in 2015. Bertha, however, is too valuable to be put on display or abandoned in a side tunnel, as happened to one of the machines that made the Channel Tunnel. The TBM will be broken up and some parts sold back to Hitachi.
The animation below shows how Bertha works.
Source: Washington State Department of Transportation